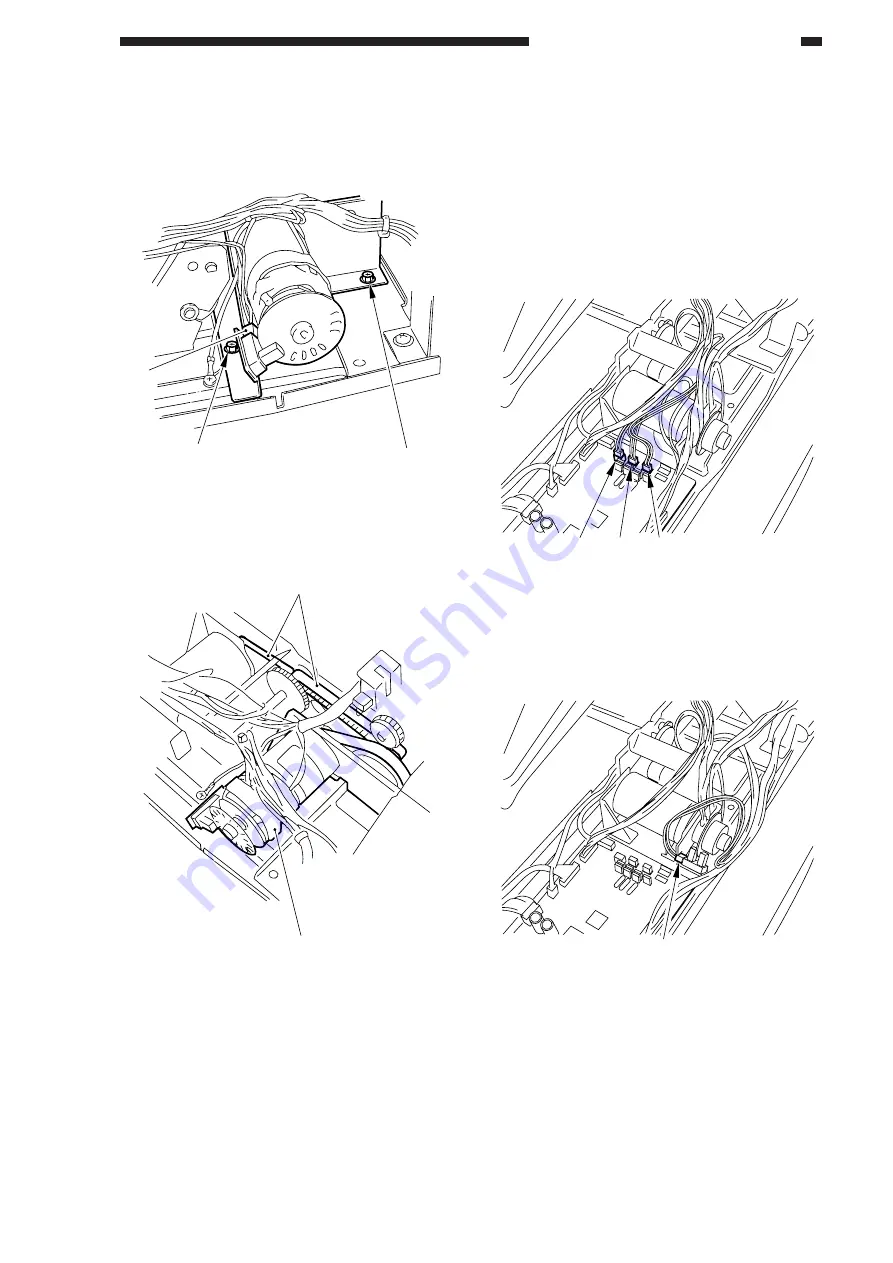
COPYRIGHT © 1998 CANON INC. CANON DADF-A1 REV.0 DEC. 1998 PRINTED IN JAPAN (IMPRIME AU JAPON)
3-7
CHAPTER 3 MECHANICAL SYSTEM
4) Remove the two screws [4], and
disconnect the connector [3] of the feeder
motor clock sensor S9.
[3]
[4]
[4]
Figure 3-205
5) Detach the two drive belts [5], and detach
the feeder motor unit [6].
[5]
[6]
Figure 3-206
C. Belt Motor
1.
Removing the Belt Motor
1) Remove the DADF from the copier.
2) Remove the feeder motor unit.
3) Remove the tie-wrap as necessary.
4) Disconnect the connectors J6 [1], J7 [3],
and J13 [3] of the DADF controller PCB.
[3]
[1]
[2]
Figure 3-207
5) Disconnect the connector [4] of the belt
motor clock sensor (S10).
[4]
Figure 3-208