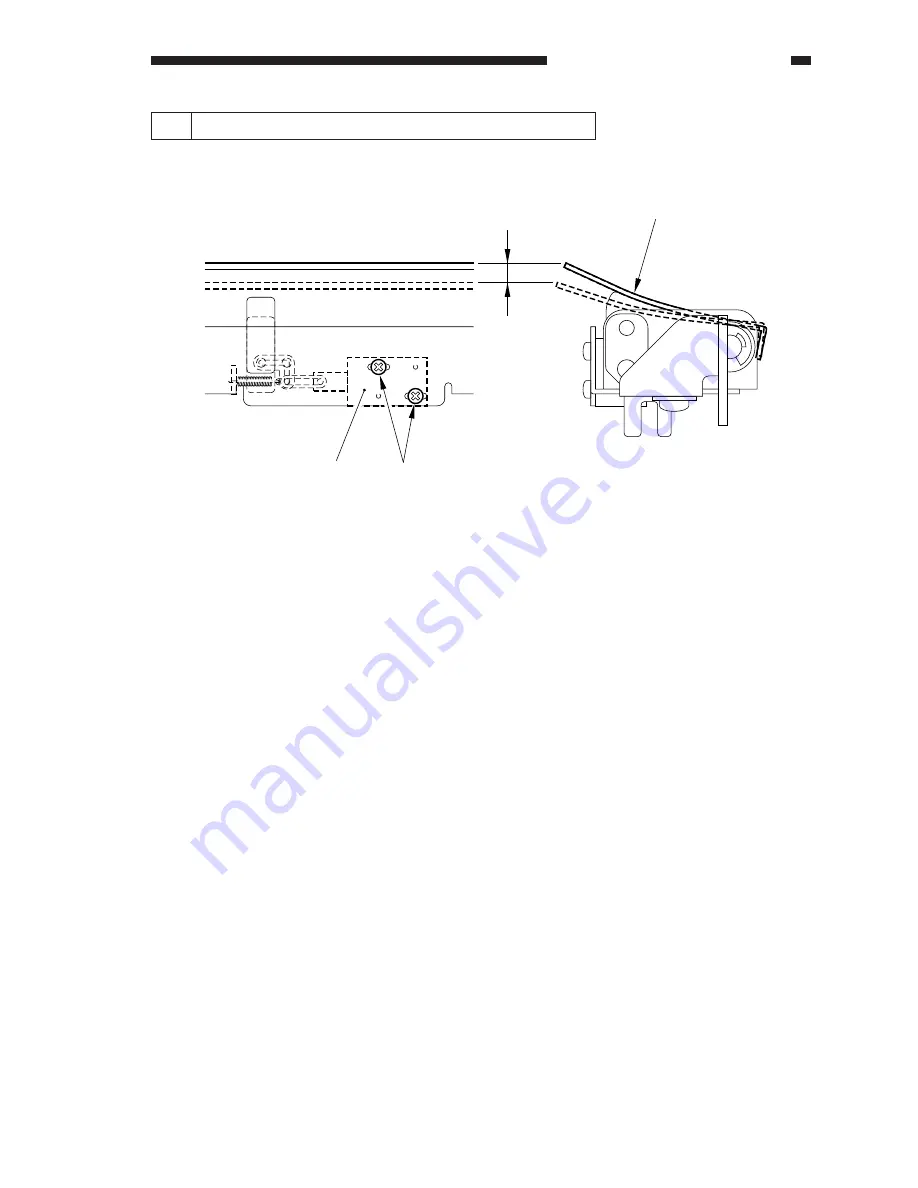
COPYRIGHT © 1999 CANON INC.
CANON GP605/605V REV.0 JAN. 1999 PRINTED IN JAPAN (IMPRIME AU JAPON)
13-25
CHAPTER 13 TROUBLESHOOTING
9.1
Position of the Fixing Inlet Guide Solenoid (SL1)
1.8mm
Guide
[1]
Solenoid (SL1)
Adjust the position of the solenoid using the screw [1] so that the guide will lower 1.8 mm
when the solenoid turns on.
Figure 13-D210
Summary of Contents for GP605
Page 3: ......
Page 4: ......
Page 24: ......
Page 56: ......
Page 78: ......
Page 116: ......
Page 124: ......
Page 148: ......
Page 150: ......
Page 168: ......
Page 170: ......
Page 250: ......
Page 252: ......
Page 342: ......
Page 390: ......
Page 392: ......
Page 464: ......
Page 466: ......
Page 512: ......
Page 514: ......
Page 572: ......
Page 574: ......
Page 590: ......
Page 592: ......
Page 854: ......
Page 870: ......
Page 874: ......