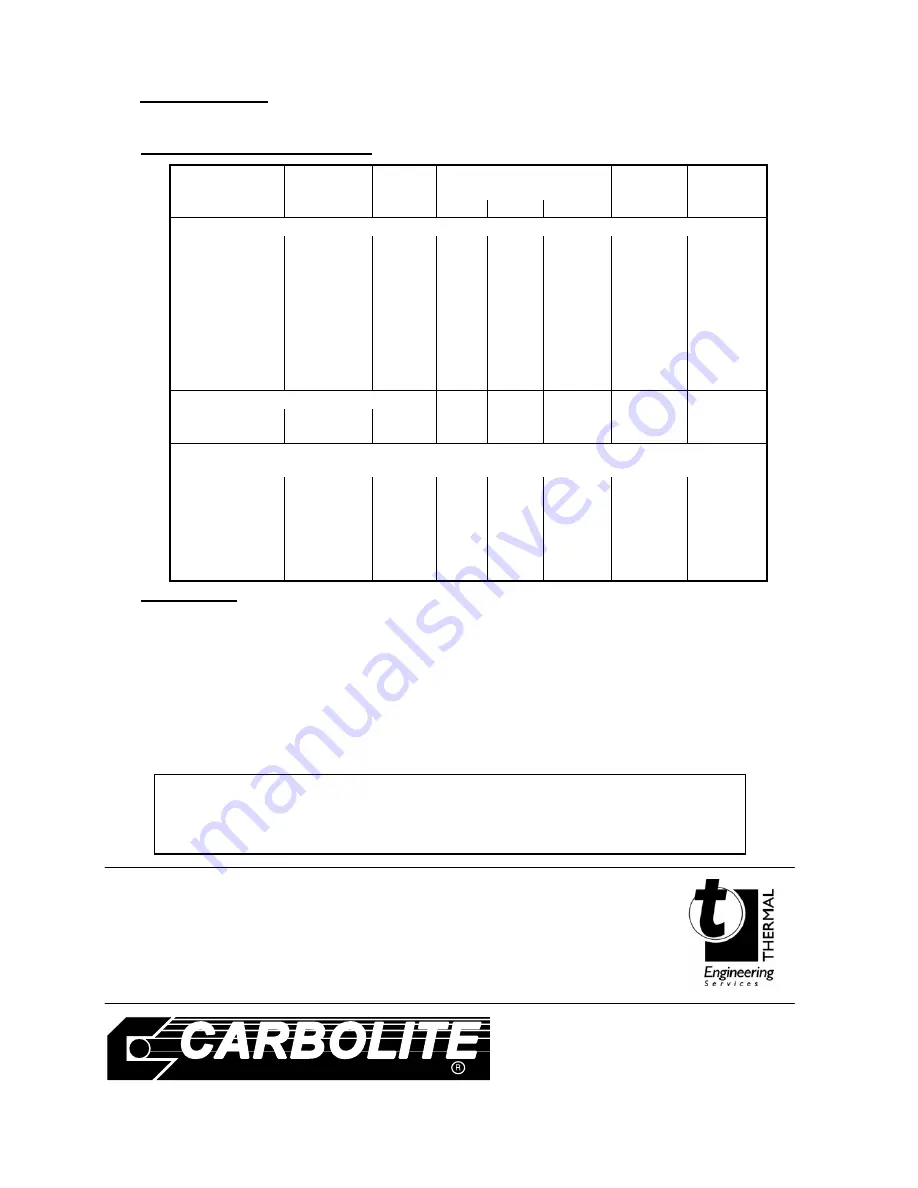
S
PECIFICATIONS
Carbolite reserves the right to change specifications without notice
.
9.1
Models Covered by this Manual
MODEL Max.
Temp.
Max.
Power
Chamber Size (mm)
Approx.
Capacity
Net
Weight
(°C)
(kW)
H
W
D
(l)
(kg)
Chamber furnaces heated by resistance wire inserted in refractory formers.
CWF 11/5
1100°C
2.4
135
140
250
5
30
CWF 11/13
1100°C
3.1
200
200
325
13
47
CWF 11/23
1100°C
7.5
235
245
400
23
68
CWF 12/5
1200°C
2.4
135
140
250
5
30
CWF 12/13
1200°C
3.1
200
200
325
13
47
CWF 12/23
1200°C
7.5
235
245
400
23
68
CWF 13/5
1300°C
2.4
135
140
250
5
30
CWF 13/13
1300°C
3.1
200
200
325
13
47
CWF 13/23
1300°C
7.5
235
245
400
23
68
Burn-off versions of the above.
BWF 11/13
1100°C
3.1
200
200
325
13
47
BWF 12/13
1200°C
3.1
200
200
325
13
47
Chamber furnaces heated by resistance wire embedded in low thermal mass
insulation.
RWF 11/5
1200°C
2.75
130
160
250
5
28
RWF 11/13
1200°C
5.0
195
210
325
13
45
RWF 11/23
1200°C
9.1
220
260
400
23
65
RWF 12/5
1200°C
2.75
130
160
250
5
28
RWF 12/13
1200°C
5.0
195
210
325
13
45
RWF 12/23
1200°C
9.1
220
260
400
23
65
9.2 Environment
The furnaces contain electrical parts and should be stored and used in indoor conditions as
follows:
temperature:
5°C - 40°C
relative humidity:
maximum 80% up to 31°C decreasing linearly to 50% at 40°C
MF02-3.12
5/12/00
CWF
Carbolite, Parsons Lane, Hope,
Hope Valley, S33 6RB, England.
Telephone:
(01433) 620011
Int: +44 1433 620011
Facsimile:
(01433) 621198
Int: +44 1433 621198
E-mail:
enquiry@carbolite.co.uk
For preventive maintenance, repair and calibration of all Furnace
and Oven products, please contact:
Thermal Engineering Services
Telephone:
UK: 0845 3308035
Int: +44 1433 623335
Fax:
UK: 0845 3308036
Int: +44 1433 623336
Email:
thermalserve@dial.pipex.com
The products covered in this manual are only a small part of the wide range of
ovens, chamber furnaces and tube furnaces manufactured by Carbolite for
laboratory and industrial use.
For further details of our standard or custom built
products please contact us at the address below, or ask your nearest stockist.