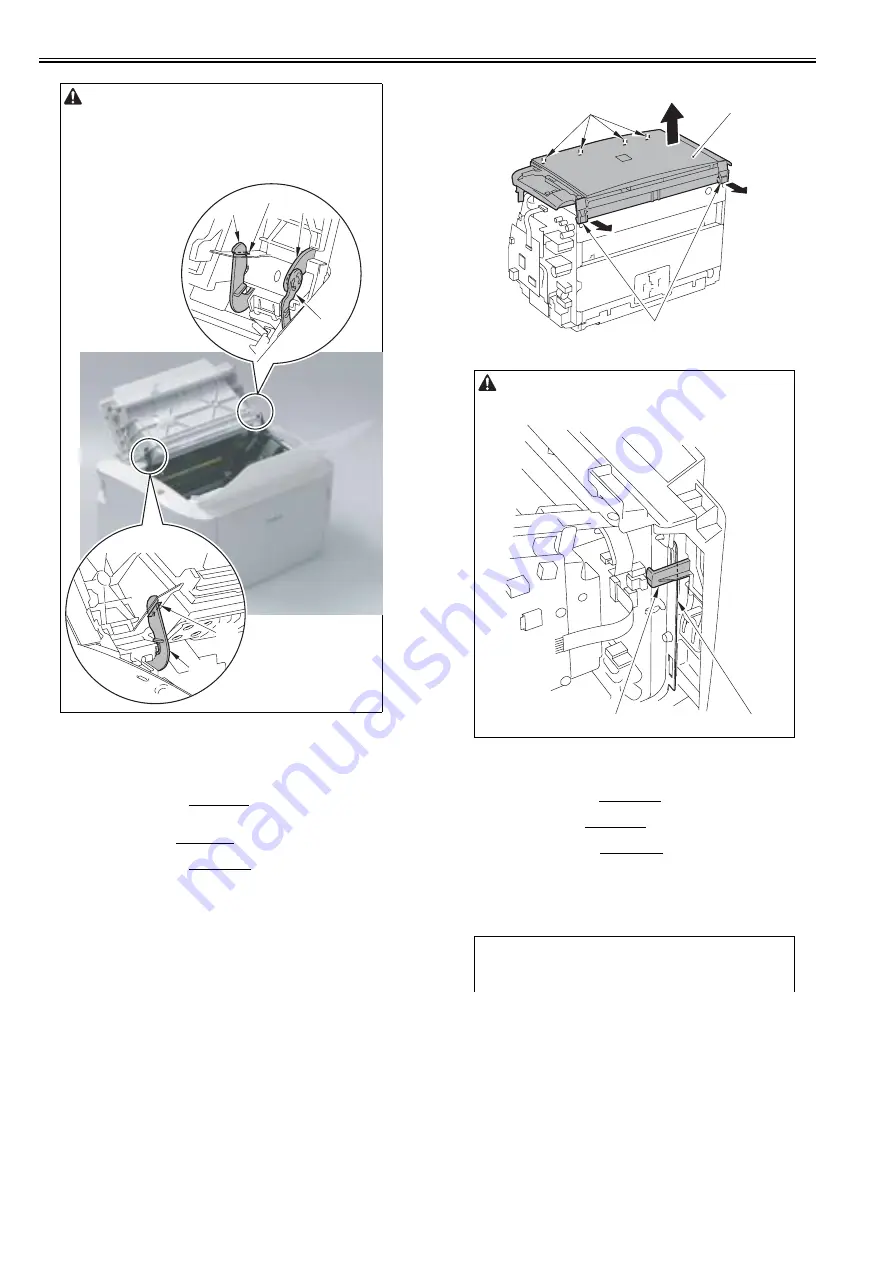
Chapter 3
3-6
3.1.5 Front Cover
3.1.5.1 Preparation for Removing the Front Cover
0019-2203
LBP3100 / LBP3010B
1) Removing the Upper Cover
Reference[Removing the Upper
Cover]
2) Removing the Left Cover
Reference[Removing the Left Cov-
er]
3) Removing the Right Cover
Reference[Removing the Right
Cover]
3.1.5.2 Removing the Front Cover
0019-2204
LBP3100 / LBP3010B
1) Release the 2 hooks in the arrow [A] direction.
2) While releasing the 4 hooks [2] in the arrow [B] direction, remove the
front cover [3].
F-3-12
3.1.5.3 Before Remove the Front Cover
0025-1212
LBP6000 / LBP6000B
Reference[Removing the Upper
Cover]
2) Remove the Left Cover.
Reference[Removing the Left Cov-
er]
3) Remove the Right Cover.
Reference[Removing the Right
Cover]
3.1.5.4 Removing the Front Cover
0025-1213
LBP6000 / LBP6000B
Points to Note at Installation
- Be sure to fit the 2 Fixing Pressure Arms (Right and Left) [2] into the 2
holes (right and left) [1] of the Delivery Tray.
- Be sure to set the Cartridge Lock Arm [4] to the arm unit [3] on the
Delivery Tray.
[1]
[2]
[1]
[3]
[2]
[4]
Points to note at installation
Make sure that the switch arm [1] does not contact with the edge of the plate
[2] when attaching the cover.
MEMO:
The following shows the 4 hooks [1] and 4 hook holes [2] of the Front
Cover.
[3]
[B]
[A]
[A]
[1]
[2]
[2]
[1]
Summary of Contents for LBP6000 Series
Page 1: ...Sep 8 2010 Service Manual LBP6000 6018 3010 3100 3150 Series...
Page 2: ......
Page 6: ......
Page 12: ...Contents...
Page 13: ...Chapter 1 PRODUCT DESCRIPTION...
Page 14: ......
Page 16: ......
Page 28: ......
Page 29: ...Chapter 2 TECHNICAL REFERENCE...
Page 30: ......
Page 74: ......
Page 75: ...Chapter 3 DISASSEMBLY AND ASSEMBLY...
Page 76: ......
Page 119: ...Chapter 4 MAINTENANCE AND INSPECTION...
Page 120: ......
Page 122: ......
Page 126: ......
Page 127: ...Chapter 5 TROUBLESHOOTING...
Page 128: ......
Page 130: ......
Page 137: ...Chapter 6 APPENDIX...
Page 138: ......
Page 140: ......
Page 144: ......
Page 145: ...Sep 8 2010...
Page 146: ......