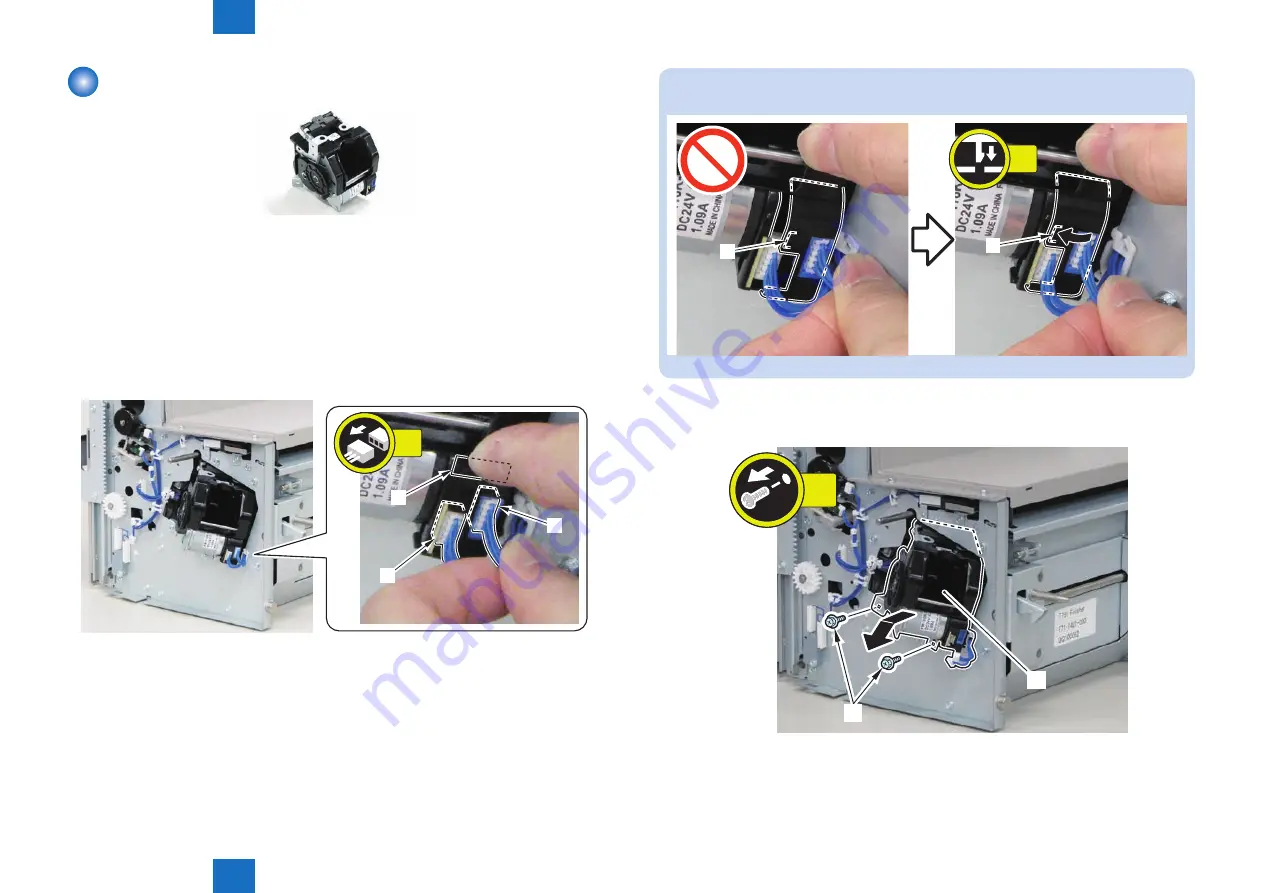
4
4
4-23
4-23
Parts Replacement and Cleaning Procedure > Major Units > Removing the Staple Unit > Procedure
Parts Replacement and Cleaning Procedure > Major Units > Removing the Staple Unit > Procedure
Removing the Staple Unit
■
Preparation
1) Remove the Finisher Unit from the connected equipment(Refer to page 4-9).
2) Remove the Staple Cartridge(Refer to page 4-22).
3) Remove the Front Cover(Refer to page 4-15).
■
Procedure
1) While holding the [A] part of the Motor Cover, disconnect the 2 connectors [1].
2x
[A]
[1]
[1]
F-4-50
F-4-51
NOTE:
If the claw [2] of the Motor Cover is disengaged, hook the claw again.
[2]
[2]
1x
F-4-52
2) Remove the Staple Unit [1].
• 2 Screws [2]
2x
[1]
[2]
F-4-53
Summary of Contents for Staple Finisher-S1
Page 6: ...Safety Precautions Notes Before Servicing Points to Note at Cleaning ...
Page 8: ...1 1 Product Outline Product Outline Features Specifications Names of Parts ...
Page 36: ...3 3 Periodic Servicing Periodic Servicing List of Work for Scheduled Servicing ...
Page 94: ...5 5 Adjustment Adjustment Adjustment Item Dip Switch Function ...
Page 113: ...Appendix Service Tools General Circuit Diagram ...