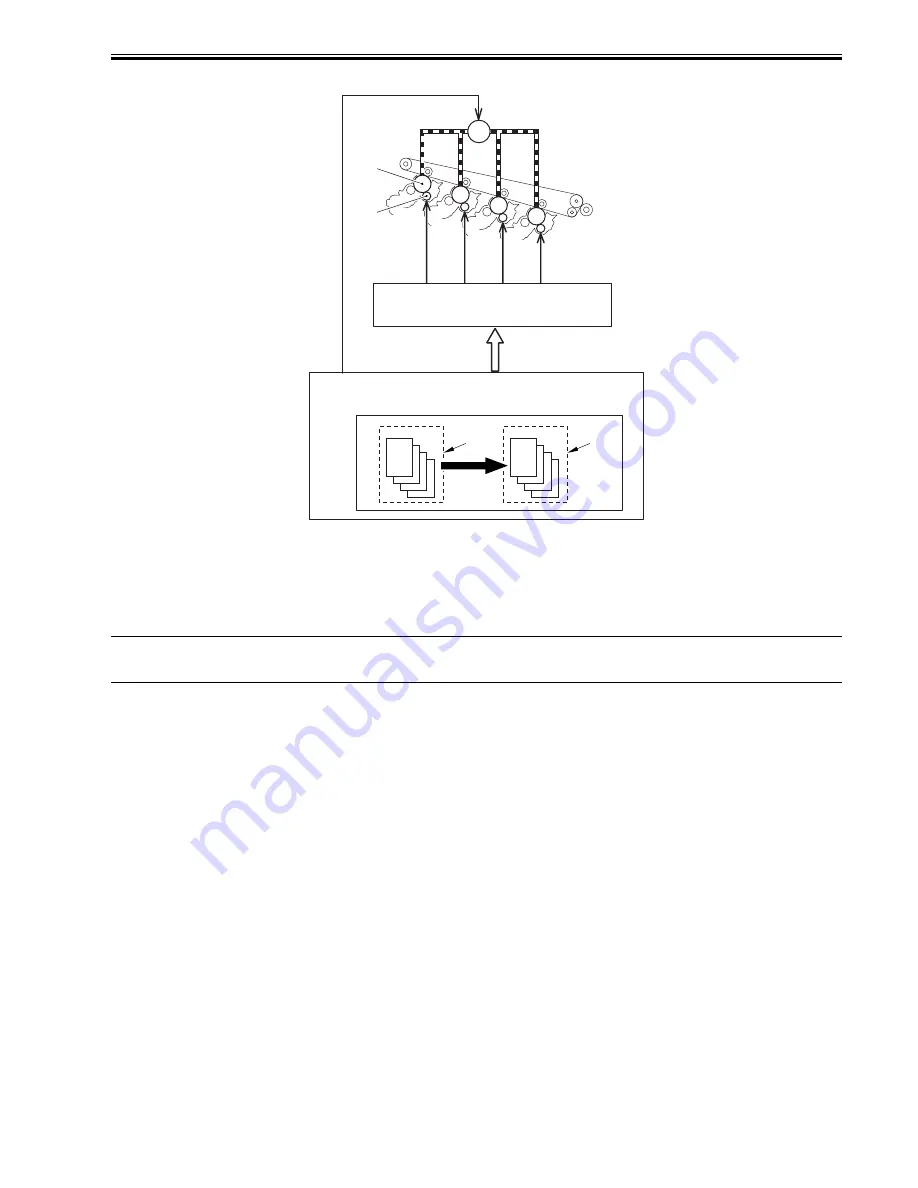
Chapter 7
7-13
F-7-17
[1] Drum/ITB motor drive signal
[2] Photosensitive drum
[3] Primary charging roller
[4] Primary charging AC bias drive signal
[5] Internal data
[6] Drum count
[7] Drum film thickness detection data
MEMO:
The drum film thickness-related data stored in EEPROM may be either drum count or drum film thickness detection data, the drum film thickness count being
internal data and used when determining bias levels.
7.3.4 ATR Control
0013-8486
/ / / / iR C3380i / iR C3380 / iR C2880i / iR C2880
The machine executes ATR control to supply toner so that the ratio between toner and carrier inside the drum unit may remain ideal.
1. timing for start-up
- When new drum unit is installed
- every print (video count)
- every 80-sheet (patch image reading sensor)
2. Particulars of Control
The machine computes the amount of toner to supply for each color, and supplies it to the drum unit.
The machine uses the following 2 types of data to compute toner amounts:
- Video Count (for each print)
The machine uses the video data arriving from the main controller to compute the amount of toner consumed, and makes up for it by supplying the drum unit
with the same amount.
- Result of Detection by the Patch Image Read Sensor (to every 80-sheet *1)
The machine measures the toner image formed on the ITB using the patch image read sensor, and supplies the drum unit so that the density will be identical to
the target density.
*1: The condition of execution is based on printing an original with an image ratio of 25%.
Y
M
C
BK
Y
M
C
BK
Y
M
C
BK
M1
D-CON
EEPROM
HVT1
[3]
[4]
[6]
[2]
[1]
[5]
[7]
Summary of Contents for iR C3380 series
Page 1: ...Aug 29 2006 Service Manual iR C3380 2880 Series...
Page 2: ......
Page 6: ......
Page 23: ...Chapter 1 Introduction...
Page 24: ......
Page 26: ......
Page 52: ......
Page 53: ...Chapter 2 Installation...
Page 54: ......
Page 127: ...Chapter 3 Basic Operation...
Page 128: ......
Page 130: ......
Page 136: ......
Page 137: ...Chapter 4 Main Controller...
Page 138: ......
Page 160: ......
Page 161: ...Chapter 5 Original Exposure System...
Page 162: ......
Page 188: ...Chapter 5 5 24 F 5 68 4 Remove the original sensor 2 hook 1 F 5 69...
Page 189: ...Chapter 6 Laser Exposure...
Page 190: ......
Page 192: ......
Page 206: ......
Page 207: ...Chapter 7 Image Formation...
Page 208: ......
Page 256: ......
Page 257: ...Chapter 8 Pickup Feeding System...
Page 258: ......
Page 262: ......
Page 303: ...Chapter 9 Fixing System...
Page 304: ......
Page 306: ......
Page 321: ...Chapter 10 Externals and Controls...
Page 322: ......
Page 326: ......
Page 336: ...Chapter 10 10 10 F 10 10 2 Remove the check mark from SNMP Status Enabled...
Page 337: ...Chapter 10 10 11 F 10 11...
Page 359: ...Chapter 11 MEAP...
Page 360: ......
Page 362: ......
Page 401: ...Chapter 12 RDS...
Page 402: ......
Page 404: ......
Page 411: ...Chapter 13 Maintenance and Inspection...
Page 412: ......
Page 414: ......
Page 416: ...Chapter 13 13 2 F 13 1 8 9 1 2 3 3 5 6 7 10 11 12 13 14 4...
Page 421: ...Chapter 14 Standards and Adjustments...
Page 422: ......
Page 424: ......
Page 431: ...Chapter 15 Correcting Faulty Images...
Page 432: ......
Page 434: ......
Page 459: ...Chapter 16 Self Diagnosis...
Page 460: ......
Page 462: ......
Page 481: ...Chapter 17 Service Mode...
Page 482: ......
Page 484: ......
Page 571: ...Chapter 18 Upgrading...
Page 572: ......
Page 574: ......
Page 603: ...Chapter 19 Service Tools...
Page 604: ......
Page 606: ......
Page 609: ...Aug 29 2006...
Page 610: ......