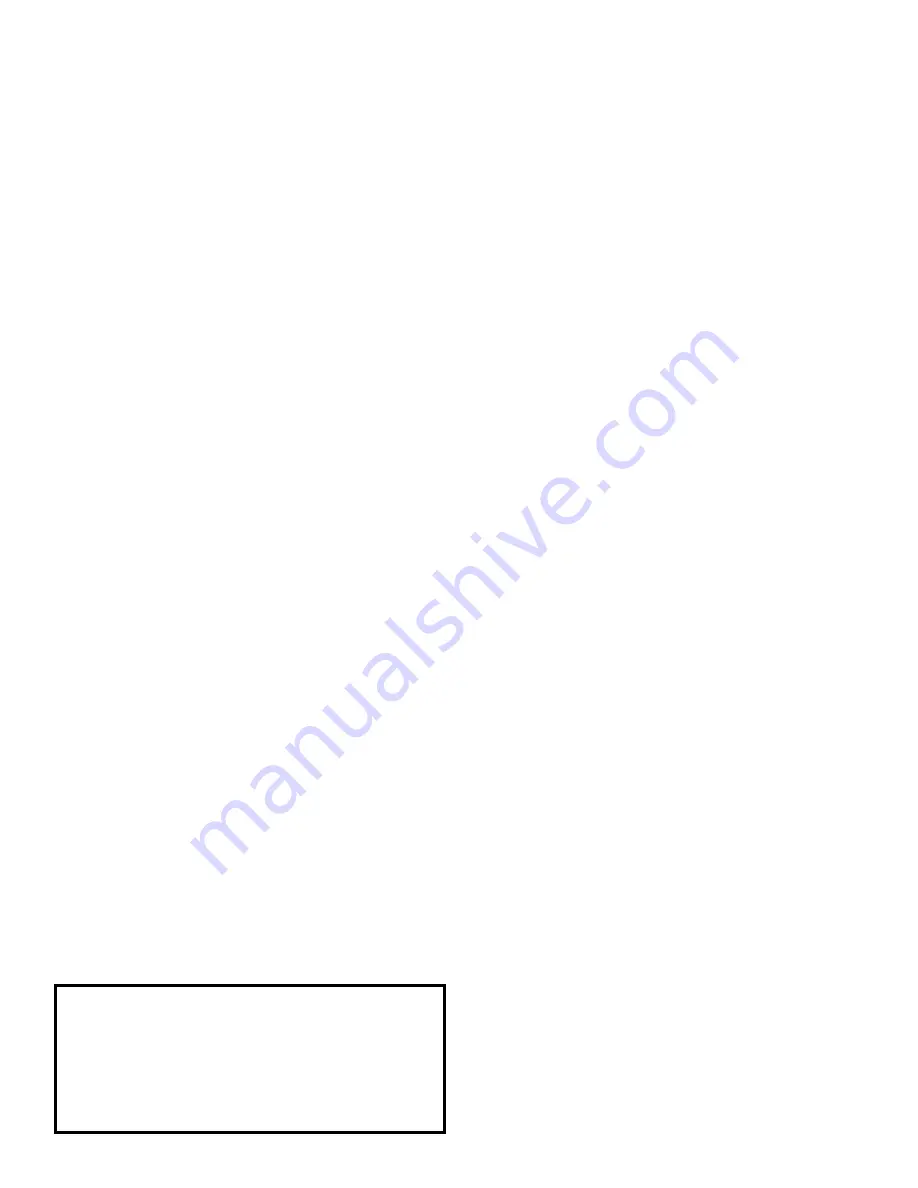
NOTE: The Skylark 70 ARF colors match Midnight
Blue(885), True Red(866) and White (#870)
UltraCote®.
2
TOOLS AND SUPPLIES FOR ASSEMBLY
.
MODELING OR UTILITY KNIFE
WORK SURFACE (24" X70")
ELECTRIC DRILL
1/16”, 3/32”,1/8", 5/32”, 1/4” DRILL BITS
SMALL STANDARD & PHILLIPS SCREW-
DRIVERS
MASKING TAPE
NEEDLE NOSE PLIERS
36” RULER OR TAPE MEASURE
FLEXIBLE STRAIGHT-EDGE
T-SQUARE
30-60-90° x 6" TRIANGLE
SOFT PENCIL
A FEW STRAIGHT OR "T" PINS
ADJUSTABLE WRENCH
WIRE CUTTER
OPTIONAL HEAT GUN/COVERING IRON
ACID BRUSH
USING THIS INSTRUCTION MANUAL
Before you begin assembling your
Skylark 70 ARF
, take
some time to read through this entire instruction book. It is
designed to take you step-by-step through the process and
to give you added information on engine and radio selec-
tion and set-up, balancing your aircraft, and flying your
model. The time you spend will speed the assembly
process and help you avoid problems.
PREPARING FOR ASSEMBLY
You will need a work area of approximately 24 x 70" which has
been covered to protect it from adhesive, as well as cuts and
other damage. Many people cover their work area with a
sheet of dry wall (sheet rock) and/or waxed paper t o pre-
vent CA Glue and Epoxy from ruining the work surface.
CONSTRUCTION TIPS
IMPORTANT: ALWAYS READ A FEW STEPS AHEAD.
This will alert you to coming instructions and will help you
plan accordingly.
Using the Parts Identification section, familiarize yourself
with the various items included in your kit box.
As you work, CHECK OFF EACH STEP in the box provid-
ed, so that you are sure you do not forget anything.
Do not hesitate to ask questions. Your local hobby dealer
and area flyers will most likely be happy to help, as they
want you to have a successful flying experience. You may
also receive technical assistance from Carl Goldberg
Products, Ltd. via by telephone 1-678-450-0085.
ADHESIVES & GLUING TECHNIQUES
CA adhesives are specially formulated to firmly glue the
plywood, hardwood, and balsa used in your model and to
withstand the vibration and stresses of high performance
flight. However, there are times, such as when you are
installing the stabilizer and fin on the fuselage and want
more set-up time for careful alignment and positioning,
then you should use epoxy.. Occasionally, you also will
want to use thin CA, which "wicks" into the surrounding
areas. Aliphatic resin glue or similar water-based glues can
also be used, but they will add to the assembly time
because they dry so much more slowly than CA glue.
Remember, when ever using any CA, you must be careful
to read instructions thoroughly, as you will have only sec-
onds for positioning of parts. Be sure to trial fit parts
together before gluing. Also, never use watery THIN type
CA glue for gluing plywood and hardwood parts. Thin CA's
do not adequately bond these areas.
CAUTION
Some people may experience an allergic reaction when
exposed to fumes from CA glue or epoxy. As with paints,
thinners, and solvents, it is always important to use glues
only where there is adequate ventilation to carry fumes
away. A fan is recommended. Also, special care must be
taken when using CA, as it will bond skin as well as other
surfaces. Before using any CA, carefully read all label pre-
cautions. When using CA, protective eye-wear and care in
keeping the glue away from the face is highly recommend-
ed. If CA does happen to get into the eye, hold lid open
and flush with water only. Seek immediate medical atten-
tion.
Notice:
Before starting be sure all parts have
not been damaged during shipping.
Once assembly has been started, all
warranty on parts are void.
ITEMS NEEDED TO COMPLETE THIS AIRCRAFT
1 RADIO GUIDANCE SYSTEM (4 CHANNEL
MINIMUM REQUIRED, 5 STANDARD SER-
VOS )
2 6” EXTENSIONS
1 Y-HARNESS
1 ENGINE .61 2-CYCLE
1 ULTRA SET CA ACCELERATOR
1 ULTRA SET 2 OZ. BOTTLE MEDIUM CA
GLUE
1 ULTRA SET 1/2 OZ. BOTTLE THIN CA
GLUE
1 ULTRA SET 20 MIN EPOXY
1
1/2” FOAM RUBBER
1 SWITCH MOUNT
1 3” SPINNER