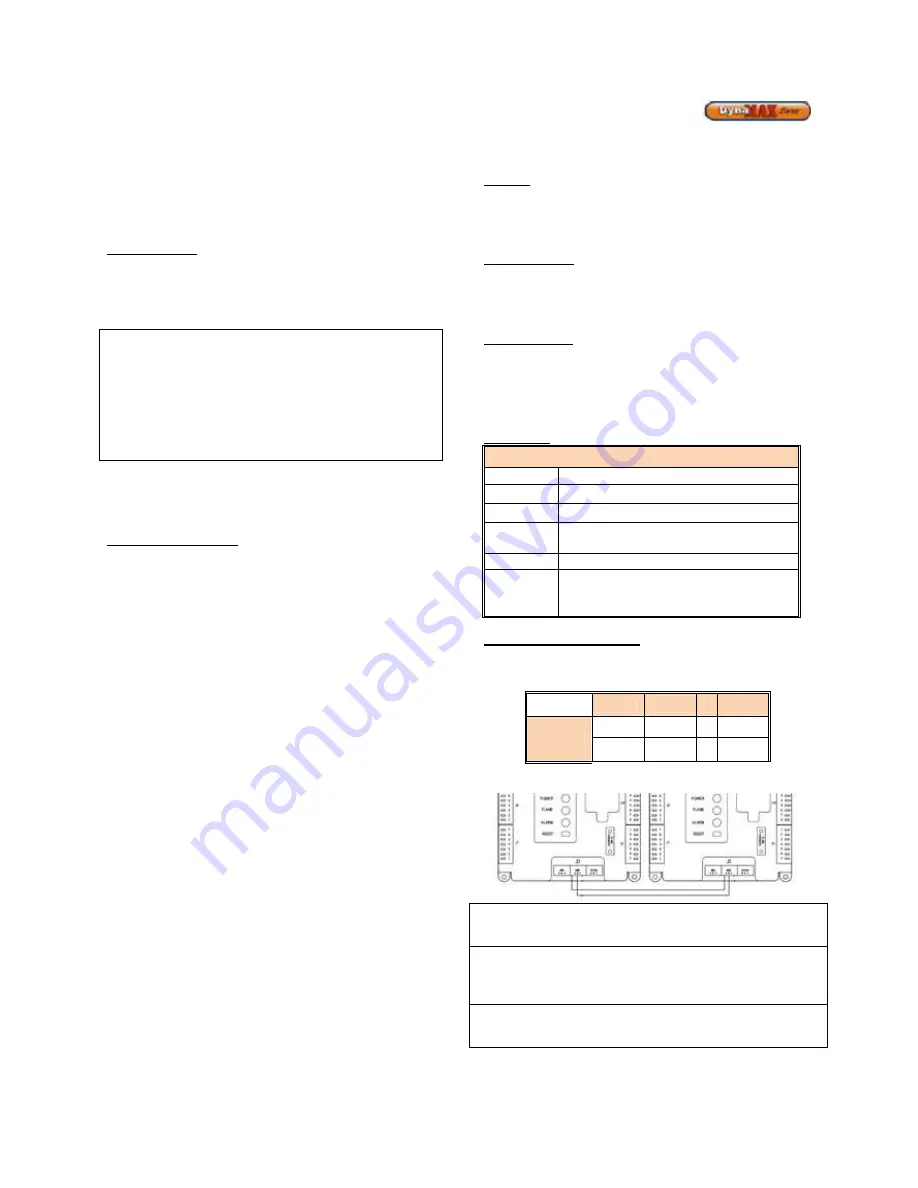
58
10.11 LEAD LAG SETUP
The following components are needed for a Lead Lag setup
1) 10k
Ω
System Sensor
Turn off all the boilers before beginning the setup process.
To setup the DynaMax HS lead lag system follow the
instructions:
System Sensor
Insert the supplied 10k
Ω
system sensor into the building
loop. The wires coming out of the system sensor should be
connected to pin#5 and #6 of the green DynaMax HS
terminal board.
NOTE
The use of a system sensor is required in lead lag
operation.
1) When variable speed main circulators ARE NOT used
the system sensor is to be placed into the return
system piping.
2) When variable speed main circulators are used the
system sensor is to be placed into the supply system
piping.
All SOLA controllers are programmed with a default
address of 1. The address of the slave controllers in the
system must have a unique address (1..8).
Sequence of Operation:
When a boiler is set as Lead Lag Master = Enabled and
Modbus address = 1, the controller of this boiler will drive
the lead lag operation.
The outdoor temperature sensor connected to the slave
boiler 2 (ie. B-2) will be the outdoor sensor for the lead lag
system
•
The system temperature sensor connected to
boiler 1 in terminals labeled “Outdoor System
Sensor” on the terminal board will be the control
sensor for lead lag operation.
•
The start/stop signal connected to boiler 1 at
terminals labeled “Remote Operator” will be the
heat demand input for lead lag operation.
When demand for heat is present the lead boiler will start
and uses the lead lag parameters for boiler modulation.
After a period of “Interstage delay” the master boiler
compares the lead lag temperature with the lead lag set
point and will check if:
1) An additional boiler is needed
Lead lag < Lead lag setpoint – Add stage Error
threshold
2) Number of boilers remain the same
Lead lag > Lead lag setpoint – Add stage Error
threshold AND
Lead lag < Lead lag se Drop stage Error
threshold
3) A boiler should stop
Lead lag > Lead lag se Drop stage Error
threshold
If the lead lag master system is interrupted the remaining
boilers will operate as standalone boilers based on the
Central Heat or DHW parameters when set to “Enabled”.
Rotation
Rotation time is configurable based on equalized run time.
For a fixed rotation schedule refer to Additional boiler
parameters section on page 33 of this manual, parameter
#575 & 733.
Interstage Delay
The length of time to wait between requesting a slave boiler
to fire and detecting that it has failed to start. (Default: 2
minutes). Access to this parameter is outlined on page 33
of this manual, parameter #722 and 731.
Base Load Rate
When a call for heat is initiated the lead boiler runs at the
desired base load rate (Default: 80%) and continues to
operate in this fashion based on the above 3 scenarios. If
the lead lag temperature is not satisfied a second boiler is
fired at they would both operate at 80% fire rate.
Slave State
Slave Status Manager
Unknown
Table entry is unused or empty
Available
Slave is operational and ready to use
Add Stage
Stage is getting ready to fire
Suspend
Stage
Stage was getting ready but is not needed
Disabled
Slave is locked out or disabled
Recovering
Slave is in time delay to verify that it is
operational before considered to be
available
Wiring the Lead Lag Setup
Use lead lag terminals on the terminal board to wire lead
lag appliances
Master
Slave 2
..
Slave 7
J3, MB2
A
A
..
A
B
B
..
B
Figure 33: Lead lag Wiring Setup (Left: Master, Right: Slave)
NOTE
Recycle power on all boilers after programming is complete if
lag boilers are not discovered automatically
NOTE
CH Setpoint or DHW Setpoint must match Setpoint located in
Lead Lag Master Configuration in order for the system to
operate correctly.
NOTE
The Local/Remote switch (explained below) must be set in the
“Local” position on ALL lag boilers.
Summary of Contents for DynaMax DMH081
Page 2: ......
Page 68: ...65 PART 14 EXPLODED VIEW PARTS LIST DYNAMAX HS WALL HUNG...
Page 69: ...66 DYNAMAX HS FLOOR MOUNT...
Page 76: ...73 PART 15 ELECTRICAL DIAGRAMS 15 1 DM 80 299 INTERNAL WIRING DIAGRAM...
Page 77: ...74 15 2 DM 399 800 INTERNAL WIRING DIAGRAM...
Page 78: ...75...