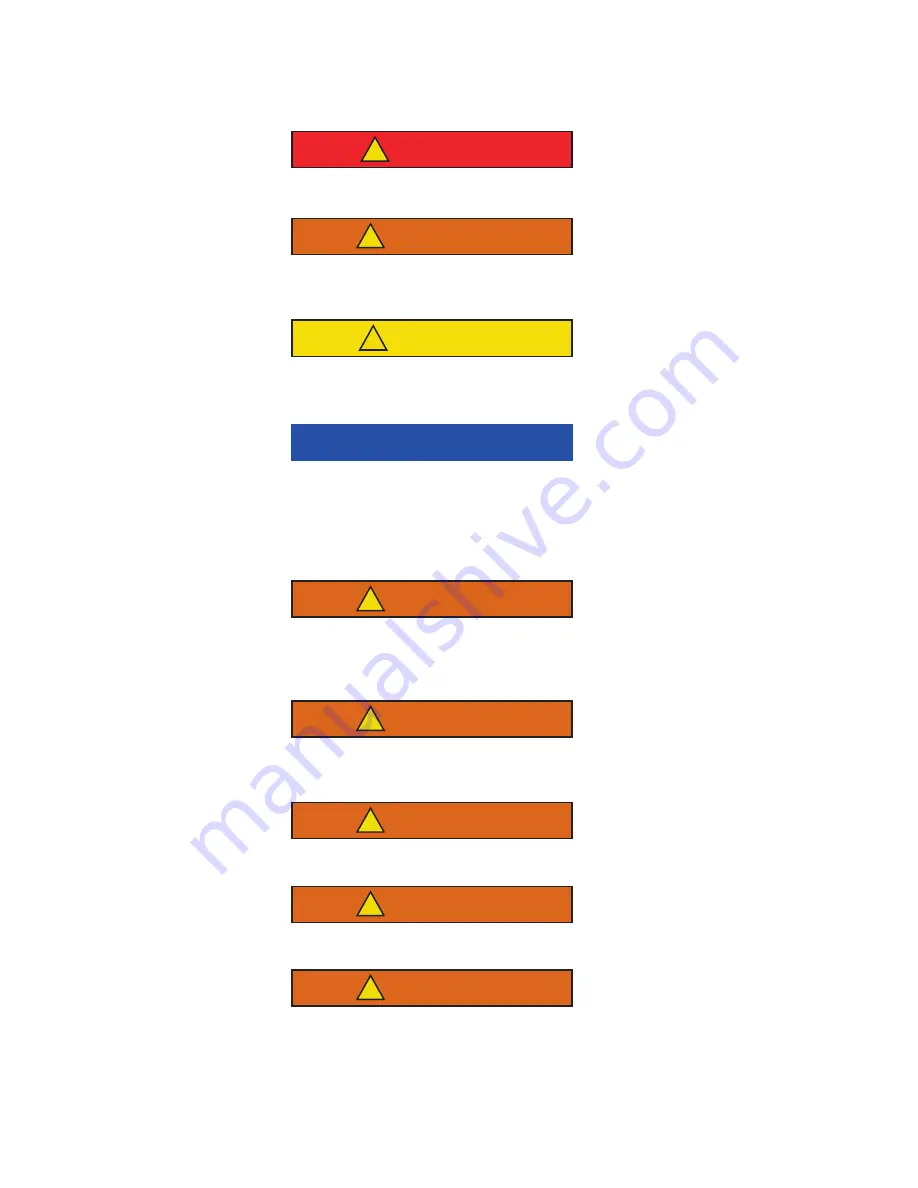
62-12023
1-2
1.6
Specific Warning, Caution, and Notice Statements
To help identify the label hazards on the unit and explain the level of awareness each one carries, an explanation is
given with the appropriate consequences:
DANGER
!
DANGER
−
warns against an immediate hazard which WILL result in severe personal injury or death.
WARNING
!
WARNING
−
warns against hazards or unsafe conditions which COULD result in severe personal
injury or death.
CAUTION
!
CAUTION
−
warns against potential hazard or unsafe practices which could result in minor personal
injury.
NOTICE
NOTICE
−
warns against potential product or property damage.
The statements listed below are specifically applicable to this refrigeration unit and appear elsewhere in this man-
ual. These recommended precautions must be understood and applied during operation and maintenance of the
equipment covered herein
.
WARNING
!
Beware of unannounced starting of the unit. The unit may cycle the fans and one of the operat-
ing compressors unexpectedly as control requirements dictate. To ensure unit is without
power, remove power plug and remove battery negative cable.
WARNING
!
Do not attempt to connect or remove power plug before ensuring the unit is OFF (press OFF
key on Cab Command) and external power circuit breaker is open.
WARNING
!
The power plug must be clean and dry before connecting to any power source.
WARNING
!
Beware of V-belt and belt-driven components as the unit may start automatically.
WARNING
!
Do not use a nitrogen cylinder without a pressure regulator. (See
) Cylinder pressure
is approximately 2350 psi (160 Bar). Do not use oxygen in or near a refrigerant system as an
explosion may occur.
Summary of Contents for Integra 35X
Page 2: ......
Page 8: ......
Page 12: ......
Page 68: ......
Page 69: ...wiring schematics ...
Page 70: ......
Page 71: ...wiring schematics ...
Page 72: ......
Page 73: ...wiring schematics ...
Page 74: ......
Page 75: ...wiring schematics ...
Page 76: ......
Page 79: ......