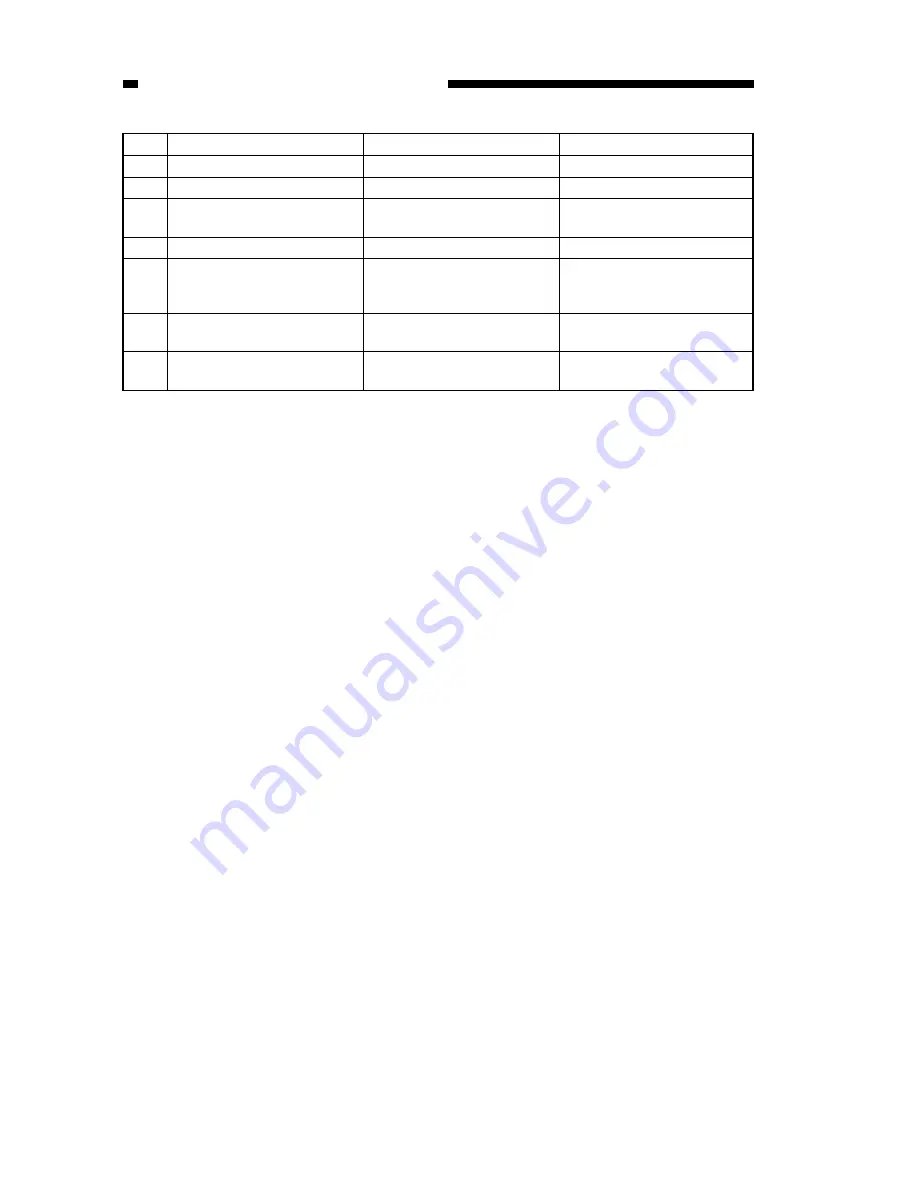
CHAPTER 13 MAINTENANCE AND SERVICING
13-4
COPYRIGHT © 1999 CANON INC. CANON imageRUNNER 400/330 REV.0 JAN. 1999 PRINTED IN JAPAN (IMPRIME AU JAPON)
No.
9
10
11
12
13
14
15
Work
Clean the copybook glass.
Make test copies.
Perform the Image Adjustment
Basic Procedure.
Make sample copies.
Put the sample copies in
order, and clean up the area
around the machine.
Record the final counter
reading.
Fill out Service Book, and
report to the person in charge.
Remarks
Checks