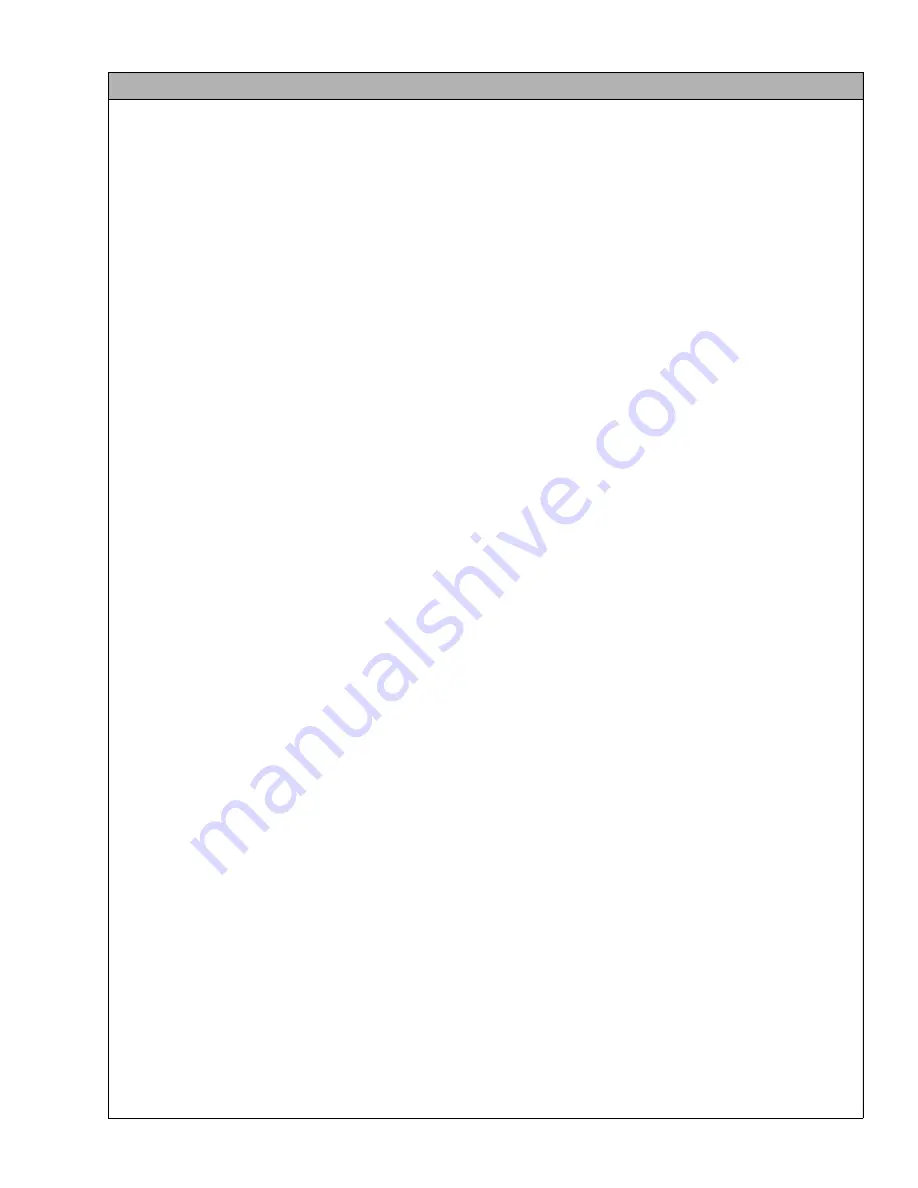
7–11
62-11640
00018
LOW REFRIGERANT PRESSURE
• ACTIVATION: Suction Pressure has been less than
−
6.3 psig (
−
0.43 bar) for the Low Suction Pressure
Configuration time or 10 seconds (whichever is less).
• UNIT CONTROL: Engine Operation: Engine and unit shutdown and alarm.
Electric Operation: Alarm only or (if configured for shutdown) refrigeration system
shutdown and alarm with PSCON still energized.
• RESET CONDITION: Auto Reset when suction pressure rises above 0.0 (bar or psig). Alarm may be
manually reset via keypad or by turning the unit OFF, then ON again.
NOTE: Follow the steps below until a problem is found. Once a repair or correction has been made, the active
alarm should clear itself (refer to reset condition above). Operate the unit through the appropriate modes to see
if any active alarm occurs. Continue with the steps below as necessary.
CORRECTIVE ACTIONS:
1.
Visually Inspect
Unit
Visually inspect unit for damage to liquid line causing restriction or signs of temperature drop at the
filter drier. All tubing from the receiver to the evaporator section must be in good condition. Verify that
there is no temperature drop at the drier or anywhere on the liquid line.
2.
Perform Pretrip
Check
Clear Active Alarm list, then run Pretrip & check for alarms. Any active alarms must be corrected and
cleared before proceeding.
3.
Check For Low Refrigerant
Charge
Check refrigerant level in the receiver. Refer to
. Generally, level should be between
upper & lower sight glasses with a refrigerated compartment temperature of 35°F (1.0°C) or lower.
4.
Manually Defrost
Unit
Defrost unit and terminate automatically. Typical defrost cycle time is 5
−
20 minutes. Suction pres-
sure should rise gradually during cycle.
5.
Check Evaporator
Section
Check evaporator section, return air bulkhead, air chute, and evaporator coil for cleanliness and air-
flow. Refer to
6.
Check System
Pressures
Install Manifold Test Set and check and compare compressor discharge & suction pressures with
those shown on the microprocessor. Suction pressure must be above 0.0 (psig or bar) Suction & Dis-
charge Pressures must have the same reading on gauges & on microprocessor display.
7. Check Transducer Wiring. Refer to
a. Inspect transducer & connector pins & terminals. (See wiring schematic
.) Verify that
there is no physical damage to sensor, and the pins in plug are not damaged or corroded.
b. Check for voltage at the transducer plug between pins A (+) and B (ground). Voltage should be
approximately12VDC.
c. Reconnect the transducer plug. Check for voltage between 1MP
−
29 and ground. Voltage should
be greater than 0.24 VDC and less than 5 VDC.
8.
Check Compressor Suction Modulation Valve
(CSMV)
Check CSMV. Refer to
.
9.
Check Expansion Valve
(EVXV)
a. Visually inspect valve. Check coil is seated properly.
b. Check operation of valve. Refer to
.
Summary of Contents for Vector 8500
Page 23: ...62 11640 1 6 1 3 SAFETY DECALS ...
Page 24: ...1 7 62 11640 62 03958 ...
Page 25: ...62 11640 1 8 ...
Page 26: ...1 9 62 11640 ...
Page 27: ...62 11640 1 10 ...
Page 125: ...62 11640 SECTION 6 MESSAGECENTER PARAGRAPH NUMBER Page 6 1 MESSAGECENTER MESSAGES 6 1 ...
Page 321: ......
Page 322: ......