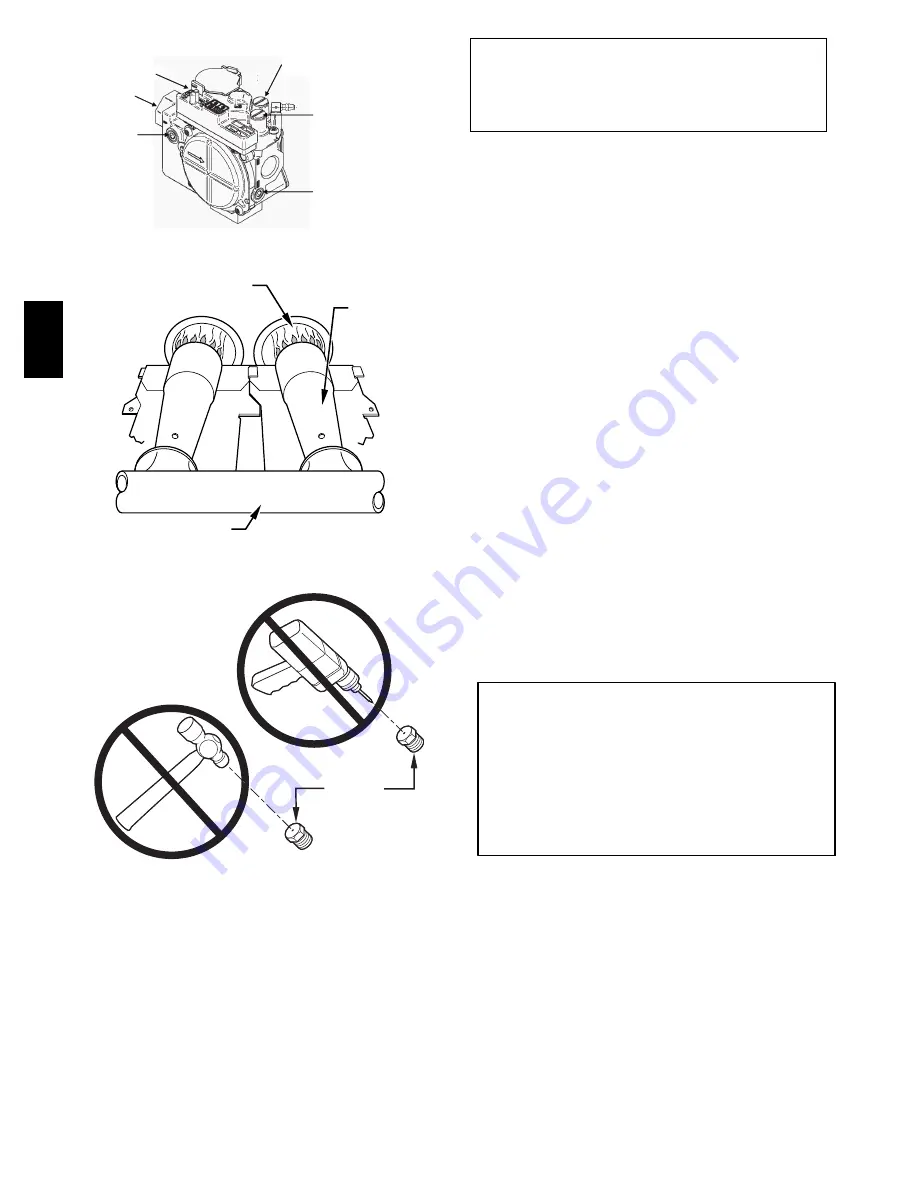
58
ON/OFF Switch
½” NPT Inlet
1/8” NPT Inlet
Pressure Tap
High Stage Regulator Seal Cap
Regulator Adjustment Under Cap
Low Stage Regulator Seal Cap
Regulator Adjustment Under Cap
1/8” Manifold
Pressure Tap
A07537
Fig. 58 -- Redundant Automatic Gas Control Valve
;;
;;
BURNER FLAME
BURNER
MANIFOLD
A89020
Fig. 59 -- Burner Flame
BURNER
ORIFICE
A93059
Fig. 60 -- Burner Orifice
3. Verify Natural Gas Input Rate By Clocking Gas Meter.
NOTE
: Be sure all pressure tubing, combustion-air and vent
pipes, and burner enclosure front are in place when checking
input by clocking gas meter.
a. Calculate high-altitude adjustment (if required).
UNITED STATES
At altitudes above 2000 ft (610 M), this furnace has
been approved for 2 percent derate for each 1000 (505
M) ft above sea level. See Example and Table 15 for
derate multiplier factor.
EXAMPLE:
100,000 Btuh input furnace installed at 4300 ft (1310 M).
Furnace Input Rate
at Sea Level
X
Derate
Multiplier
=
Furnace Input Rate
at Installation
Factor
Altitude
100,000
X
0.91
=
91,000
CANADA
At installation altitudes from 2001 to 4500 ft (610 to
1372 M), this furnace must be derated 5 percent by an
authorized Gas Conversion Station or Dealer. To
determine correct input rate for altitude, see example
above and use 0.95 as derate multiplier factor.
b. Reinstall burner box cover.
NOTE
: Clocking gas input rate MUST always be performed
with the burner box cover INSTALLED.
c. Check that gas valve adjustment caps are in place for
proper input to be clocked.
d. Obtain yearly heat value average for local gas supply.
NOTE
: Be sure heating value of gas used for calculations is
correct for your altitude. Consult local gas utility for altitude
adjustment of gas heating value.
e. Check and verify orifice size in furnace. NEVER
ASSUME THE ORIFICE SIZE. ALWAYS CHECK
AND VERIFY.
f. Turn off all other gas appliances and pilots.
g. Move setup switch SW-1 to ON position. This keeps
furnace locked in low-heat operation.
h. Jumper R-to-W/W1.
i. Let furnace run for 3 minutes in low-heat operation.
j. Measure time (in sec) for gas meter to complete 1
revolution. Note reading.
k. Refer to Table 17 for cubic ft of gas per hr.
l. Multiply gas rate cu ft/hr by heating value (Btu/cu ft).
m. Move setup switch SW-1 to OFF position and jumper
R and W1 and W2 thermostat connections. This keeps
furnace locked in high-heat operation. Repeat items ‘i’
through ‘l’ for high-heat operation.
Example:
(0 -- 2000 ft (610 M) altitude)
Furnace input from rating plate is 100,000 Btuh.
Btu heating input = Btu/cu ft X cu ft/hr
Heating value of gas = 975 Btu/cu ft
Time for 1 revolution of 2-cu ft dial = 70 sec
Gas rate = 103 cu ft/hr (from Table 17)
Btu heating input = 103 X 975 = 100,425 Btuh. In this
example, the orifice size and manifold pressure adjustment
is within
±
2 percent of the furnace input rate.
NOTE
: Measured gas inputs (high-heat and low-heat) must be
within
±
2 percent of that stated on furnace rating plate when
installed at sea level or derated per that stated above when
installed at higher altitudes.
n. Remove jumper across R, W/W1, and W2 thermostat
connections to terminate call for heat.
58MEC