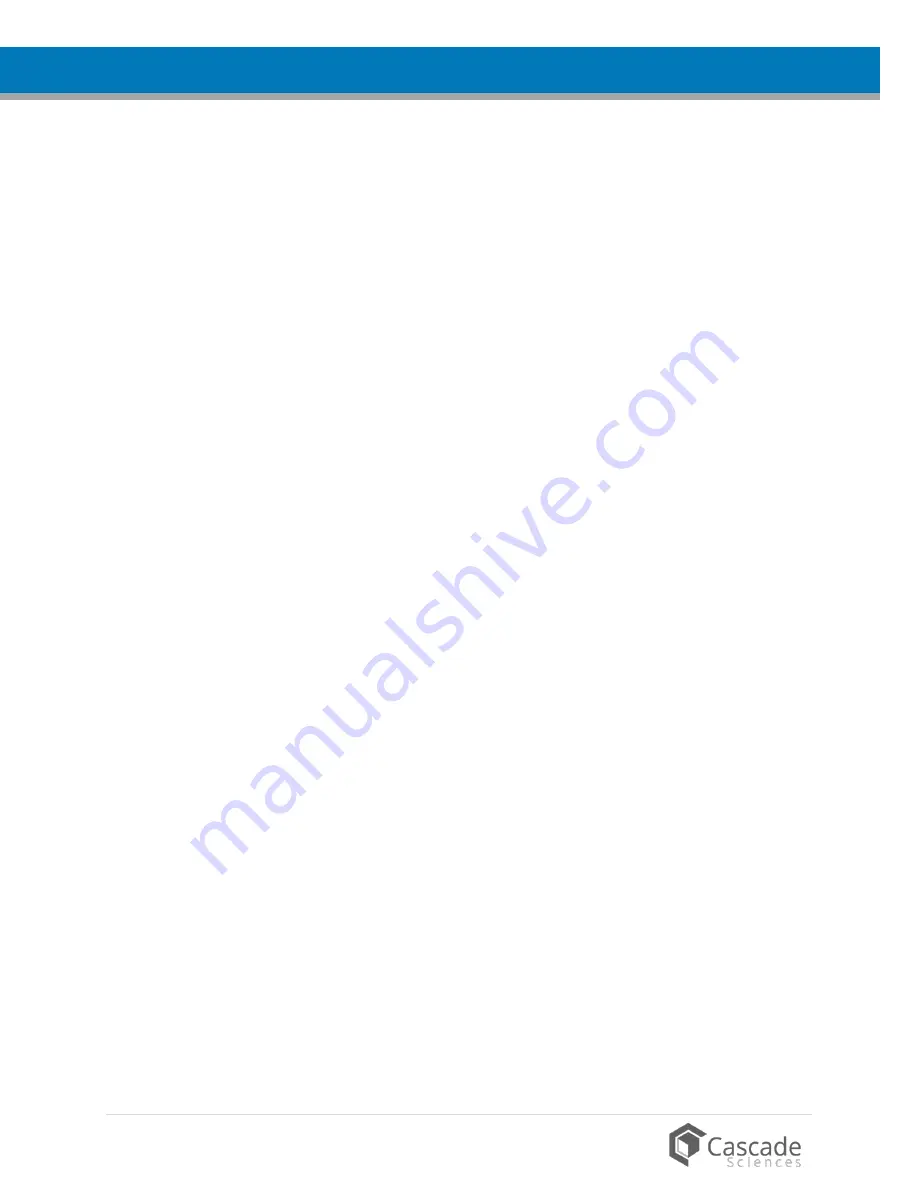
84 |
P a g e
cascadesciences.com
|
Tel. 503 847-9047
OPERATION
T
HEORY OF
O
PERATION
Purge and Pressurize Process
The built-in purge and pressurize system is engineered to prevent potentially explosive atmospheres from
coming into contact with the oven’s high-voltage electronic components when they are powered. This
prevents the components — including the heating elements — from serving as explosion-ignition sources.
The controller, power, and other major systems components are located in an enclosure at the top of the
oven. The heating elements are positioned in an internal enclosure wrapped around the oven chamber
exterior on the side walls, the ceiling, and the floor. The two enclosures are connected for purge gas flow
and over-pressurization. Both are isolated from the oven chamber atmosphere and the contents of the
internal vacuum plumbing.
The purge and pressurize process is automatic, fully automated, and must complete before the oven can
be turned on. The purge is controlled by a timer. The timer only starts the purge when two conditions are
both met. When power is provided to the oven (when it is plugged into a wall socket or the hardwire
connection to the oven is energized)
and
when the purge gas is flowing through both enclosures. The
timer automatically resets if the gas flow is interrupted or stops during the purge.
Prior to and while the oven is purging, only two types of electronic components are powered in the
enclosures. Encapsulated components isolated from the enclosure atmosphere. Intrinsically safe
components and circuits are designed to lack the spark potential and heat needed to ignite the hazardous
atmosphere types the oven is engineered and certified to work with.
Purge gas flowing at the rate specified in this user manual purges the enclosure volumes five times within
15 minutes. While maintaining an overpressure slightly higher than the ambient atmosphere, the purge
gas first diffuses through the electronics enclosure, then down a pipe into and through the elements
enclosure, and then exits through the Purge System Exhaust vent on the back of the oven. When the
purge completes, the gas flow maintains the overpressure and the oven enters a standby mode. An
internal gas pressure regulator and an enclosure pressure-relief valve help safeguard against damaging
levels of overpressure throughout the purge and after.
Once in standby mode, the oven can be fully powered (turned on) by an operator. When turned on, the
oven seals the over-pressurized enclosures by internally closing the purge gas line and the Purge System
Exhaust vent internal solenoids. However, the oven will automatically revert to standby mode,
depowering the elements and other high-voltage components, if the overpressure is lost. The oven gas-in
Vent port should remain connected to the pressurized gas supply flow while the oven is operating to help
guard against the loss of overpressure by backstopping the pressurized enclosures.
The oven has been tested to the IECEx 60079 standards governing purge and pressurization,
encapsulated components, and intrinsically safe components and circuits as protective concepts for
preventing the ignition of explosive gases.
These features do not make the oven explosion-proof
or guarantee it cannot ignite explosive concentrations of gas or vapor if operated incorrectly. Residual
risks are inherent in extracting or working with flammable materials and potentially ignitable
atmospheres.
Summary of Contents for CVO-5-EX Series
Page 1: ...Flammable Solvent Ovens Installation Operation Manual CVO 5 EX Oven Series...
Page 6: ...6 P a g e cascadesciences com Tel 503 847 9047 Special Conditions Of Use 131...
Page 7: ...7 P a g e cascadesciences com Tel 503 847 9047 TABLE OF CONTENTS...
Page 11: ...11 P a g e cascadesciences com Tel 503 847 9047 SAFETY CERTS AND STATEMENTS...
Page 17: ...17 P a g e cascadesciences com Tel 503 847 9047 SPECIFICATIONS...
Page 22: ...22 P a g e cascadesciences com Tel 503 847 9047...
Page 24: ...24 P a g e cascadesciences com Tel 503 847 9047 These groups include propane and n butane...
Page 29: ...29 P a g e cascadesciences com Tel 503 847 9047 Continued next page...
Page 37: ...37 P a g e cascadesciences com Tel 503 847 9047 INTRODUCTION...
Page 39: ...39 P a g e cascadesciences com Tel 503 847 9047...
Page 44: ...44 P a g e cascadesciences com Tel 503 847 9047 RECEIVING...
Page 51: ...51 P a g e cascadesciences com Tel 503 847 9047 Continued next page...
Page 54: ...54 P a g e cascadesciences com Tel 503 847 9047 Continued next page...
Page 61: ...61 P a g e cascadesciences com Tel 503 847 9047 End of Procedure...
Page 65: ...65 P a g e cascadesciences com Tel 503 847 9047 INSTALLATION...
Page 67: ...67 P a g e cascadesciences com Tel 503 847 9047 SYMBOLS...
Page 69: ...69 P a g e cascadesciences com Tel 503 847 9047 Continued next page...
Page 72: ...72 P a g e cascadesciences com Tel 503 847 9047 Continued next page...
Page 95: ...95 P a g e cascadesciences com Tel 503 847 9047 End of Procedure...
Page 104: ...104 P a g e cascadesciences com Tel 503 847 9047 End of Procedure...
Page 116: ...116 P a g e cascadesciences com Tel 503 847 9047 End of Procedure...
Page 123: ...123 P a g e cascadesciences com Tel 503 847 9047 Continued next page...
Page 125: ...125 P a g e cascadesciences com Tel 503 847 9047 Continued next page...
Page 127: ...127 P a g e cascadesciences com Tel 503 847 9047 End of Procedure...
Page 128: ...128 P a g e cascadesciences com Tel 503 847 9047 MAINTENANCE...
Page 130: ...130 P a g e cascadesciences com Tel 503 847 9047 REPLACEMENT PARTS...
Page 132: ......