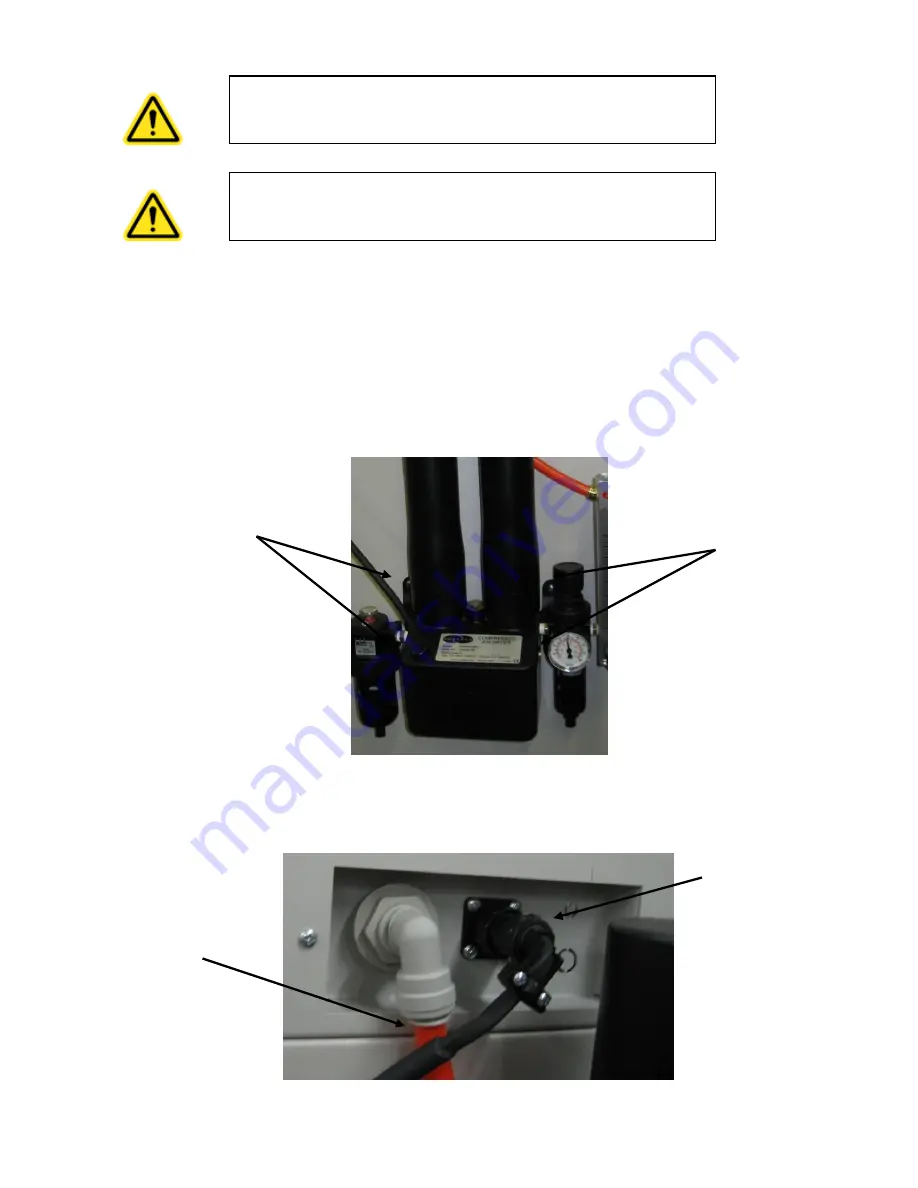
6200 series Operations Manual
Rev D 2/14/2012
Page 19 of 60
Incoming compressed air must be free of dirt, oil,
moisture and filtered to 10 microns minimum.
Incoming compressed air must not exceed 100
psig.
CARON recommends installing a pressure gauge, filter, and shutoff prior to the dryer
to monitor incoming air pressure. The air supply (either house air or other compressed
air source) must be 90 to 100psig at the air supply inlet. An oil-less compressor may
be used. A Sound Suppression Kit maybe used to reduce the dryer noise (contact
CARON service for details).
1. Attach Dryer Package to exterior chamber with four mounting screws.
2. Connect dryer package power cord and 3/8” orange tubing into the dryer panel
on the chamber
Mounting
Screws
Mounting
Screws
Power Cord
Connection
Tube
Connection