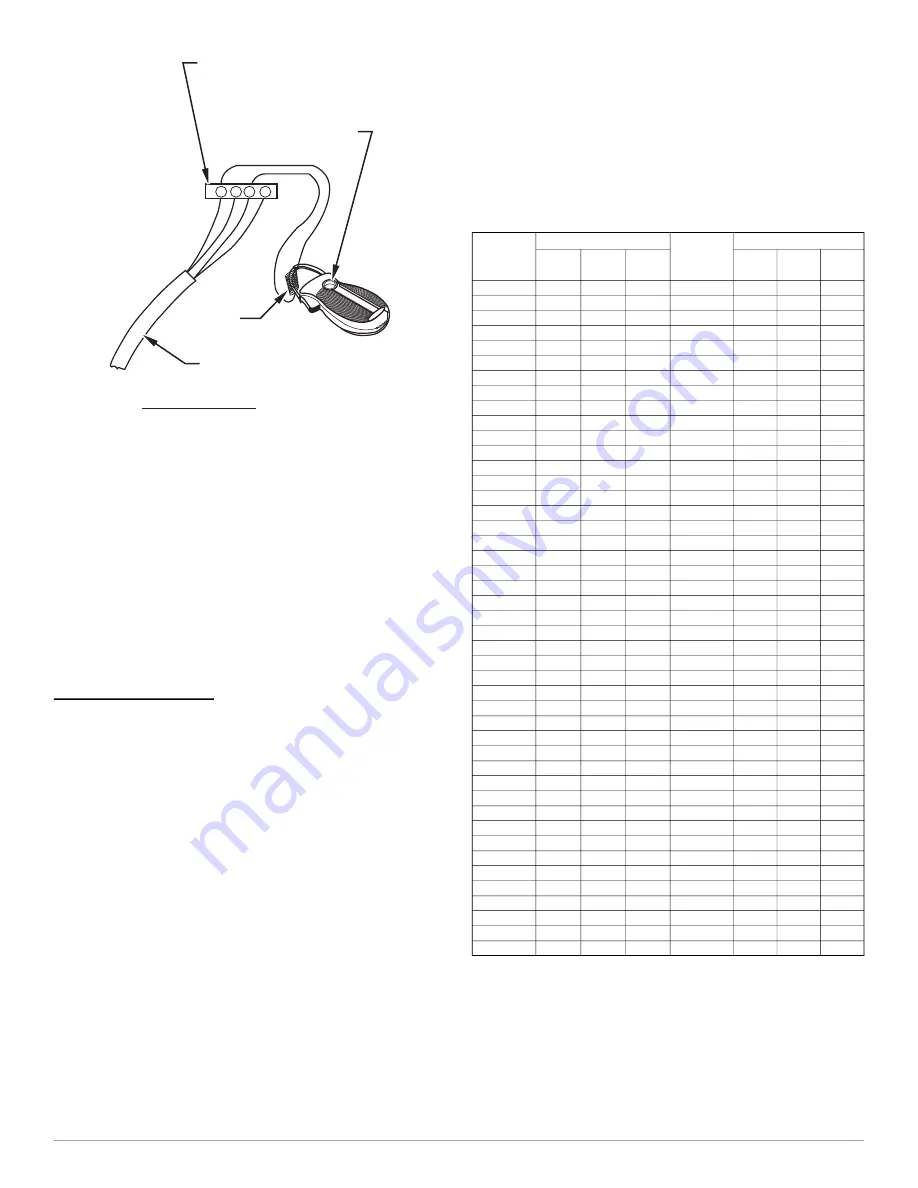
PG95ESU: Installation, Start-up, Operating and Service Maintenance Instructions
Manufacturer reserves the right to change, at any time, specifications and designs without notice and without obligations.
47
A96316
Fig. 62 – Amp. Draw Check With Ammeter
b. Electronic thermostat: Set cycle rate for 4 cycles per hr.
9. Adjust Cooling Airflow. The cooling airflow can be set from the
remaining blower speed taps. Refer to the Air Delivery Tables in
these instructions.
10. Adjust blower off delay. The blower off delay has four (4)
adjustable settings from 90 seconds to 180 seconds. The blower off
delay jumpers are located on the furnace control board - see wiring
diagram (see
). Position A-90 seconds, B-120 seconds,
C-150 seconds, D-180 seconds.
To change the blower off delay setting, move the jumper from one
set of pins on the control to the pins used for the selected blower off
delay. Factory off delay setting is 120 seconds.
11. Cooling On Delay is fixed at 2 seconds for either jumper selection.
Check Safety Controls
1. Check Main Limit Switch(es)
This control shuts off combustion control system and energizes
air-circulating blower motor, if furnace overheats. By using this
method to check limit control, it can be established that limit is
functioning properly and will operate if there is a restricted duct
system or motor failure. If limit control does not function during
this test, cause must be determined and corrected.
a. Run furnace for at least 5 minutes.
b. Gradually block off return air with a piece of cardboard or sheet
metal until the limit trips.
c. Unblock return air to permit normal circulation for 5 minutes.
d. Main limit circuit open causes 3 hour lock out.
e. Reset unit power to clear limit fault lockout.
Checklist
1. Put away tools and instruments. Clean up debris.
2. Verify that the Blower/Heat Off Delay jumpers are set as desired.
(see
and
).
3. Verify that there are no unsealed openings in the blower shelf or
casing.
4. Verify that the blower (lower door in upflow position) and control
(“Main” or upper door in upflow position) doors are properly
installed.
5. Verify that the Status LED glows. If not, check that the power
supply is energized and that the blower door is secure. Interpret
).
6. Cycle test furnace with room thermostat to be sure that it operates
properly with the room thermostat. Check all modes including
Heat, Cool and Fan.
7. Check operation of accessories per manufacturer’s instructions.
8. Review Owner’s Manual with owner.
9. Attach entire literature packet to furnace.
R
Y W G
10 TURNS
THERMOSTAT SUBBASE
TERMINALS WITH
THERMOSTAT REMOVED
(ANITICIPATOR, CLOCK, ETC.,
MUST BE OUT OF CIRCUIT.)
HOOK-AROUND
AMMETER
EXAMPLE:
5.0 AMPS ON AMMETER
10 TURNS AROUND JAWS
=
0.5 AMPS FOR THERMOSTAT
ANTICIPATOR SETTING
FROM UNIT 24-V
CONTROL TERMINALS
Table 21 – Gas Rate (CU ft./hr)
SEC
FOR 1
REV
SIZE OF TEST DIAL
SEC
FOR 1
REV
SIZE OF TEST DIAL
1 Cu
Ft.
2 Cu
Ft.
5 Cu
Ft.
1 Cu
Ft.
2 Cu
Ft.
5 Cu
Ft.
10
360
720
1800
55
65
131
327
11
327
655
1636
56
64
129
321
12
300
600
1500
57
63
126
316
13
277
555
1385
58
62
124
310
14
257
514
1286
59
61
122
305
15
240
480
1200
60
60
120
300
16
225
450
1125
62
58
116
290
17
212
424
1059
64
56
112
281
18
200
400
1000
66
54
109
273
19
189
379
947
68
53
106
265
20
180
360
900
70
51
103
257
21
171
343
857
72
50
100
250
22
164
327
818
74
48
97
243
23
157
313
783
76
47
95
237
24
150
300
750
78
46
92
231
25
144
288
720
80
45
90
225
26
138
277
692
82
44
88
220
27
133
267
667
84
43
86
214
28
129
257
643
86
42
84
209
29
124
248
621
88
41
82
205
30
120
240
600
90
40
80
200
31
116
232
581
92
39
78
196
32
113
225
563
94
38
76
192
33
109
218
545
96
38
75
188
34
106
212
529
98
37
74
184
35
103
206
514
100
36
72
180
36
100
200
500
102
35
71
178
37
97
195
486
104
35
69
173
38
95
189
474
106
34
68
170
39
92
185
462
108
33
67
167
40
90
180
450
110
33
65
164
41
88
176
439
112
32
64
161
42
86
172
429
116
31
62
155
43
84
167
419
120
30
60
150
44
82
164
409
124
29
58
145
45
80
160
400
129
28
56
140
46
78
157
391
133
27
54
135
47
76
153
383
138
26
52
130
48
75
150
375
144
25
50
125
49
73
147
367
150
24
48
120
50
72
144
360
157
23
46
115
51
71
141
355
164
22
44
110
52
69
138
346
171
21
42
105
53
68
136
340
180
20
40
100
54
67
133
333