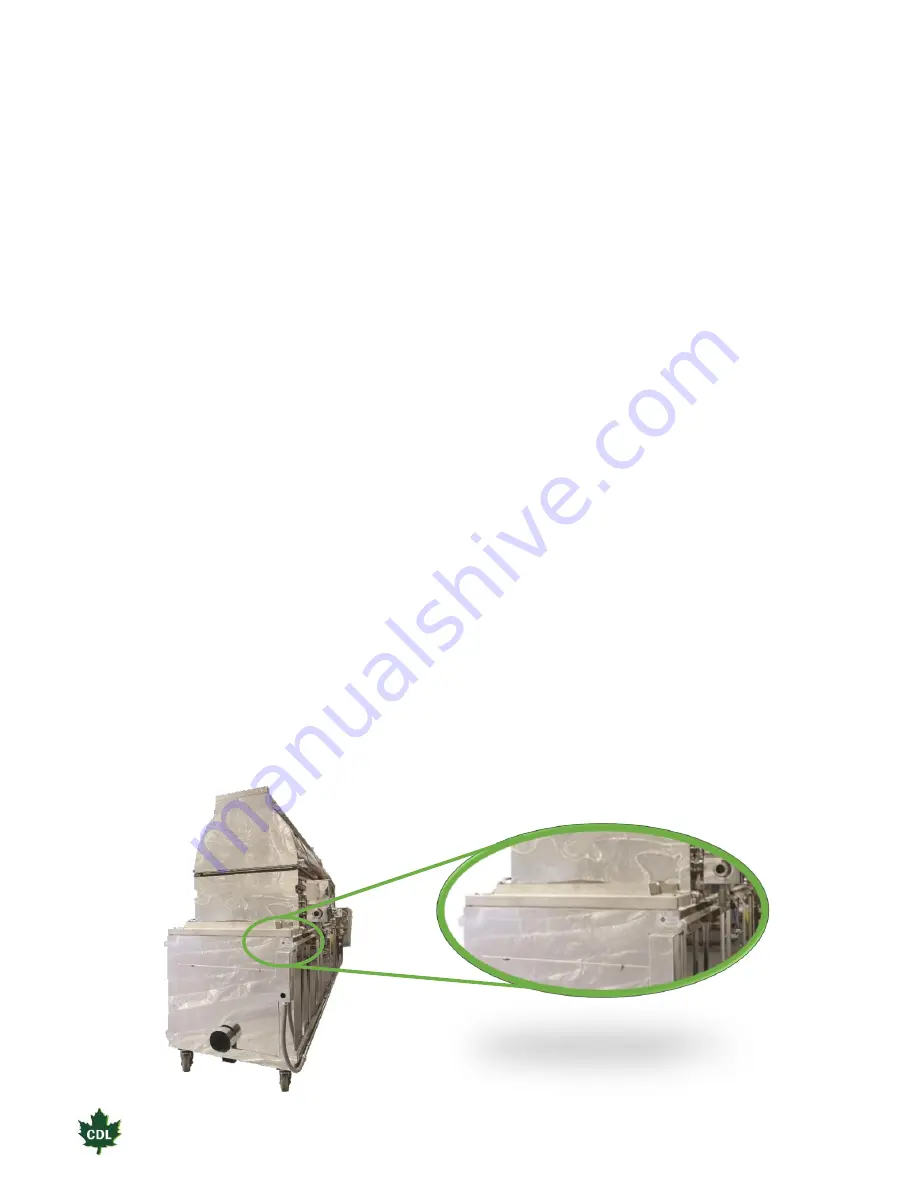
2
CDL Maple Sugaring Equipment Inc.
Thank you for purchasing the
INTENS-O-FIRE 2.0
wood-fired evaporator from CDL. This
guide will help you install your product and make the most of it. It has all the
information you need.
INFORMATION
Write down these details for future reference
Size: ________________________________________________
Purchase date and invoice number: ______________________________
Serial number: _________________________________
Representative: _______________________________________________
Serial number location
The serial number can be found on the back of the evaporator.