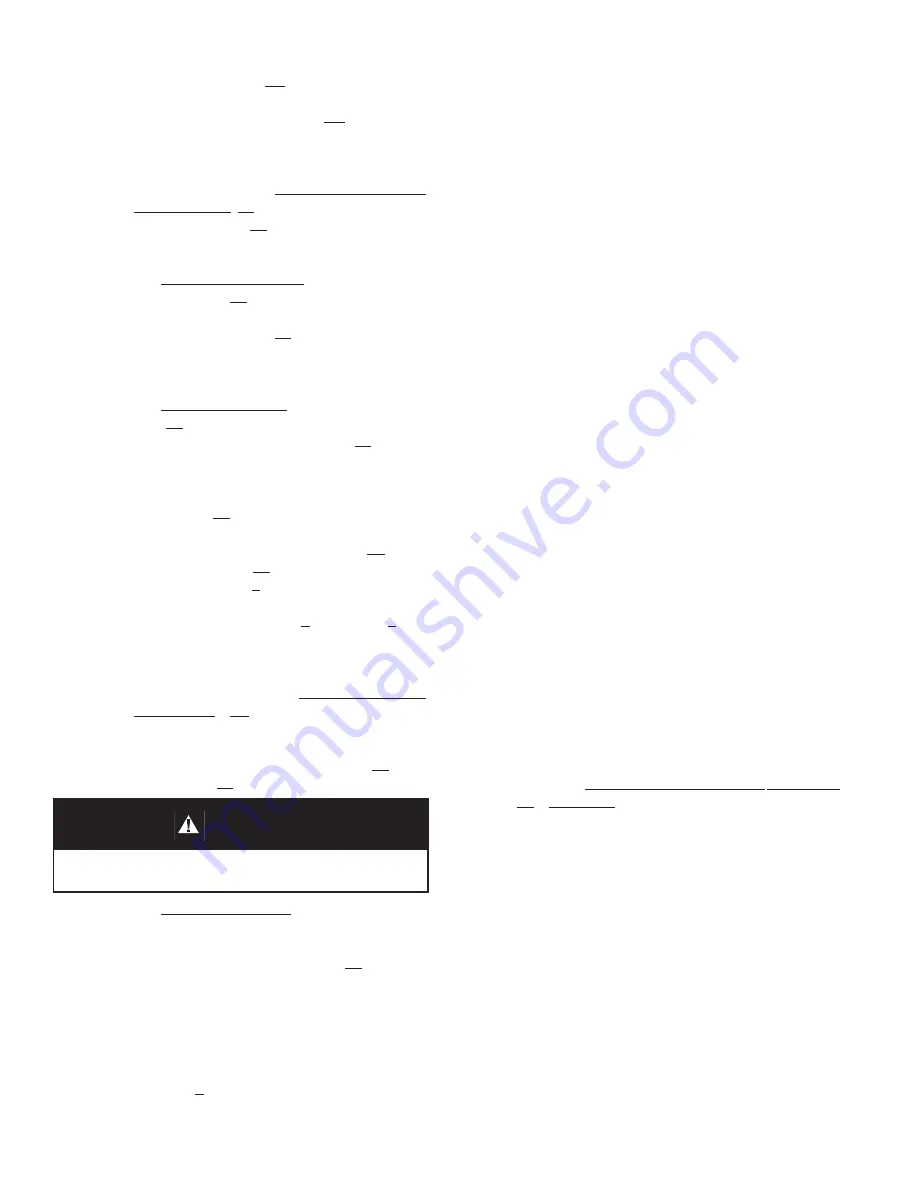
IOM-Ranger
6
1. Position valve on a
fl
at work sur face with the
actuator assembly (AA) oriented vertical.
NOTE:
If actuator assembly (AA) has been
re moved, rotate stem (7) to close plug (6), and
proceed with Steps 4 through 8.
2. If the valve actuator includes a handwheel/
adjusting screw (58) assembly, use handwheel/
ad just ing screw (58) to remove the closing
torque; i.e. “stem windup”.
a. For ATO-FC valves: Loosen locking
le ver/nut (59) with CCW rotation when
viewed from above and rotate handwheel/
ad just ing screw (58) CW just enough to
relieve the closing torque, but not enough
to start opening the plug (approximately
1/2-1 handwheel rev o lu tion).
b. For ATC-FO valves: Loosen locking le ver
(59) with CCW rotation when viewed from
above and turn handwheel (58) CW to
fully close the plug (6) and then back
off enough to relieve the closing torque
by reversing the handwheel/adjusting
screw (58) CCW (approximately 1/2-1
handwheel revolution).
c. Remove machine screws (36) and
cover plate (20). Through opening in
arm hous ing (4), insert a tool similar to a
screw driv er and apply force to either side
at the lower rod end (9). Rod end (9) will
move easily from side to side when all
clos ing torque has been relieved.
3. If the valve actuator does not include
handwheel (58) assembly, connect a
tem po rary air supply with an in-line ad just able
airset reg u la tor with gauge to the ac tu a tor top
works. Remove machine screws (36) and
cover plate (20).
a. For ATC-FO Valves: Pressurize ac tu a tor
to a level 2-3 psig (0.1-0.2 Barg) under the
upper pressure lev el of the bench setting
as stated on the name plate (21); i.e. 5-15
psig (.34–1.03 Barg) range, set pressure
at 12-13 psig (.83-.90 Barg). Refer to 2.c.
previous to con
fi
rm relief of all closing
torque. Ad just ac tu a tor pres sure slow ly
±1 to 2 psig (±.07–0.2 Barg) to con
fi
rm
great est/eas i est move ment of lower rod
end (9).
4. Remove the seal retainer screws (18) and
washers (23) and (47)
5. Remove the seal retainer (3) (full or i
fi
ce,
re duced, anti-cavitation, lo-noise), seal re tain er
gas ket (9), soft seal (10) (if supplied) and metal
seal (11).
6. Through backside of body (1), place a wood en
hammer handle on the vane on the back side
of the plug (6), or the LN2–LN4 lo-noise insert
(25), and tap lightly to remove cage as sem bly.
7. Remove bearings (4)( 5) from the cage (2).
(If necessary, pry or tap the bear ings loose.)
Rotate plug (6) 135° to 180° from the closed
position and lift plug (6) from the cage (2).
8. Remove abrasion sleeve (26) or LN2–LN4
lo-noise insert, if installed.
9. Depressurize actuator for ATC-FO valves.
C. Trim
Reassembly:
Inspect and clean all parts. If any parts are worn,
replace with new parts. If the stem assembly (7)
has been removed, reassemble per Section IV,
Sub sec tion F., then proceed to reassemble the trim.
For sizes 1" - 3", Reorient unit so that the back-end
of the body (1) is directed downwards, and the
front-end is up wards and in a horizontal plane. In
this position gravity will assist in proper alignment of
internals. For 4" - 8" sizes orient body on its side.
NOTES:
A. The seal retainer gasket (9) and soft
seal (10) should always be replaced after every
dis as sem bly. Use only original factory re place ment
parts.
B. For ATC-FO Valves without handwheel
(58) assembly: Pressurize ac tu a tor to levels
in di cat ed per previous Sub sec tion 3.a. to prop er ly
align groove in stem sub as sem bly (7) to mate with
the tongue on the plug (6).
1. Install LN2/4 “lo-noise” insert (25) or “abra sion
sleeve” insert (26) into the body (1) cavity before
inserting the cage/plug subassembly (2)(4)(5)
(6). Ensure that the insert (25)(26) is properly
located within the groove located in the back-
end of the body (1)
NOTE:
For proper orientation of LN2, LN3 or LN4
trims, see Figure 6.
WARNING
Do not insert hands/
fi
ngers into body (1) or actuator
arm housing (4) openings while actuator is pressurized.