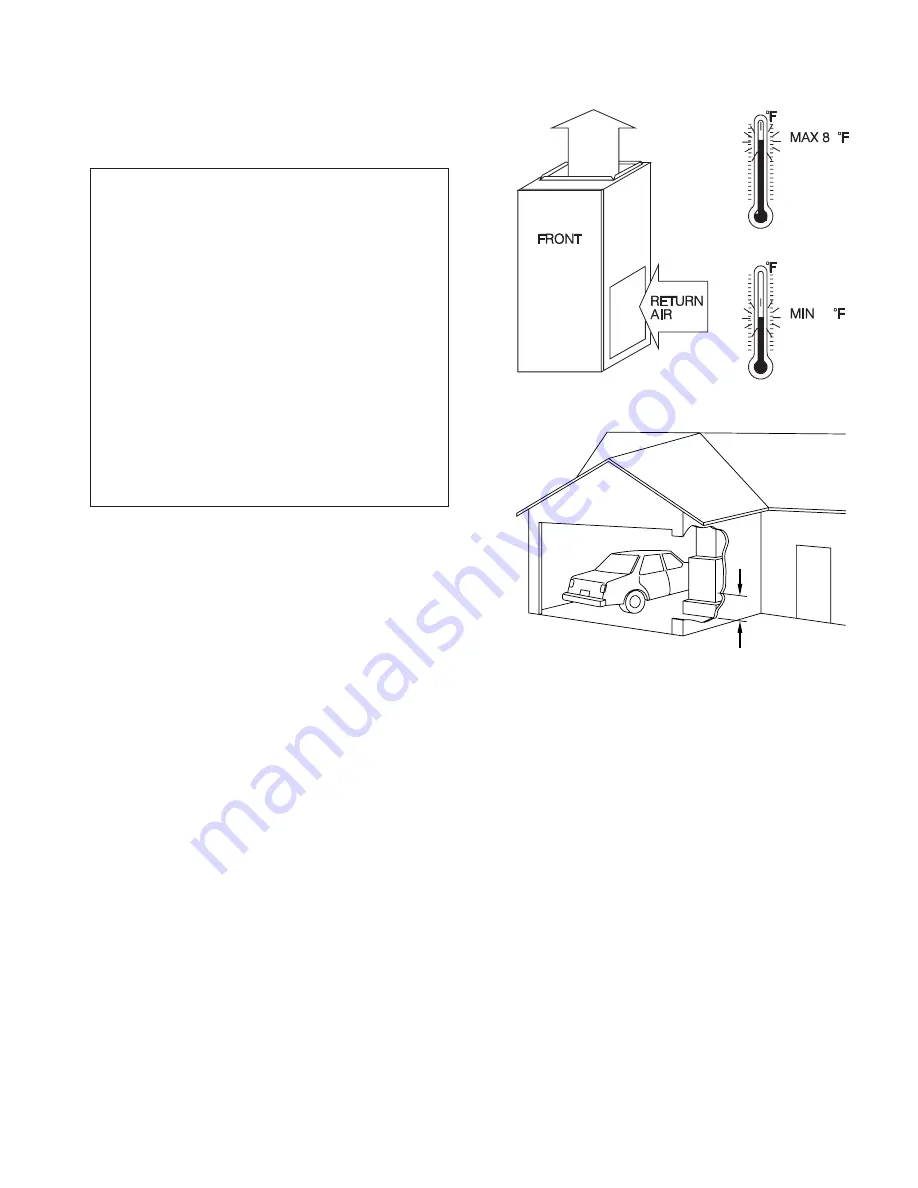
from the outside atmosphere and all flue products are discharged to
the outside atmosphere. See furnace and factory accessory termi-
nation kit instructions for proper installation.
These furnaces are shipped with the following materials to assist in
proper furnace installation. These materials are shipped in the main
blower compartment.
The furnace shall be installed so that the electrical components are
protected by water.
For accessory installation details, refer to applicable installation
literature.
CODES AND STANDARDS
Follow all national and local codes and standards in addition to
these instructions. The installation must comply with regulations
of the serving gas supplier, local building, heating, plumbing, and
other codes. In absence of local codes, the installation must
comply with the national codes listed below and all authorities
having jurisdiction in Canada.
In the United States and Canada, follow all codes and standards for
the following:
Step 1—Safety
•
US: National Fuel Gas Code (NFGC) NFPA 54-2002/ANSI
Z223.1-2002 and the Installation Standards, Warm Air Heating
and Air Conditioning Systems ANSI/NFPA 90B
•
CANADA: National Standard of Canada, Natural Gas and
Propane Installation Code (NSCNGPIC) CSA B149.1-05
Step 2—General Installation
•
US: NFGC and the NFPA 90B. For copies, contact the National
Fire Protection Association Inc., Batterymarch Park, Quincy,
MA 02269; or for only the NFGC contact the American Gas
Association, 400 N. Capitol, N.W., Washington DC 20001
•
A manufactured (Mobile) home installation must conform with
the Manufactured Home Construction and Safety Standard,
Title 24 CFR, Part 3280, or when this standard is not
applicable, the Standard for Manufactured Home Installation
(Manufactured Home Sites, Communities, and Set-Ups),
ANSI/NCS A225.1, and/or CAN/CSA-Z240, MH Series Mobile
Homes
•
CANADA: NSCNGPIC. For a copy, contact Standard Sales,
CSA International, 178 Rexdale Boulevard, Etobicoke (Tor-
onto), Ontario, M9W 1R3, Canada.
Step 3—Combustion and Ventilation Air
•
US: Section 8.3 of the NFGC, Air for Combustion and
Ventilation
•
CANADA: Part 7 of the NSCNGPIC, Venting Systems and Air
Supply for Appliances
Step 4—Duct Systems
•
US and CANADA: Air Conditioning Contractors Association
(ACCA) Manual D, Sheet Metal and Air Conditioning Con-
tractors National Association (SMACNA), or American Soci-
ety of Heating, Refrigeration, and Air Conditioning Engineers
(ASHRAE) 2001 Fundamentals Handbook Chapter 34.
Step 5—Acoustical Lining and Fibrous Glass Duct
•
US and CANADA: current edition of SMACNA, NFPA 90B as
tested by UL Standard 181 for Class I Rigid Air Ducts
Step 6—Gas Piping and Gas Pipe Pressure Testing
•
US: NFGC; chapters 5, 6, 7, and 12 and national plumbing
codes
•
CANADA: NSCNGPIC Parts 3, 4, 5, A, B, E, G, and H
In the state of Massachusetts:
•
This product must be installed by a licensed plumber or gas
fitter.
•
When flexible connectors are used, the maximum length shall
not exceed 36 inches.
Installer Packet includes:
Installation, Startup, and Operating Instructions
Service and Maintenance Instructions
User’s Information Manual
Warranty Certificate
Loose Parts Bag includes:
Quantity
Pressure tube extension
1
Collector Box or condensate trap extension tube
1
Inducer housing drain tube
1
1/2-in CPVC street elbow
2
Drain tube coupling
1
Drain tube coupling grommet
1
Gas line grommet
1
Vent pipe grommet
1
Combustion-air pipe grommet
1
Gas line entry hole filler plug
1
Power entry hole filler plug
2
Condensate trap hole filler plug
3
Vent and combustion-air intake hole filler plug
2
Combustion-air pipe perforated disk assembly
1
Fig. 4—Return-Air Temperature
A05004
60
0
Fig. 5—Installation in a Garage
A93044
18-IN. MINIMUM
TO BURNERS
5
→
→
→
→