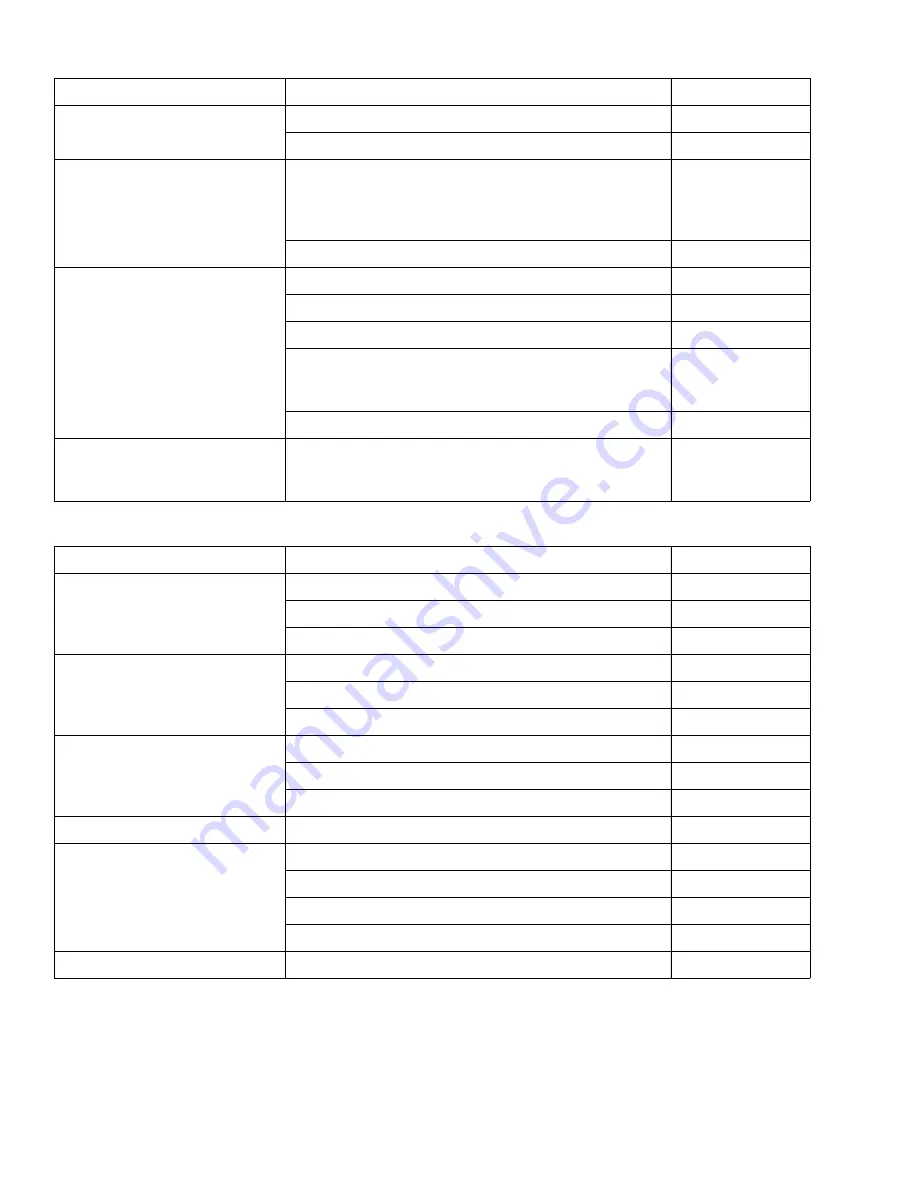
62-11640
9–4
9.2
BATTERY CHARGER
9.3
GENERATOR
Indication/Trouble
Possible Causes
Action / Reference
F33, F34, F35 fuse blown
Short in 12 volt wiring causing overload of charger
Internal short
Charging rate does not taper back
after charging for a few minutes of
engine crank
Bad cell in battery
Test battery for de-
fect according to
battery manufactur-
er’s instructions
Defective charger
Replace
Charger does not charge
Open F33 or F34 or F35
Replace
Charger is not receiving AC input
AC input exceeding design limits
Charger output is not connected to 12 volt battery
Check output wiring
connections to bat-
tery.
Defective charger
Replace
Low output voltage measured
across charger output
Battery not connected to charger.
It is normal to measure 12 volts or less across charger
output with no battery connected
Check charging
leads from charger
to battery
Indication/Trouble
Possible Causes
Action / Reference
No voltage with engine running
Damaged harness
Check
GENCON damaged
Check
Open or short in stator windings
Check
Low voltage
Low engine speed
Correct
Excessive load
Check
High resistance connections - connections warm or hot
Clean and Tighten
Fluctuating voltage
Fluctuating speed
Irregular speed of engine
Loose terminal or load connections
Tighten
High voltage
Excessive engine speed
Overheating
Generator overloaded
Check
Clogged ventilation openings
Clean
Insufficient circulation
Check Fan
Unbalanced load
Balance
Mechanical Noise
Loose laminations
Summary of Contents for Vector 8500
Page 23: ...62 11640 1 6 1 3 SAFETY DECALS ...
Page 24: ...1 7 62 11640 62 03958 ...
Page 25: ...62 11640 1 8 ...
Page 26: ...1 9 62 11640 ...
Page 27: ...62 11640 1 10 ...
Page 125: ...62 11640 SECTION 6 MESSAGECENTER PARAGRAPH NUMBER Page 6 1 MESSAGECENTER MESSAGES 6 1 ...
Page 321: ......
Page 322: ......