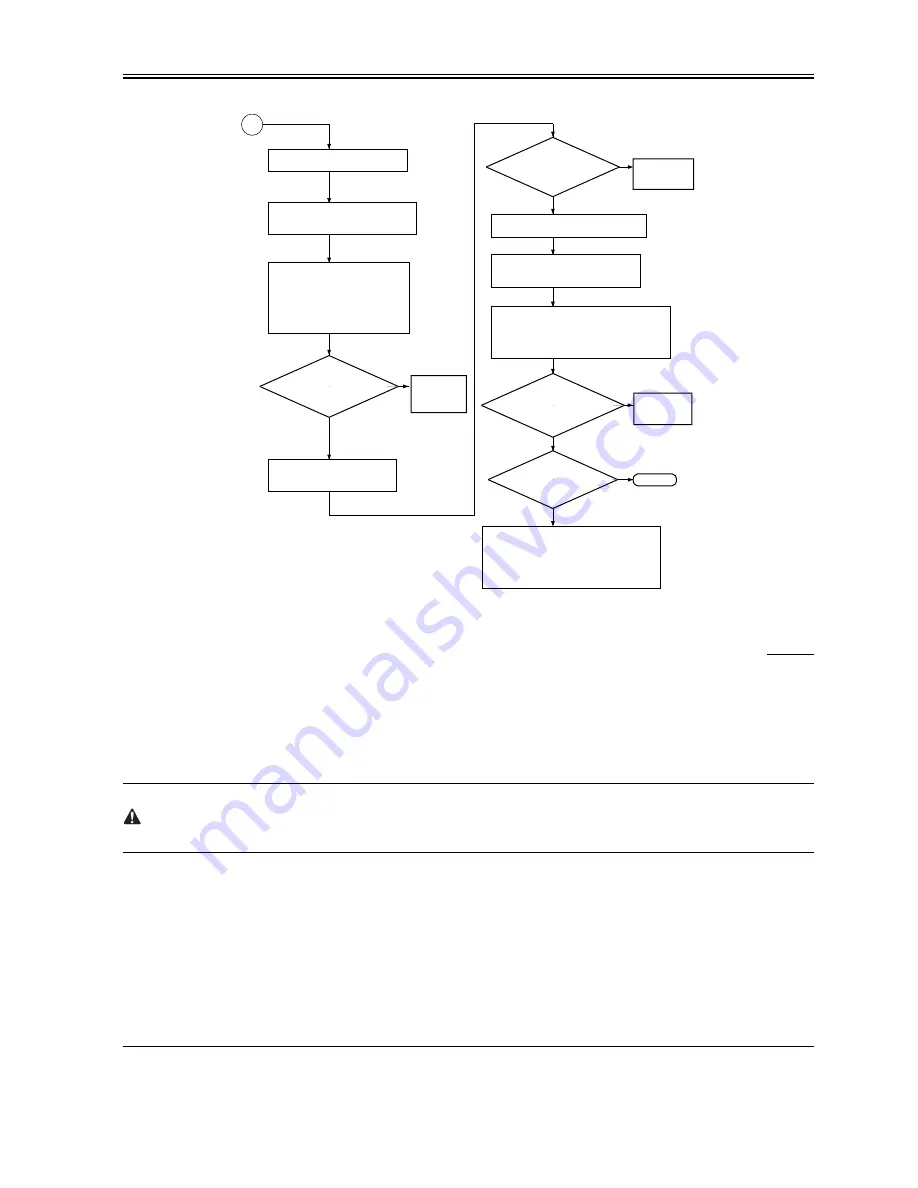
Chapter 13
13-11
F-13-12
13.1.6 Checking the Surface Potential Control System
0008-7914
1. Outline
If an image fault occurs, it is necessary to find out whether the cause is in the static image formation block including the photosensitive drum and
the potential control system or if it is caused at time of development or transfer.
An image fault may be isolated by finding out whether the surface potential is correct using service mode.
2. Disabling the Auto Control Mechanisms
As a means of checking the potential control system, the auto control mechanism may be disabled (hereafter, non-auto control mode).
If the image fault in question is more or less corrected when the machine is in non-auto control mode, you can suspect the potential measurement
unit and the DC controller PCB as the cause of the fault.
You can also take advantage of non-auto control mode as a tentative remedy when the auto control mechanism has a fault.
When the machine is in non-auto control mode, all settings used for corona current control, laser power control, and developing bias control will be
automatically be set to default settings.
Using Non-Auto Control Mode
1)Make the following selections in service mode, enter '0', and press the OK key:
COPIER>OPTION>BODY>PO-CONT.
2) Press the Reset key twice.
3. Making a Zero-Level check
A "zero-level check" is a check made to see if the control mechanism of the DC controller PCB is identifying a 0-V level without fail when the drum
surface potential is 0 V.
A zero-level check may be made in either of 2 ways, and you can use it to decided whether the DC controller PCB and the potential measurement
PCB is free of error:
Method 1: use it to find out if the level shift circuit on the DC controller PCB is free of a fault
Method 2: use it to find out if the potential control circuit is free of a fault
(1) Method 1
1) Turn off the main power switch.
2) Remove the upper rear over.
3) Short GP33 on the DC controller PCB and GND using a cable equipped with an alligator clips or probes on both ends.
Check the developing assembly
for leakage; if normal, go to a
check on the transfer output.
Make the following selections (DC
value of the developing bias):
COPIER>DISPLAY>HV-STS>BIAS.
Covert the indication during printing
(V) into a control voltage with
reference to "Potential Control
Conversion Table."
Is the
deferense between
the actual measurement of
HVT_DEV-BIAS_DC and 'BIAS'
in service mode
± 10%?
YES
NO
Checking the Developing Bias Output
1) Check the transfer charging assembly for
leakage.
2) Make the following selections in service
mode, and try changing the setting:
COPIER>OPTION>BODY>FUZZY.
3) Try replacing paper.
Make the following selections in service mode
(level of current of transfer charging). Convert
the reading (mA) during printing into a control
voltage based on 8.5 "Potential Control
Conversion Table."
Replace the
photosensitive
drum.
NO
YES
NO
YES
NO
Is the
difference between
the measurement of HVT_
TRANSFER and 'TR' in
service mode
+/- 10%?
Checking the Transfer Output
Is the toner
image on the photosensitive
drum before transfer
normal?
Replace the
high-voltage transformer.
Is the problem
corrected?
YES
Replace the
DC controller
PCB.
Replace the
DC controller
PCB.
END
Enable potential control: COPIER>
OPTION>BODY>PO-CNT=1
B
Measure the voltage HVT_DEV_BIAS
_DC during printing of J102A-8 on the
DC controller PCB.
Disable the potential control mechanism
by setting '0' for the following:
COPIER>OPTION>BODY>PO-CNT.
Measure the voltage HVT_TRA during
printing of J102A-12 on the DC
controller PCB.
Summary of Contents for iR5570 Series
Page 1: ...Mar 29 2005 Service Manual iR6570 5570 Series ...
Page 2: ......
Page 6: ......
Page 26: ...Contents ...
Page 27: ...Chapter 1 Introduction ...
Page 28: ......
Page 30: ......
Page 55: ...Chapter 2 Installation ...
Page 56: ......
Page 58: ...Contents 2 9 3 Mounting the Cassette Heater 2 34 ...
Page 98: ......
Page 99: ...Chapter 3 Basic Operation ...
Page 100: ......
Page 102: ......
Page 110: ......
Page 111: ...Chapter 4 Main Controller ...
Page 112: ......
Page 114: ......
Page 135: ...Chapter 5 Original Exposure System ...
Page 136: ......
Page 181: ...Chapter 6 Laser Exposure ...
Page 182: ......
Page 184: ......
Page 192: ......
Page 193: ...Chapter 7 Image Formation ...
Page 194: ......
Page 198: ......
Page 259: ...Chapter 8 Pickup Feeding System ...
Page 260: ......
Page 350: ......
Page 351: ...Chapter 9 Fixing System ...
Page 352: ......
Page 401: ...Chapter 10 External and Controls ...
Page 402: ......
Page 406: ......
Page 448: ......
Page 449: ...Chapter 11 MEAP ...
Page 450: ......
Page 452: ......
Page 455: ...Chapter 12 Maintenance and Inspection ...
Page 456: ......
Page 458: ......
Page 468: ......
Page 469: ...Chapter 13 Standards and Adjustments ...
Page 470: ......
Page 505: ...Chapter 14 Correcting Faulty Images ...
Page 506: ......
Page 508: ......
Page 537: ...Chapter 15 Self Diagnosis ...
Page 538: ......
Page 540: ......
Page 565: ...Chapter 16 Service Mode ...
Page 566: ......
Page 568: ......
Page 633: ...Chapter 17 Upgrading ...
Page 634: ......
Page 636: ......
Page 641: ...Chapter 17 17 5 F 17 4 HDD Boot ROM Flash ROM System Software ...
Page 646: ...Chapter 17 17 10 F 17 11 8 Click START F 17 12 ...
Page 675: ...Chapter 17 17 39 F 17 59 2 Select the data to download F 17 60 3 Click Start ...
Page 677: ...Chapter 18 Service Tools ...
Page 678: ......
Page 680: ......
Page 683: ...Mar 29 2005 ...
Page 684: ......