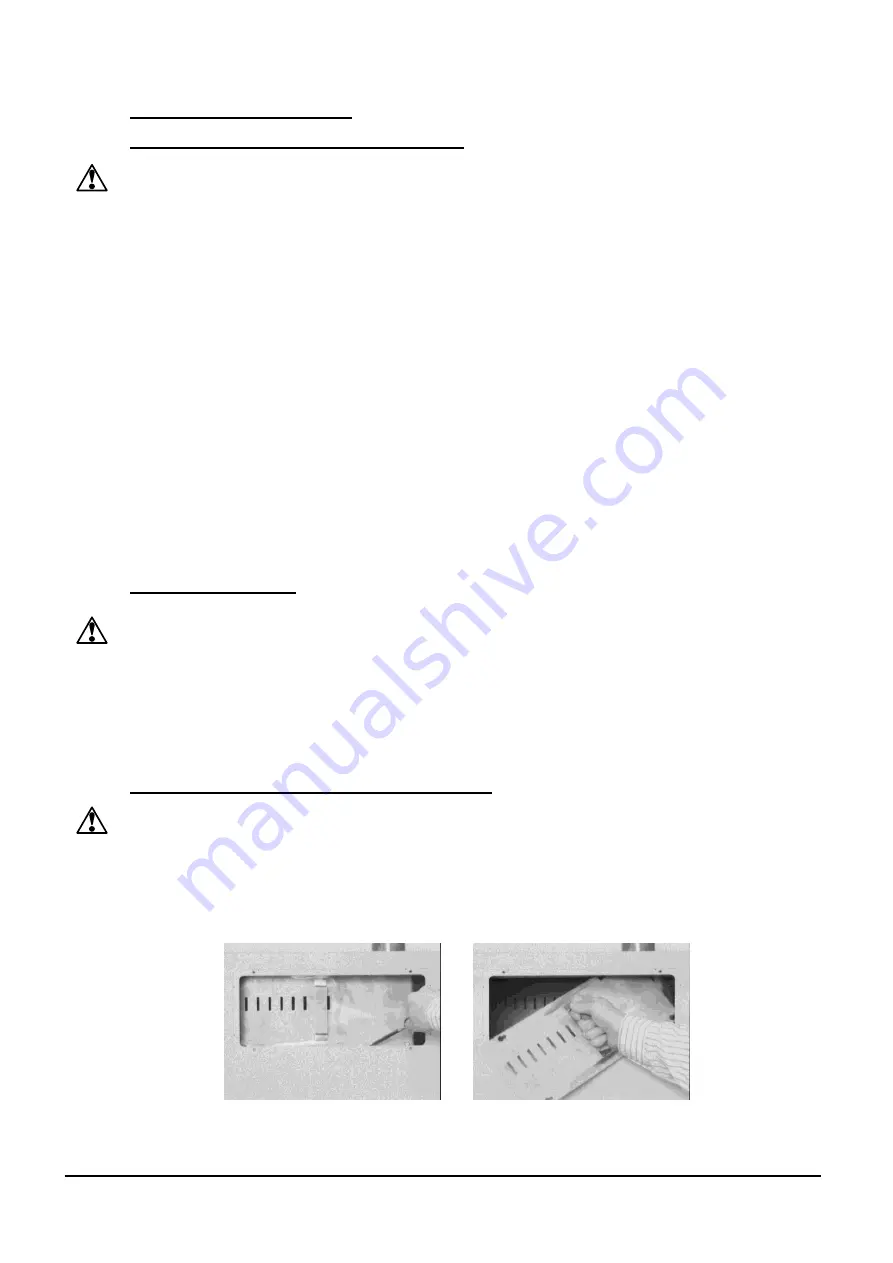
MF58
– 1.06 9
M
AINTENANCE
&
R
EPAIRS
4.0
Safety Note - Refractory Fibrous Insulation
Insulation made from High Temperature Insulation Wool
Refractory Ceramic Fibre, (better described as Alumino Silicate Wool) (ASW)
This product contains
alumino silicate wool products
in its thermal insulation. These materials
may be in the form of blanket or felt, formed board or shapes, mineral wool slab or loose fill
wool.
Whilst there is no evidence of any long term health hazards, we strongly recommend that safety
precautions are taken whenever the materials are handled.
Exposure to fibrous dust may cause respiratory disease.
When handling the material always use an approved respiratory protection equipment
(RPE-i.e. FFP3), eye protection, gloves and long sleeved clothing.
Avoid breaking up waste material. Dispose of waste in sealed containers.
After handling rinse exposed skin with water before washing gently with soap (not
detergent). Wash work clothing separately.
Before commencing any major repairs we recommend reference to the European Association
representing the High Temperature Insulation Wool industry
(www.ecfia.eu)
We can provide further information on request. Alternatively our service division can quote for
any repairs to be carried out at your premises or ours.
4.1
General Maintenance
Regularly clean the plenum chamber, as described below.
The outer surface of the unit may be cleaned with a damp cloth. Do not allow water to enter the
interior of the case or chamber. Do not clean with organic solvents.
Occasionally remove the lower side panels and clean out any accumulated dust in the balance
compartment. If necessary, remove the balance assembly and give a thorough cleaning.
If the ABF is used below its maximum temperature of 800°C, then regularly heat it up to 750°C
for one hour, without load, to burn off any accumulated soot.
4.2
Cleaning the Plenum Chamber & Fan Impeller
Remove the upper side access panel, and the cover of the plenum chamber. Clean out all
accumulated soot and debris using a vacuum cleaner. Also clean any accumulated soot from the
fan impeller located at the back of the plenum chamber. If the accumulation of soot on the
impeller is great it may be necessary to remove the motor/impeller assembly from the back of the
plenum chamber to give good access for cleaning.
Photo 4.1 Photo 4.2
accessing the plenum chamber
Summary of Contents for ABF 8/28
Page 14: ...14 MF58 1 06 ...
Page 15: ...MF58 1 06 15 ...