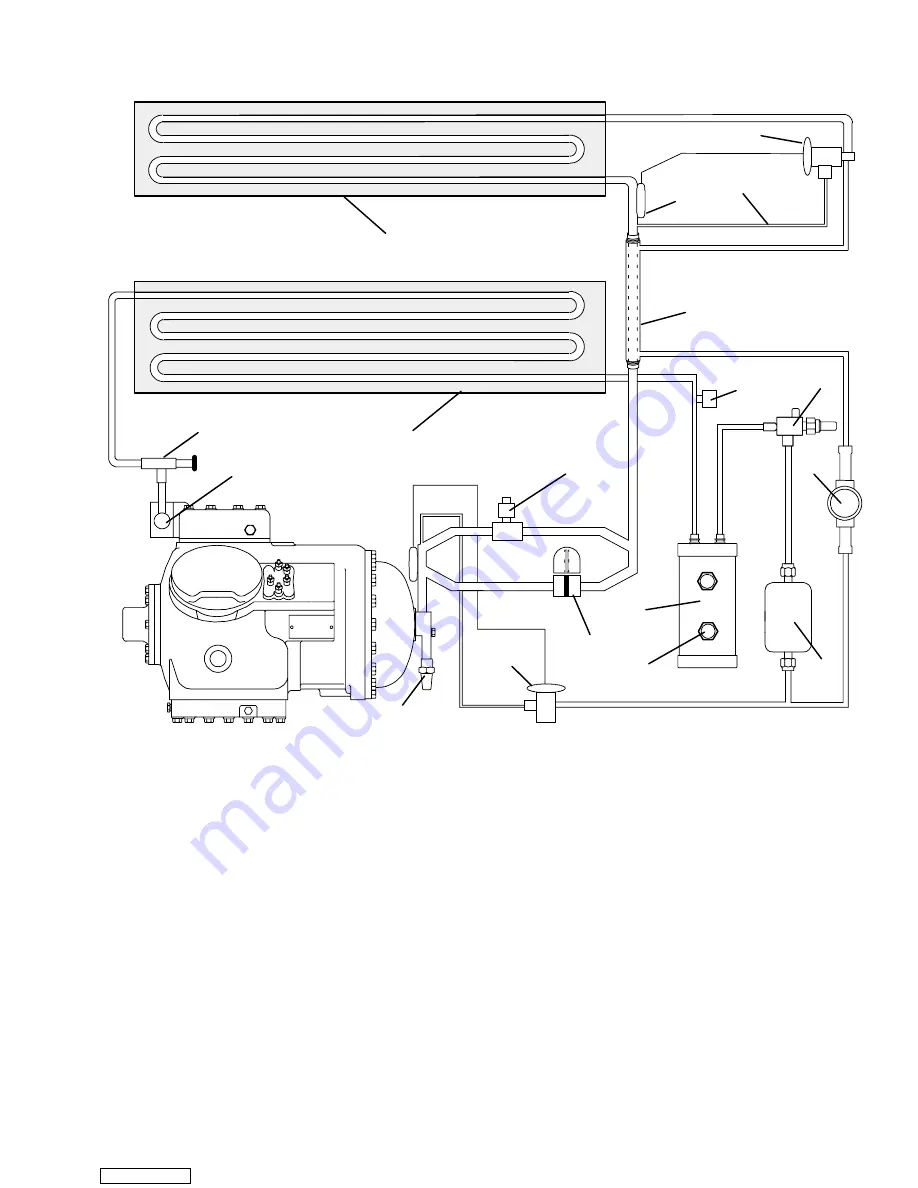
1-13
1. Suction Service Valve
2. Discharge Service Valve
3. Discharge Pressure Regulator Valve
4. Air-Cooled Condenser
5. Evaporator
6. Thermostatic Expansion Valve
7. External Equalizer Line
8. Thermostatic Expansion Valve Bulb
9. Heat Exchanger
10. Fusible Plug or
Rupture Disc (if equipped w/Water-Cooled
Condenser
11. Manual Liquid Line Valve
12. Moisture-Liquid Indicator
13. Filter-Drier
14. Sight Glass
15. Receiver or
Water-Cooled Condenser
16. Suction Solenoid Valve
17. Suction Modulation Valve
18. Quench Expansion Valve
1
2
3
4
5
6
7
8
9
11
12
13
14
15
16
17
18
10
Figure 1-7. Refrigeration Circuit
Downloaded from