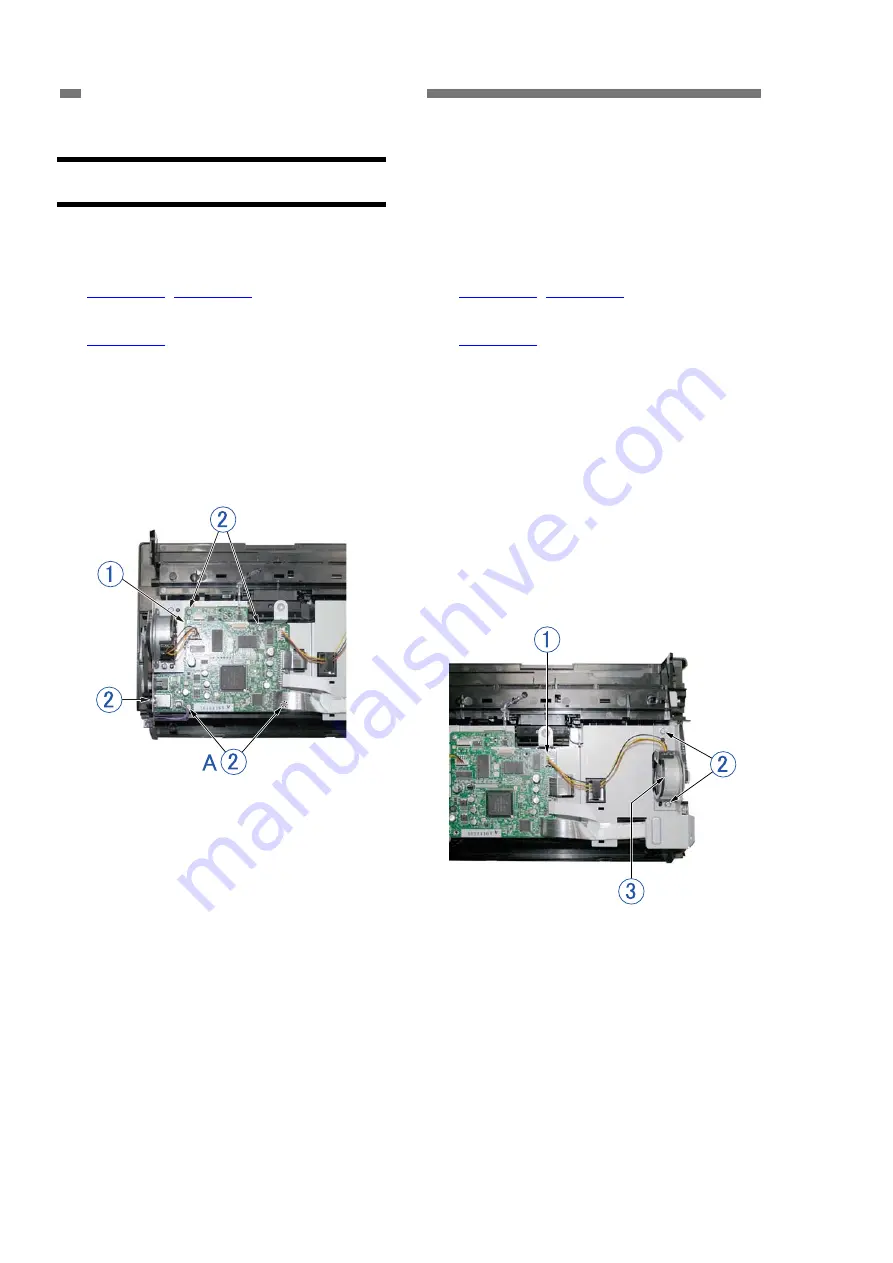
CHAPTER 3 DISASSEMBLY & REASSEMBLY
III. BASE UNIT
1. Control PCB
1) Remove the left and right covers.
2) Remove the rear cover.
3) Remove the 6 cables that are connected
to the control PCB
{
1
from the
connectors. Remove the 5 screws
{
2
(BH, M3) and remove the control PCB.
Note:
There are sensors mounted on the
back side of the PCB.
Figure 3-301
Notes on assembling
Since there are protrusions on the screw
unit marked A in the above diagram for
determining the position, place it into the
holes on the PCB. Do not forget to
tighten the screws for the USB
connector.
2. Feed Motor
1) Remove the left and right covers.
2) Remove the rear cover.
3) Remove the connector
{
1
and 2 screws
{
2
(TP, tapping, M3), and then remove
the feed motor
{
3
.
Note:
Once you have removed the motor,
the timing belt, pulley, and gear can
also be removed. The timing belt is
the same component as the timing
belt on the main motor side.
The motor is attached with the
mounting plate. Do not remove the
mounting plate.
Figure 3-302
3-8
COPYRIGHT
©
CANON ELECTRONICS INC. 2011 CANON DR-C125 FIRST EDITION