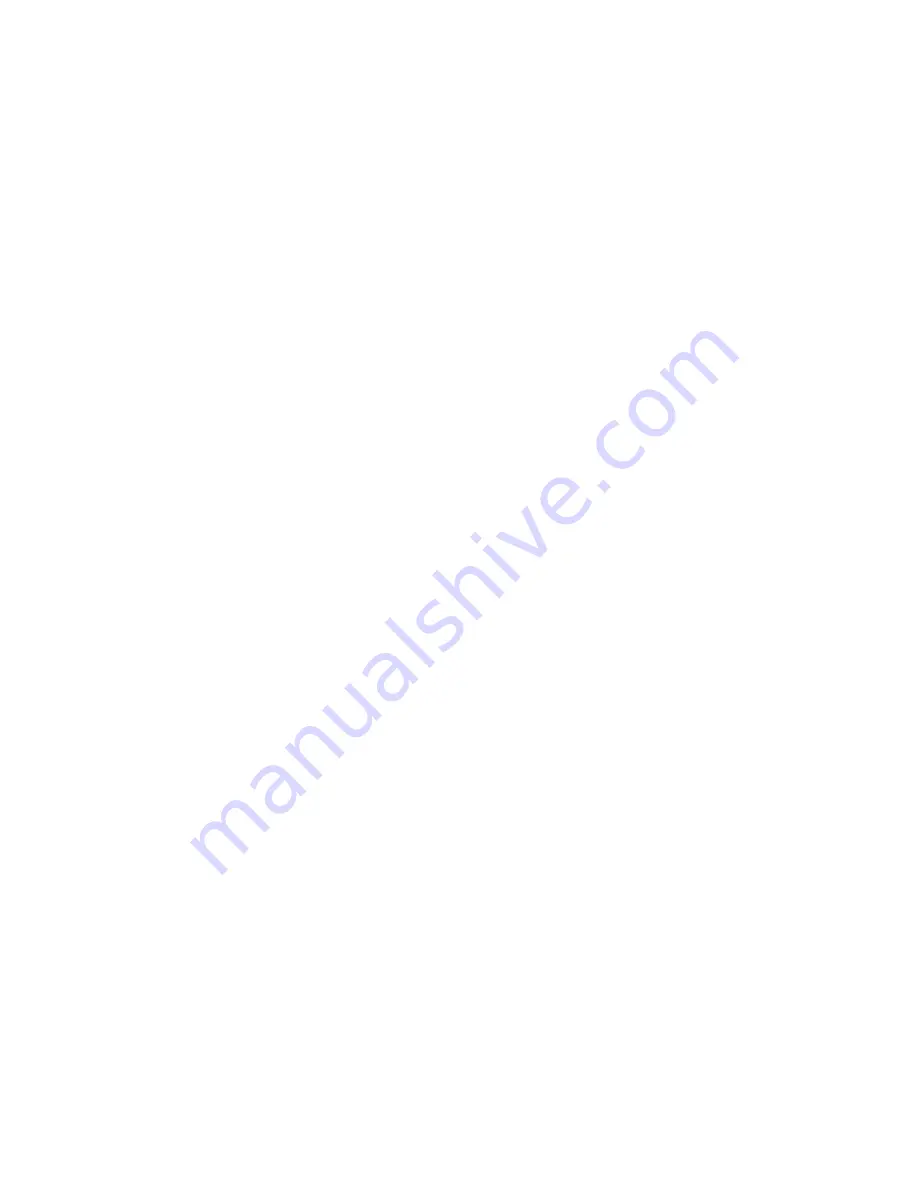
4–1
62-11640
SECTION 4
ENGINE AND TEMPERATURE CONTROL
NOTES
1. If the unit is in an alarm condition, the control system alarm response may override the operation described
herein. If an alarm is displayed in the MessageCenter, refer to the specific alarm description in Section 7 for
“Unit Control” descriptions.
2. With the complex control interactions in use with the APX control system there are many user selected and
preprogrammed software overrides which may change the operation of the unit. Refer to
&
for complete descriptions of these features.
4.1
INTRODUCTION
This section describes operation of the unit when
power is supplied from an external source
−
Electric
Operation and when power is supplied by the internal
generator
−
Engine Operation. The section also
describes two additional sub
−
categories of operation;
Start-Stop Operation and Continuous Operation.
For a description and flow diagram of the refrigerant
system component interaction while in cooling, refer to
. For a description of the system compo-
nent interaction in heating or defrost, refer to
.
4.2
SEQUENCE OF OPERATION - ELECTRICAL
With the battery connected (see schematic diagram
), power is available from the battery
through fuse F7:
• and fuse F1 to the module logic circuit at main
microprocessor module (MM) terminal 1MM
−
6,
to the stepper valve module (from 1MM
−
8 and
SP
−
16 to 1SMV
−
6), to the display module (from
1SVM
−
8 to DM
−
10), to the first contactor control
board (1CCB) (from SP
−
16 through HVB7
−
B
and HVB1
−
B and SP52 to 1CCB
−
04) and to the
second contactor control board (2CCB) (from
SP
−
52 to 2CCB
−
04).
• and fuse F3, PCM
−
34 and SP
−
18 to SVM at
2SVM
−
22 & 3SVM
−
22 (for operation of the
valves), and ENCU
−
22 (for the ENCU logic cir-
cuit).
Potential power is also established for the starter sole-
noid contactor (SSC) normally open contacts, the bat-
tery charger logic circuit (BTYC TEMP/VOLTAGE), the
engine preheat transistor (EPHT), fuel heater relay
(FHR) normally open contacts, AutoFresh Air relay
(AFAR) normally open contacts, power enable relay
(PER) normally open contacts (through fuse F5), and
the buzzer (B + through fuse F1).
Once the module logic circuit is powered, the modules
begin to communicate over the controlled area network
(CAN).
The “HI” CAN connectivity is established from the main
microprocessor (1MM
−
2, through connectors HVB7
−
C
& HVB1
−
C) to the first contactor control board (at ter-
minal 1CCB
−
05) and to the second contactor control
board (from 1CCB
−
06 to terminal 2CCB
−
06). The con-
nectivity continues (from 2CCB
−
05 and through termi-
nals HVB1
−
H and HVB7
−
H) to SP
−
13. From SP
−
13
the connectivity continues to the ENCU (at terminal
ENCU
−
23), to the stepper valve module (at 1SVM
−
5)
and to the display module (from 1SVM
−
2 to DM
−
2).
The “LO” CAN connectivity is established from the
main microprocessor (1MM
−
4, through connectors
HVB7
−
D & HVB1
−
D) to the first contactor control
board (at terminal 1CCB
−
17) and to the second con-
tactor control board (from 1CCB
−
29 to terminal
2CCB
−
29). The connectivity continues (from 2CCB
−
17
and through terminals HVB1
−
G and HVB7
−
G) to
SP
−
14. From SP
−
14 the connectivity continues to the
ENCU (at terminal EN CU
−
24), to the stepper valve
module (at 1SVM
−
7) and to the display module (from
1SVM
−
4 to DM
−
6).
To start the unit, SROS is placed in the START/RUN
position. Power flows from SROS through terminal
DM
−
7, the J1 jumper, the high pressure switch (HPS)
and the overload ground fault (through terminal
HVB1
−
K, OV
−
+12V OV
−
S+, SP
−
63, terminals
HVB1
−
F & HVB7
−
F and PCM
−
15) to the power enable
relay (PER) coil. Confirmation of power circuits are
established from splice point SP
−
24 back to the main
microprocessor at 2MM
−
35, SP
−
23 to 3MM
−
16 and
from SP
−
63 to the second contactor control board at
2CCB
−
12. If any of these circuits is broken, the appro-
priate alarm will be activated.
If conditions are correct for operation, the main micro-
processor will energize Power Enable Relay (PER) by
providing ground through PCM16 from 3MM18. Ener-
gizing PER closes its normally open contacts to pro-
vide power:
• through fuse F10 to the main microprocessor at
3MM
−
34 & 3MM
−
23.
• through fuse F12 for satellite communication
(SATPWR).
Summary of Contents for Vector 8500
Page 23: ...62 11640 1 6 1 3 SAFETY DECALS ...
Page 24: ...1 7 62 11640 62 03958 ...
Page 25: ...62 11640 1 8 ...
Page 26: ...1 9 62 11640 ...
Page 27: ...62 11640 1 10 ...
Page 125: ...62 11640 SECTION 6 MESSAGECENTER PARAGRAPH NUMBER Page 6 1 MESSAGECENTER MESSAGES 6 1 ...
Page 321: ......
Page 322: ......