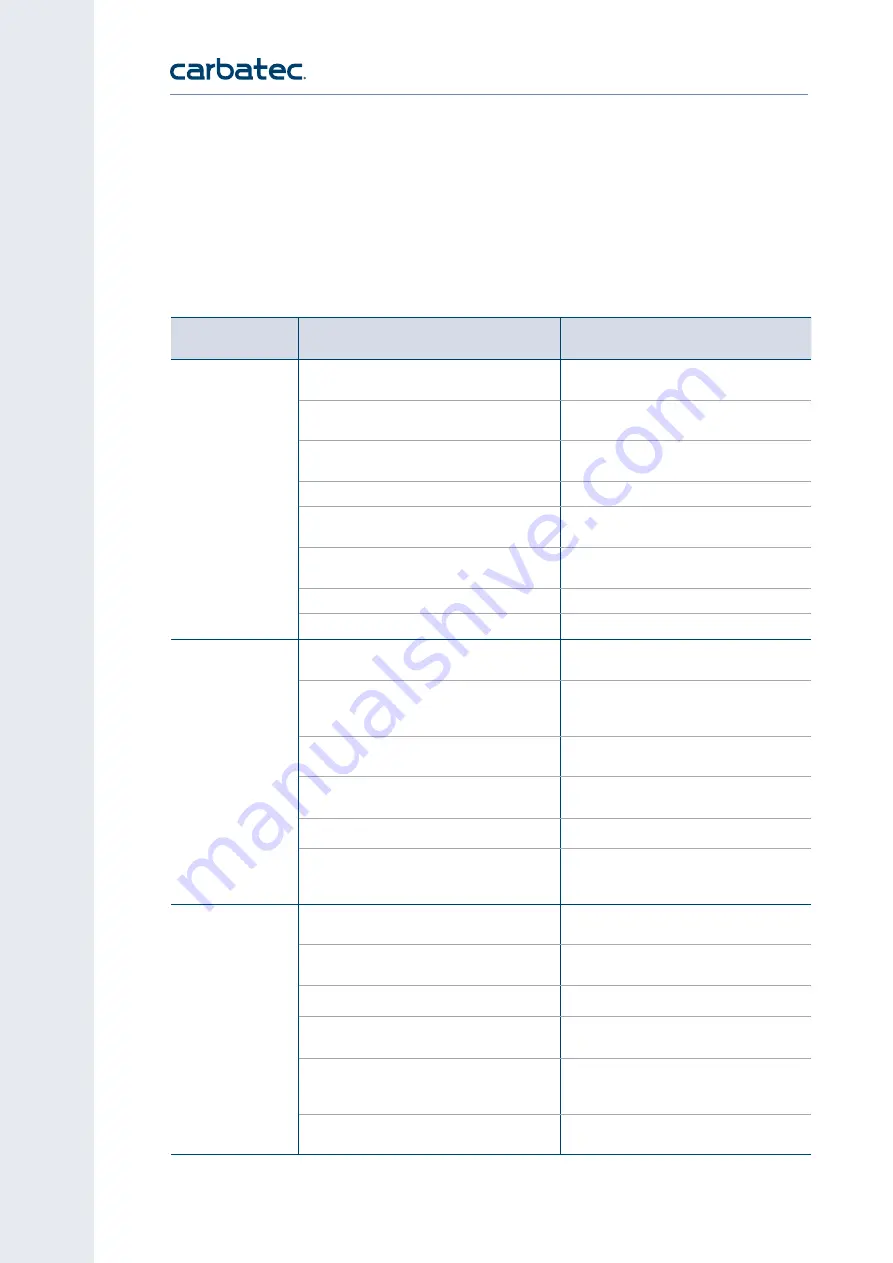
FOR TEC HNICAL SUPPOR T CALL
1800 658 111
28
CDC-650P
TO PREVENT INJURY TO YOURSELF or damage to the cyclone dust collector, turn the switch to the
“OFF” position and unplug the power cord from the electrical receptacle before making any adjustments.
TROUBLESHOOTING
PROBLEM
LIKELY CAUSE(S)
SOLUTION(S)
Machine does not
start, or power
supply fuse or
breaker trips
immediately after
startup.
1.
Cyclone dust collector not properly
connected to ducting.
Connect dust collector to ducting.
2.
Incorrect power supply voltage or
circuit size.
Ensure correct power supply voltage and
circuit size.
3.
Power supply circuit breaker tripped or
fuse blown.
Ensure circuit is sized correctly and free of
shorts.
4.
Motor overheated.
Reset circuit breaker or replace fuse.
5.
Wiring open / has high resistance.
Allow motor to cool, reset overload
if necessary.
6.
Power switch at fault.
Check and fix broken, disconnected,
or corroded wires.
7.
Capacitor at fault.
Test and replace.
8.
Motor at fault.
Test and repair or replace.
Machine seems
underpowered.
1.
Motor overheated.
Allow motor to cool, reset overload if
necessary.
2.
Dust-extraction ducting problem.
Clear blockages, seal leaks, use smooth-
wall duct, eliminate bends, close other
branches.
3.
Canister filter clogged or at fault.
Clean canister filter.
Replace canister filter.
4.
Dust extractor too far from machine or
undersized for dust extraction system.
Move closer to machine or redesign
ducting layout or upgrade dust extractor.
5.
Capacitor at fault.
Test and repair or replace.
6.
Motor bearings at fault.
Test by rotating shaft.
Rotational grinding or loose shaft requires
bearing replacement.
Machine has
vibration or noisy
operation.
1.
Motor or component loose.
Inspect, replace damaged bolts and nuts,
and retighten with thread-locking fluid.
2.
Motor fan rubbing on fan cover.
Fix replace fan cover.
Replace loose or damaged fan.
3.
Motor mount loose or broken.
Tighten or replace.
4.
Impeller damaged, unbalanced, or
loose.
Inspect, tighten or replace.
5.
Motor bearings at fault.
Test by rotating shaft.
Rotational grinding or loose shaft requires
bearing replacement.
6.
Motor shaft bent.
Test with dial indicator.
Replace motor if damaged.