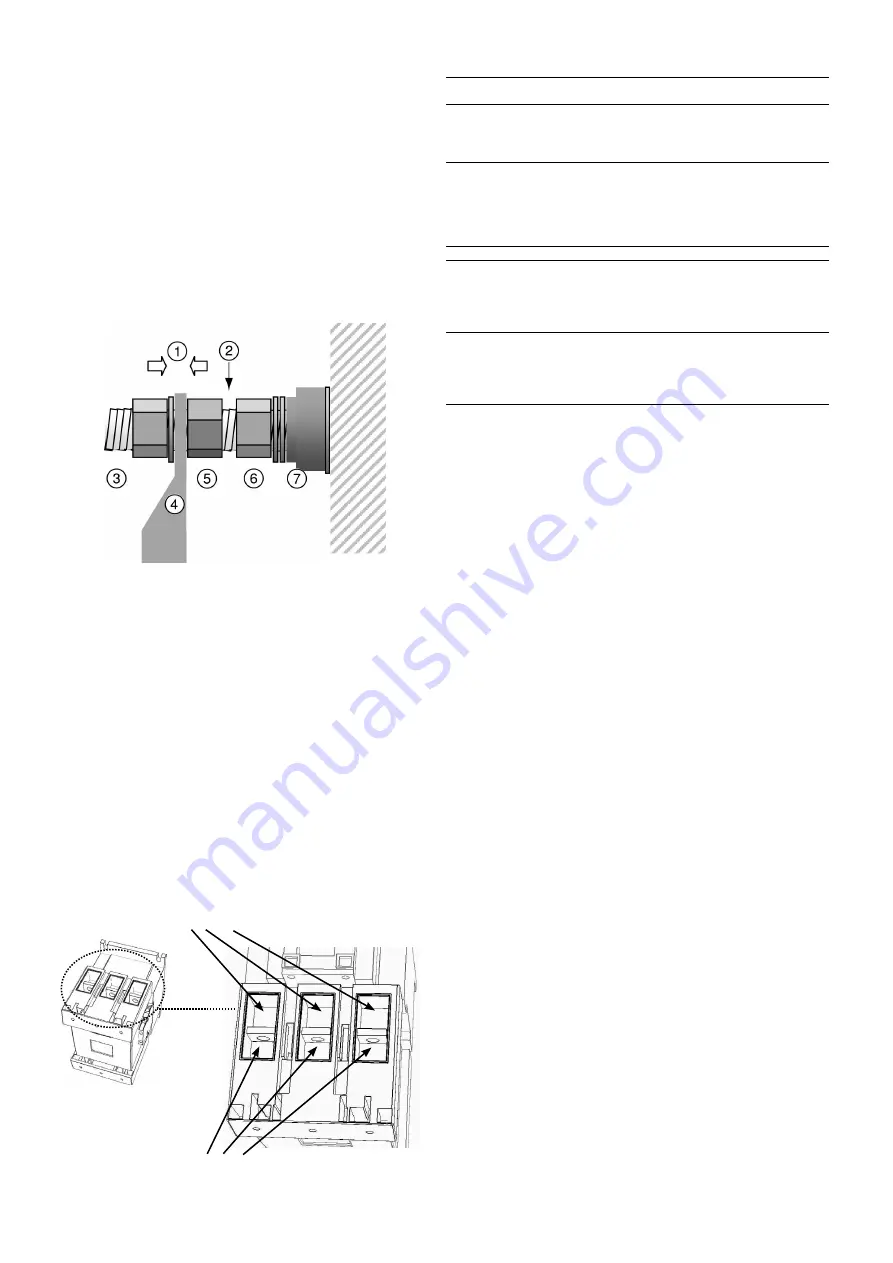
32
13.5 - Tightening torques for the main bolts and screws
Screw type
Used for
Torque
value, N·m
M20 nut
Chassis
190
M20 nut
Heat exchanger side-side connection
240
M16 nut
Compressor fixing
190
H M16 screw
Heat exchanger water boxes, structure
190
H M16 screw
Compressor suction flanges TT
190
H M20 screw
Compressor suction flanges TU & TV
240
M16 nut
Compressor discharge line TT & TU
190
M20 nut
Compressor discharge line TV
240
H M12 screw
Economiser port flange & economiser port
valve, option 92
80
H M8 screw
Drier cover
35
1/8 NPT connection
Oil line
12
TE nut
Compressor oil line
24,5
7/8 ORFS nut
Oil line
130
5/8 ORFS nut
Oil line
65
3/8 ORFS nut
Oil line
26
H M6 screw
Stauff collar
10
Taptite screw M6
Oil line collar
7
Taptite screw M6
Brass body, economiser line
10
Metric screw M6
Steel plate fixing, control box, terminal box
7
Taptite screw M10 Oil filter, economiser module, control box fixing
30
13.6 - Evaporator and condenser maintenance
Check that:
•
the insulating foam is intact and securely in place,
•
the sensors and flow switch are correctly operating
and correctly positioned in their support,
•
the water-side connections are clean and show no sign
of leakage.
13.7 - Compressor maintenance
13.7.1 - Oil filter change schedule
As system cleanliness is critical to reliable system operation,
there is a filter in the oil line at the oil separator outlet. The
oil filter is specified to provide a high level of filtration (5 µm)
required for long compressor life.
The filter should be checked after the first 500 hours of
operation, and every subsequent 2000 hours. The filter should
be replaced at any time when the pressure differential
across the filter exceeds 2 bar.
The pressure drop across the filter can be determined by
measuring the pressure at the discharge port (at the oil
separator) and the oil pressure port (at the compressor).
The difference in these two pressures will be the pressure
drop across the filter, check valve, and solenoid valve. The
pressure drop across the check valve and solenoid valve is
approximately 0.4 bar, which should be subtracted from the
two oil pressure measurements to give the oil filter pressure
drop.
13.4.3 - Connection precautions for the power contactors
These precautions must be applied for units equipped with
06TUA554, 06TVW753 and 06TVW819 compressors. For
these units the power contactor type is 3RT1064 (Siemens).
The contactors allow two connection positions in the cage
clamps. But only one position allows safe and reliable
tightening on the contactor (KM1 or KM2). The conductor
must be positioned in front of the connection area when it
is tightened. If it is tightened behind the area, there is a risk
that the brackets will be damaged during the tightening.
Conductor position
NOT ALLOWED
COMPULSORY
conductor position
13.4.2 - Connection precautions for the compressor power
terminals
These precautions must be applied during an intervention
that requires the removal of the power conductors connected
to the compressor supply terminals.
The tightening nut of terminal (6) supporting the isolator
(7) must never be loosened, as ist ensures terminal tightness
and compressor leak tightness.
The tightening of phase lug (4) must apply the torque
between counter nut (5) and tightening nut (3): during this
operation a counter-torque must be applied at counter nut
(5). Counter-nut (5) must not be in contact with the tightening
nut of terminal (6).
1. Torque application to tighten the lug
2. Avoid contact between the two nuts
3. Lug tightening nut
4. Flat lug
5. Counter-nut
6. Terminal tightening nut
7. Isolator