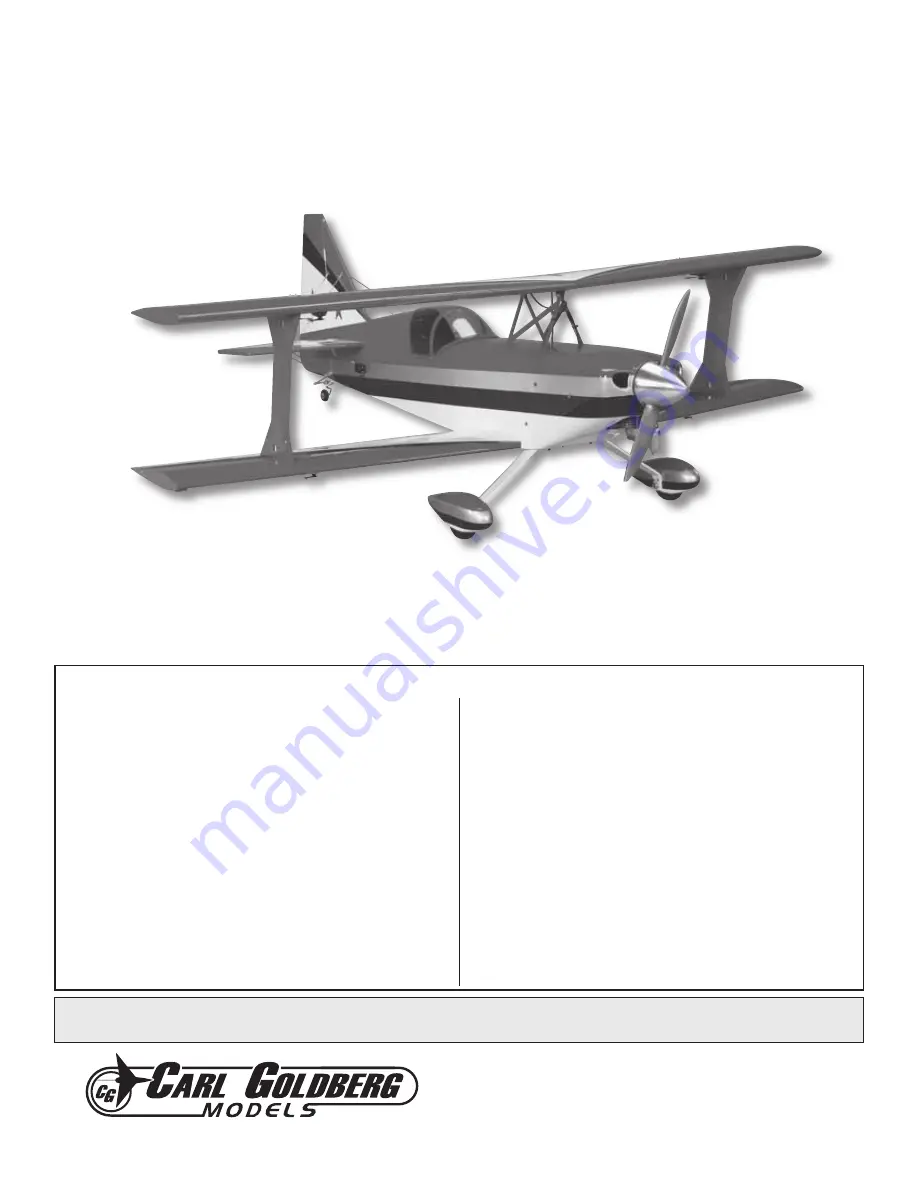
READ THROUGH THIS MANUAL BEFORE STARTING CONSTRUCTION. IT CONTAINS IMPORTANT
INSTRUCTIONS AND WARNINGS CONCERNING THE ASSEMBLY AND USE OF THIS MODEL.
Champaign, Illinois
(217) 398-8970
www.carlgoldbergproducts.com
Carl Goldberg Products Ltd.
has inspected and certifi ed the
components of this aircraft. The company urges the buyer to
perform their own inspection, prior to assembly, and to immediately
request a replacement of any parts they believe to be defective
for their intended use. The company warrants replacement of any
such components, provided the buyer requests such replacement
within a period of 90 days from the date of purchase and provided
the defective part is returned, if so requested by the company.
No other warranty, expressed or implied, is made by the company
with respect to this kit. The buyer acknowledges and understands
that it is their responsibility to carefully assemble the fi nished fl ying
model airplane and to fl y it safely. The buyer hereby assumes full
responsibility for the risk and all liability for personal or property
damage or injury arising out of the buyer’s use of the components
of this kit.
If the buyer is not prepared to accept the liability associated
with the use of this product, the buyer is advised to return
this kit immediately in new and unused condition to the place
of purchase.
To make a warranty claim send the defective part or item to Hobby
Services at the address below:
Hobby Services
3002 N. Apollo Dr., Suite 1
Champaign, IL 61822 USA
Include a letter stating your name, return shipping address, as
much contact information as possible (daytime telephone number,
fax number, e-mail address), a detailed description of the problem
and a photocopy of the purchase receipt. Upon receipt of the
package, the problem will be evaluated as quickly as possible.
LIMITED WARRANTY
Entire Contents © Copyright 2008
GBGZ1047 for GBGA1047 V1.0
Wingspan:
60.5 in [1535mm]
Wing Area:
1250 in
2
[80.6dm
2
]
Weight:
11.75 – 12 lb [5330 – 5445g]
Wing Loading:
22 oz/ft
2
[67g/dm
2
]
Length:
66 in [1675mm]
Radio:
5-channel minimum
Servos:
(6) Futaba 9001 servos, (1) Futaba 9202 servo (rudder),
(1) Futaba 3003 servo (throttle)
Engine
.90 – 1.20 cu in [15 – 20cc] two-stroke,
1.20
–
1.50 cu in [20 – 25cc] four-stroke
The Ultimate ARF
INSTRUCTIONS
Welcome to the world of
Ultimate
fl ying! Now that you’re an
experienced R/C pilot, you’re ready to step up to a higher level
of aerobatic fl ying. And we’ve made sure this ARF version won't
disappoint. With the same fl ight characteristics as the kit version,
you’ll soon know why the
Carl Goldberg Products Ultimate
has been America’s favorite sport biplane since 1990.
™