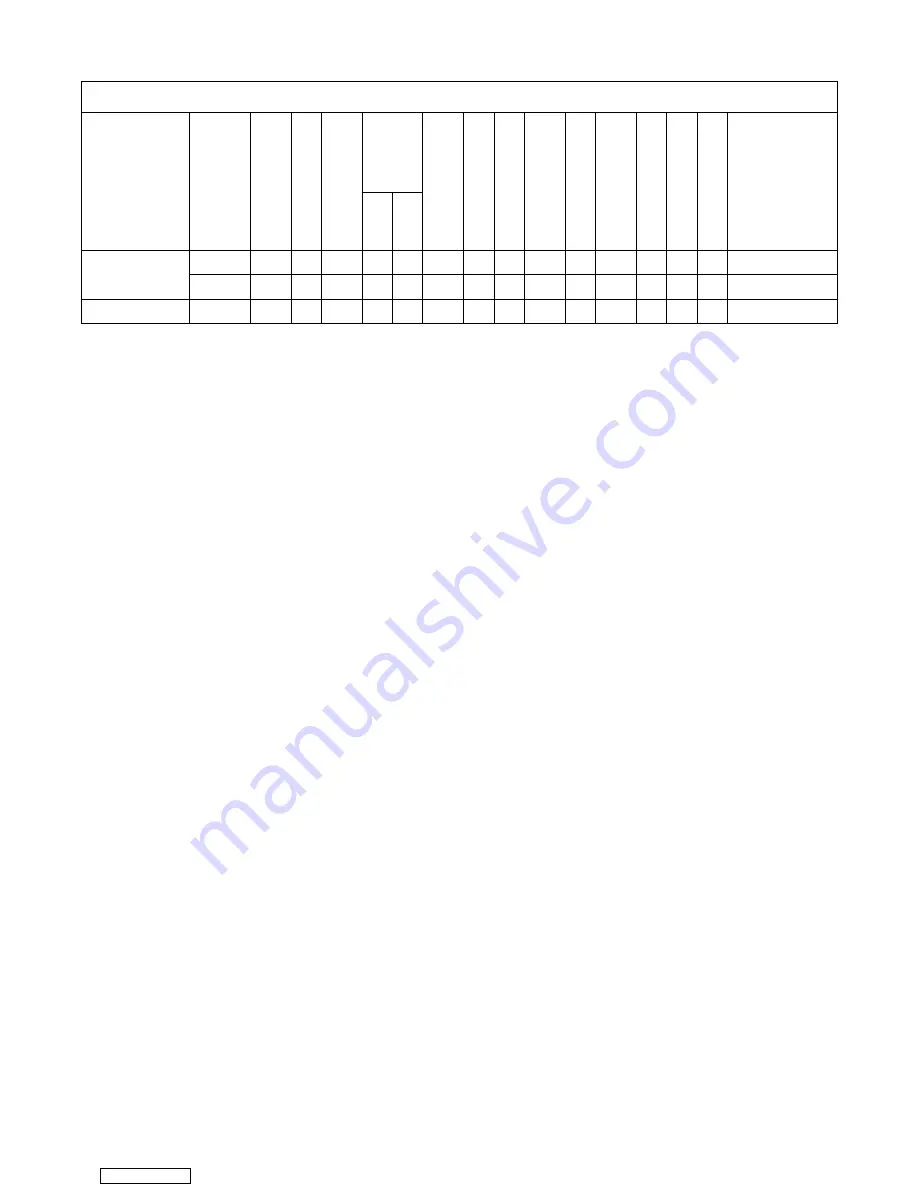
1-2
T-294-01
Table 1-1. Model Chart
MODEL
PID
A
Cold
tme
nt
sf
or
me
r
r-C
ooled
ens
er
Condens
er
Coil
Dis
ch
ar
ge
Op
tio
n
idif
icat
ion
nsF
re
sh
nic
at
ions
e
Mo
du
le
re
Rec
or
der
Fac
to
r
or(
PF
C)
Op
tio
n
eti
c
Un
it
e
Cont
ro
l
Box
Schematic & Diagra
MODEL
PID
US
DA
Tr
ea
tm
Tr
an
s
Wa
te
r-
Conde
3R
ow
4R
ow
Su
ct
io
n
&
D
Pre
ssu
re
O
Dehum
id
Tr
an
s
Co
mmu
ni
In
te
rfa
ce
Te
m
per
at
ur
e
Po
we
rF
a
Co
rre
ct
or
Arct
ic
O
Her
m
et
Com
pos
ite
g
69NT40 511 201
NT0448
P
X
X
--
X
--
P
--
X
--
X
--
X
--
77-01698-38
69NT40-511-201
NT0569
P
X
X
X
--
--
P
--
X
--
X
--
X
X
77-01698-60
69NT40-511-201 NT0602
P
X
X
X
--
--
P
X
X
--
X
--
X
X
77-01698-60
A = Factory Installed Pressure Gauges
B = Factory Installed Pressure Transducers
P = Provision
X = Features that apply to model
-- = Features that are
not applicable
to model
Downloaded from