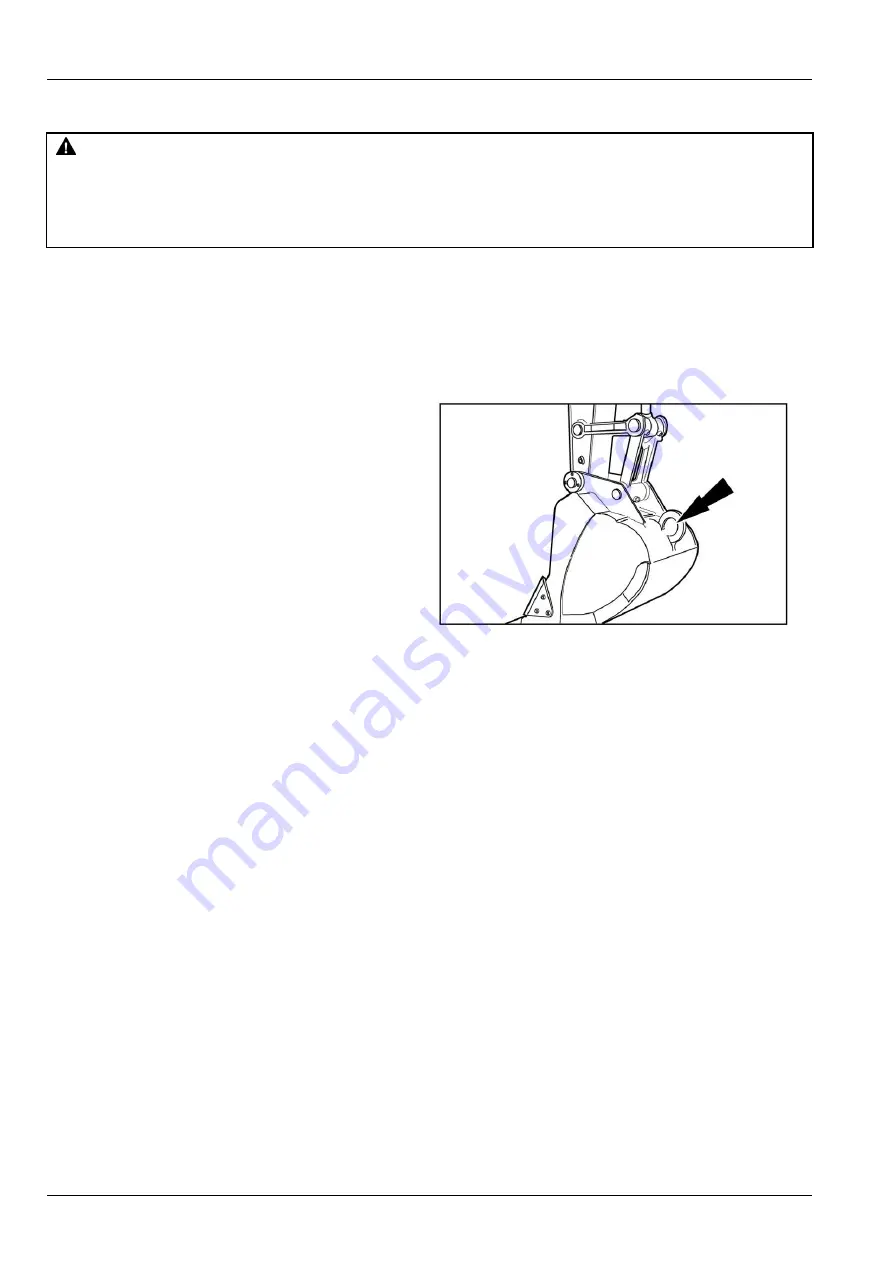
4 - OPERATING INSTRUCTIONS
Load handling
WARNING
Crushing hazard!
During load handling operations, it is very important to adhere strictly to the instructions given in this
manual and local legislation.
Failure to comply could result in death or serious injury.
W0257A
ATTENTION:
This machine is not a crane. Be very careful when you lift a load.
NOTICE:
The loads given are valid for the total working range height at the reach point indicated.
The load handling chart (located in the cab) shows the different permitted loads which can be lifted, depending on the
reach and the type of attachment on the machine.
The machine must be on a flat level, hard surface.
Only the load lift eye on the bucket may be used.
CT10D001A
1
If this machine is to be used to lift loads, for safety purposes, it is recommended that the machine is properly equipped.
Contact your CASE CONSTRUCTION dealer and install a Hose Burst Check Valve on your machine’s boom cylinders.
This system prevents the sudden lowering of the load in the event of a failure of a hydraulic hose, line, or fitting in the
boom hydraulic system. Such a failure can cause personal injury or death.
• Know and understand each signal from the signal person before you start.
• Always know the location of all persons in your work area before you start.
• Make certain there is no damage to the lifting device and rigging parts.
• Make certain the lifting device has the appropriate tensile strength for the load being lifted.
• Do not exceed either the radius or the height restrictions shown on the lift capacity charts posted in the cab.
• Be careful to balance the load correctly.
• Always move the load slowly. Do not move the load over the top of persons. Keep all persons away from the load.
• When the load is raised, keep all persons away until the load is placed on blocks or on the ground.
ATTENTION:
It is extremely dangerous if the load lifted begins to swing. The upper structure should be centered over
the load to help prevent dangerous swinging.
4-20
Summary of Contents for CX145C SR
Page 6: ......
Page 18: ...1 GENERAL INFORMATION 1 12 ...
Page 29: ...2 SAFETY INFORMATION E5054225_TU 4 2 11 ...
Page 132: ...3 CONTROLS INSTRUMENTS 3 82 ...
Page 160: ...4 OPERATING INSTRUCTIONS 4 Operate the arm control to unhook the tool KKZVLU 024A 14 4 28 ...
Page 180: ...4 OPERATING INSTRUCTIONS 4 48 ...
Page 206: ...6 MAINTENANCE Offset boom pin 10 07C803C9 17 6 16 ...
Page 207: ...6 MAINTENANCE Arm backhoe bucket 375EFD72 18 AB1F527A 19 6 17 ...
Page 298: ...8 SPECIFICATIONS Offset maximum left EACB5F36 6 See next page for the value 8 14 ...
Page 300: ...8 SPECIFICATIONS 8 16 ...