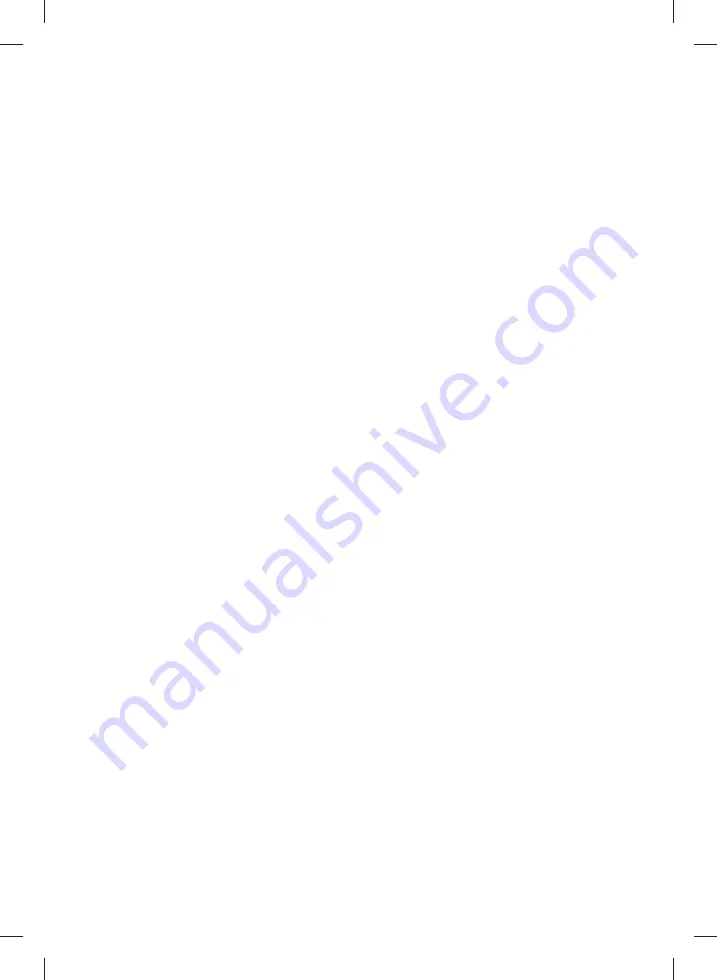
7. REMOVAL OF USED TWIN
BLADES
1. Unplug the saw and allow blades to cool.
2. Rotate the blades while pressing the
spindle lock down until the blades cannot
move. Remove the locking bolt and blades
can now be removed.
Then unscrew Lock Nutby rotation in coun-
ter clockwise and remove (see Fig.5-6).
3. Open the lower guard (see Fig. 2)
4. Lift up and remove Blade”B”
5. Remove the arbor adaptor (see Fig. 1)
6. Lift up and remove Blade “A” (see Fig. 1)
Disconnect the plug from the power source
before making any assembly, adjustments or
changing accessories. Such preventive safety
measures reduce the risk of starting the tool
accidentally. Do not use blades with
incorrect sized holes. Do not use defective or
incorrect blade washers or bolts. Avoid cutting
nails.
8. MOUNTING OF REPLACE-
MENT BLADES
Refer to section ACCESSORIES for the proper
replacement blades thatare needed for this
saw.
1. Unplug the saw.
2. Lay the saw down with the blade arbor
pointing upward.
3. Open the lower guard(Fig.2)
4. Place blade “A” onto the flange with the “A”
clearly visible (see Fig. I)
5. Align the holes on the blade with the pins
on the flange and securely fit the blade on
the flange (see Fig. 2).
6. Take the arbor adaptor ”I”and push it down
onto the flange with the”I“ clearly visible.
Make sure that the adaptor is properly
seated over the flat sides of the flange. (see
Fig.3)
7. Place the blade “B”onto the adaptor with
the “B” easily visible, then thread the lock
nut onto shaft. Do not tighten,(see Fig. 4).
8. Turn the blades so that the spindle lock can
be pressed down
9. Press down the spindle lock (see Fig.5)
10. Tighten the lock nut clockwise and then
release the press from the spindle lock (see
Fig.6). This will allow the blades to turn
freely.
11. Carefully turn blades with your hand to be
sure they easily turn in opposite directions.
9. DUAL BLADES
PLEASE NOTE
These products are fitted with specially
designed blades for “universal” use. These
blades spin in opposite direction. Never use
conventional carbide blades in this product.
Always bear in mind that it is the blades do-
ing the job, which means that the machine’s
capacity is not increased by overloading.(See
also in the instructions)
This is a very special machine and it can cope
with a surprising amount of tasks, but use it
with great care until you have learnt how to
handle it.
LUBRICATING INSTRUCTIONS
For cutting aluminum, copper or stainless
steel, the lubricating device must always be
used.
1. Before installing or replacing a lubricat-
ing stick, remove the power plug from the
source.
2. Insert the lubricating stick into the hole of
the lubricating device.
3. Turn the plastic knob of the lubricating
device clockwise to secure the stick.
The lubricating stick is fed by turning the
feeder wheel dock wise.
10.ACCESSORIES
LUBRICATINGSYSTEM
Lubricating System consists of two parts:
• Feeder wheel assembly
• Lubricating stick
AUXILIARY HANDLE
This fits into gearbox assembly and can be
fitted in one of the tapped (threaded) holes for
convenience.
This dual blade saw uses specifically designed
blades and no other types of blades should
ever be used. Other blades will not operate
safely in this saw and could resullt in serious
personal injury. Blades are marked ‘A’
inner blade and ‘B’ outer blade.
Do not touch the gearbox. It gets hot when in
operation.
Summary of Contents for DBS900
Page 10: ......