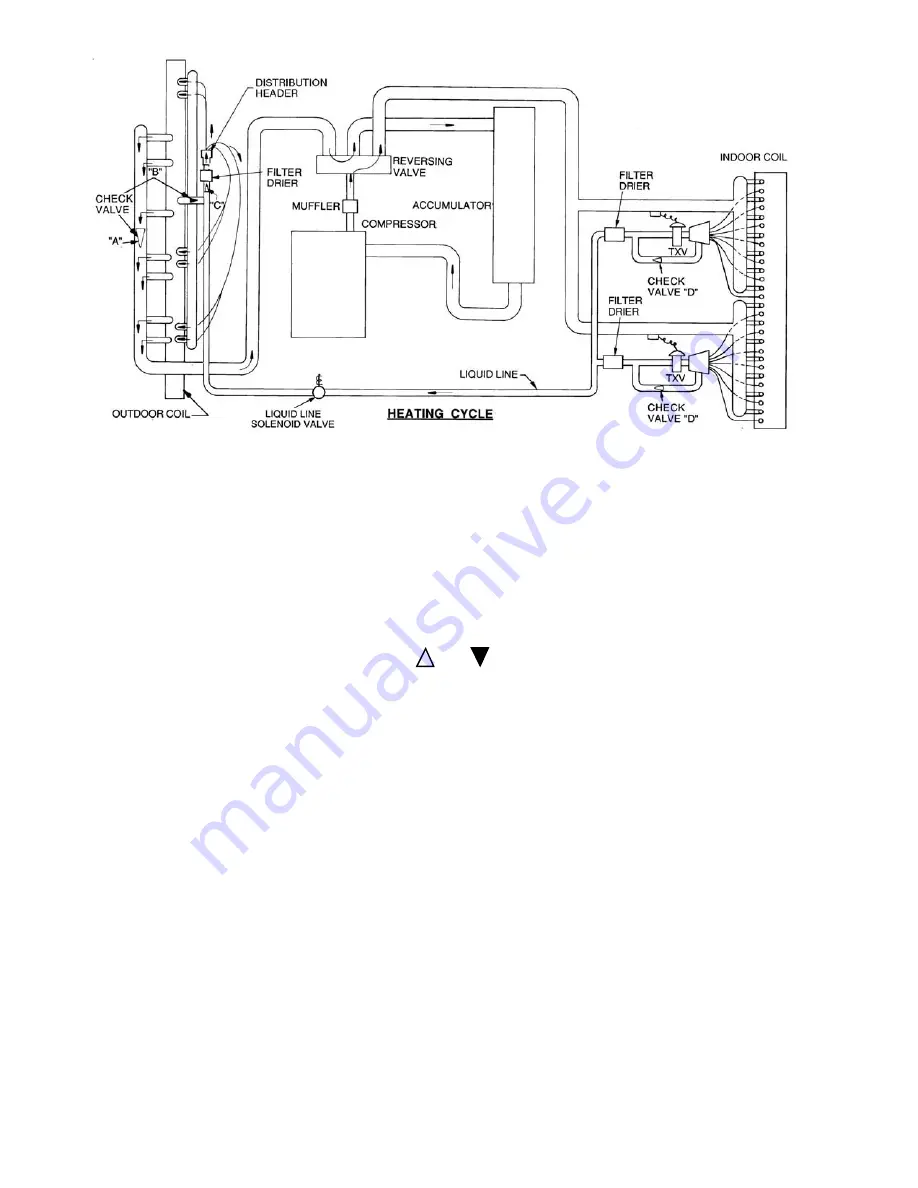
22
1. Hot gas from compressor flows through the reversing (4-way)
valve and is directed to the indoor coil header. At the header
refrigerant is directed to the indoor coil where it is condensed
and subcooled and then exits through the indoor coil check
valve to the liquid line. (The TXVs stop the refrigerant flow dur-
ing the heating cycle.)
2. The refrigerant then feeds the outdoor coil by way of filter-drier,
a distribution manifold, and then through capillary tubes on
each circuit.
3. Each circuit evaporates the refrigerant and all the circuits are
combined in the outdoor header (with some of the circuits flow-
ing through the check valve “A”).
4. The refrigerant then flows through the reversing (4-way) valve,
accumulator and back to the compressor.
LEGEND
NOTES:
1. Check valves are designated “A” through “D.”
2. Illustrations are typical and do not portray exact coil circuiting.
3. Check valve positions:
open,
closed.
TXV —
Thermostatic Expansion Valve
Fig. 17 — Typical Heat Pump Heating Operation Schematic
(38AQS012 Shown)