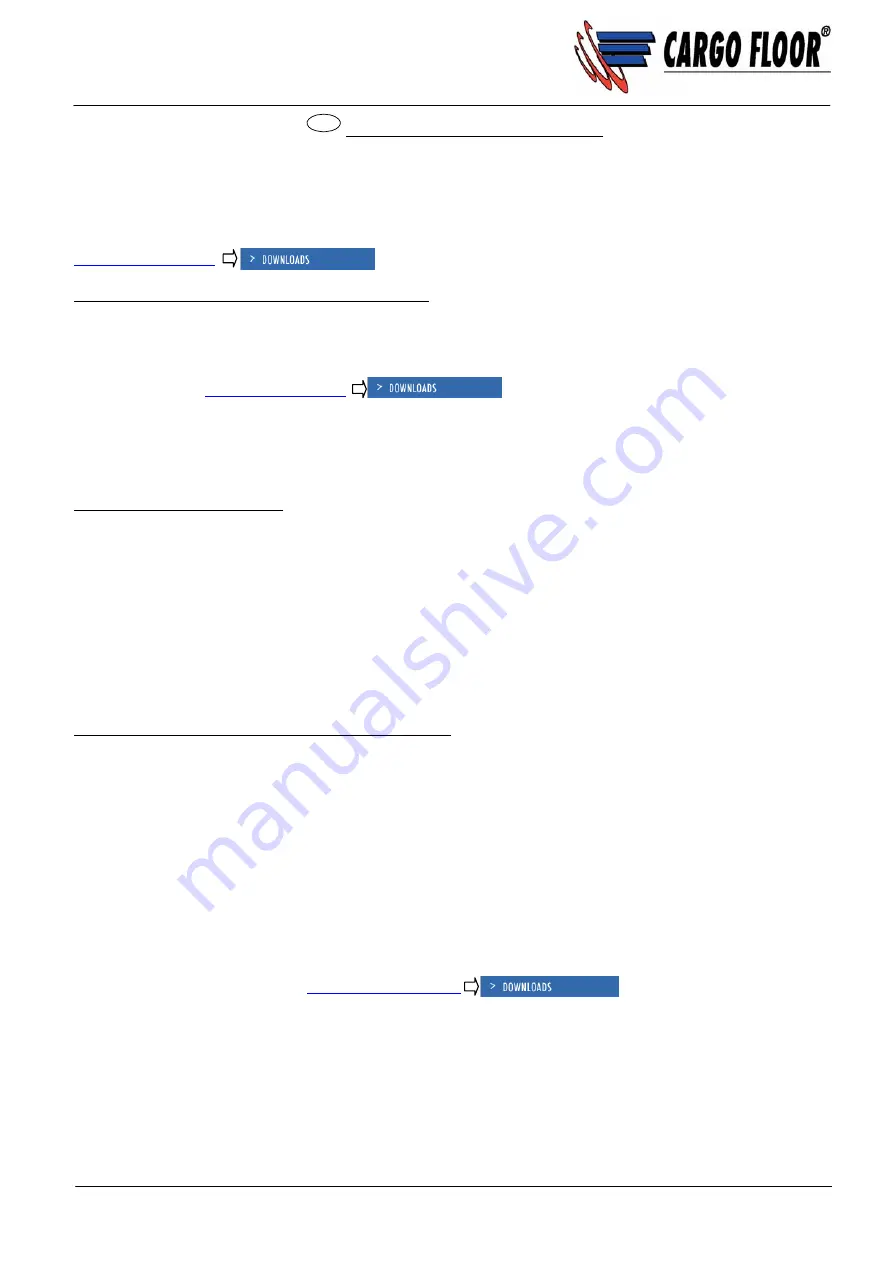
2012 Cargo Floor B.V. Coevorden, Holland
Versie 01/11-01-2012
www.cargofloor.com
info@cargofloor.com
Cargo Floor B.V.
P.O. Box 271
NL-7740 AG Coevorden
Phone: +31-(0)524-
593900
Fax: +31-(0)524-
593999
Blz. 73
GB
MAINTENANCE INSTRUCTIONS
When handing over the trailer to the end user always give an extended instruction with regards to operation,
maintenance and use of the Cargo Floor system. At the handing over always give a users manual. When works
require turning on the floor you should take care of that the floor can be shut down immediately at any time.
Places where clamping/clasping of body parts is possible may not be approached when the system is moving.
For more detailed explanation of the execution of the works we would like to refer you to our website:
www.cargofloor.com
Check for the end user after receipt of the new trailer:
Check the join between the aluminium floor profiles and the Cargo Floor-system. You do this by placing your
finger half on the bolt and half on the floor profile when the floor is operating. If you feel movement in the bolt
connection then the bolt should be removed, cleaned, fitted with Loctite and mounted again, or be replaced. Do
not simply just tighten the bolts, the Loctite connection will be broken. If bolts are loose, we would like to refer
you to our website:
www.cargofloor.com
. Check this a couple of days after receipt of the
trailer, after 10 loads / unloads and after one month.
Specifications of the screws:
M12 x 30 countersunk screws with hexagon socket, class 10.9, galvanized. DIN 7991 (Dacromet).
The torque is 100 – 140 Nm.
Regular checks for the enduser:
To ensure that your Cargo Floor system operates reliably and has a long life, it is important that you regularly
perform careful checks on the following aspects:
-
The quality of the oil; this must be cleaned regularly (check every ½ year);
- Replace the filter element every year;
-
Change the oil every 2 years, or more frequently if required;
-
The level of oil in the tank. In order to prevent heat developing it is required to have at least 100 liters of oil in
the tank. Out of practical experience (high flow, frequently loading and unloading) we advise you to have at
least 150 liters of oil available. Use a good quality, hydraulic oil in accordance with the ISO VG 32 norm.
Check and, if necessary clean the following components:
- Floor profiles: are they still fixed, replace screws/bolts if necessary!
-
Check the ducts and joints of all hydraulic components, and adjust if necessary!
-
Oil tank: by taking the lid off the tank, you can remove any remains (condensation, dirt etc.) from the bottom.
-
Return-/pressure filter: by removing the filter lid/ chamber you can check the filter element, or after one year
replace it.
- Check the seal between the two fixated floor profiles and the moving profiles. If a margin exist in between,
then adjust the fixated floor profiles, in order for the sealing to be optimal and leakage via the side walls is
prevented.
This is all necessary to avoid internal wear (of the pump/cylinders etc., for example).
New filter parts are available at your system builder. For the right type we refer you to our “exploded views”
which you can find on our website
www.cargofloor.com
We want to emphasize that the minimal costs of replacing dirty parts or oil do not match the costs and discomfort
that can proceed out of this.
-
Adjusting the threaded rod of the steering valve;
It is important that the steering valve is correctly adjusted and that the switchover moment occurs according to
the procedures. See page 56.
Cleaning the floor parts with a steam cleaner is also part of the regular preventative maintenance, especially with
the so called SLP profiles this is mandatory to clean the large gulley regularly.