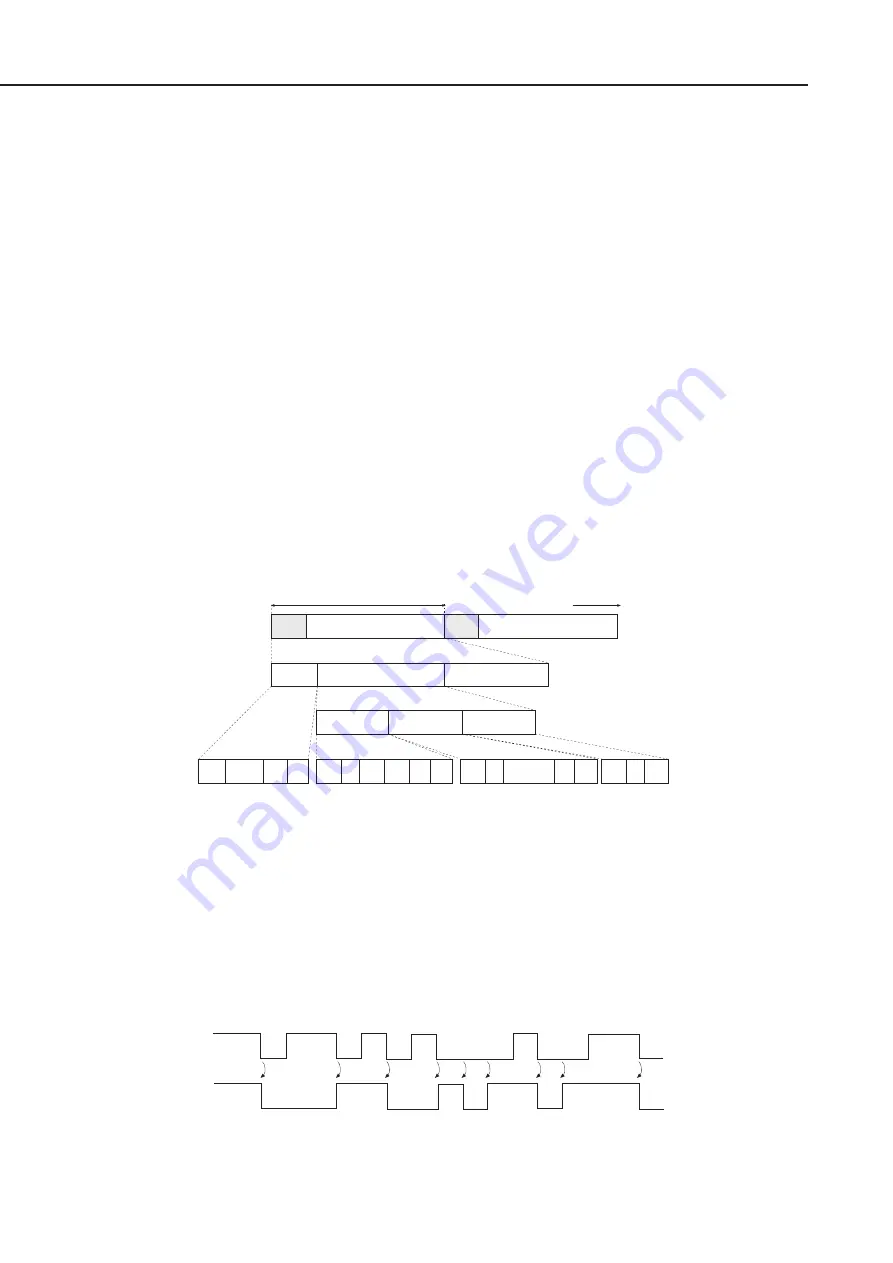
1.3.3 USB interface
USB is a serial interface which connects up to 127 peripheral devices to a host
computer, and transmits data at a high-speed rate of 12Mbps. Hot plugging, in which
connecting/disconnecting devices while the host or the printer is in use, is supported.
Each device is connected to a hub's port, where each port's detection/disconnection
status is returned to the host.
Data transfer
The data transfer in USB is executed in terms of the transfer unit called a frame, a
time frame of approximately 1ms, into which the data is divided. Data is transferred
by piling up these frames.
All packets begin with a SYNC (synchronizing) field to synchronize with the local
clock, and are separated with an EOP (End of Packet) field.
Frame lines begin with an SOF (Start of Frame) packet. An SOF is composed of a PID
(Packet Identification Field) that represents the type of the packet and the direction,
frame number, and a CRC (Cyclic Redundancy Check) used for error-check.
Inside a frame is a packet line containing a token packet, data packet and a
handshake packet, which indicates the status of the flow control.
A token packet is composed of a PID, an address field which can specify up to 128
addresses, an ENDP (endpoint) field, and a CRC.
Inside a data packet are a PID, data field, CRC, and EOP.
Only a PID is present inside the handshake packet.
Encoding/Decoding the Data
In USB, data transfer lines are ultimately encoded with NRZI (Non Return to Zero
Invert) method. When the original data bit is 0, sent data bits are inverted; when the
original data bit is 1, the value is retained.
However, if the level of the transferred data remain unchanged for a certain period of
time, the receiving side may not be able to synchronize with the data sample position,
which will result in data bits being out of phase. This is prevented by a method called
bit stuffing; when data bit 1 is repeated 6 times, one 0 bit is added to the original data
before encoded with NRZI.
Part 5: Appendix
BJC-3000
5-8
SOF
1 Frame (approx. 1ms)
SOF
Printer
Other Function
SYNC
Frame
Number
CRC
SYNC
Token
Data
Handshake
PID ADDR ENDP CRC
EOP
EOP
SYNC PID
DATA
CRC EOP
SYNC PID
EOP
SOF
Frame Line
Frame Structure
Packet Line
Packet Structure
Time Lapse
Idle
Idle
NRZI
0
1
1
0
1
0
1
0
0
0
1
0
0
1
1
0
Data
Figure 5-7 USB Data Transfer
Figure 5-8 NRZI
Summary of Contents for BJC-3000 Series
Page 2: ...0899 SC 0 30 0 ...
Page 3: ......
Page 12: ...VIII This page intentionally left blank ...
Page 14: ......
Page 28: ......
Page 48: ...Part 2 Maintenance BJC 3000 2 20 This page intentionally left blank ...
Page 50: ......
Page 62: ...Part 3 Operation BJC 3000 3 12 This page intentionally left blank ...
Page 64: ......
Page 88: ......
Page 95: ......
Page 112: ...Part 5 Appendix BJC 3000 5 24 This page intentionally left blank ...
Page 118: ......
Page 119: ...PRINTED IN JAPAN IMPRIME AU JAPON CANON INC The printing paper contains 70 waste paper ...