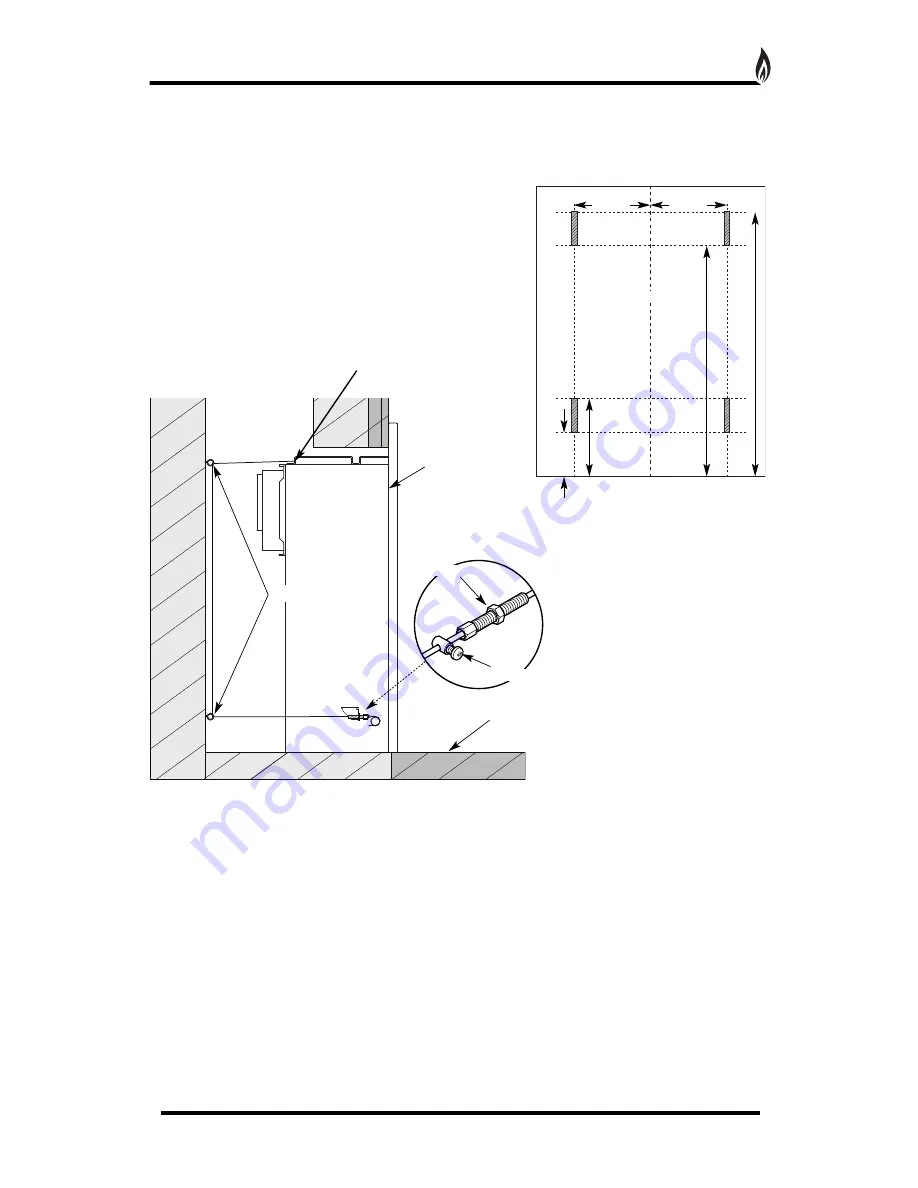
10
ALTERNATIVE FIXING METHOD
Where the drilling of the back panel is not practical, an alternative
fixing method may be employed using the optional cable fixing
kit provided. Drill four holes in the rear of the fireplace opening.
Securely fix the four eye bolts provided using suitable Rawl
plugs. Feed one cable through each of the eyes in the rear of
the fire box.
Fix the box into the opening, securing into position using the
cable fixing kit. Do not cut off the loose ends as the full length
is required should the box need refitting at any time. Coil up
and securely store underneath the burner tray.
INSTALLATION PROCEDURE FOR STANDARD 22” X 16” OPENING
CONTINUED
Radiant box
Hearth
Eye Bolts
Tension Nut
Cable Clamping Screw
Fig. 7
Insert cables through two small
holes in vertical edge of top plate.
119mm
Centre Line
567mm
max
Fig. 8
Drill holes for 4 eye bolts between
max and min heights.