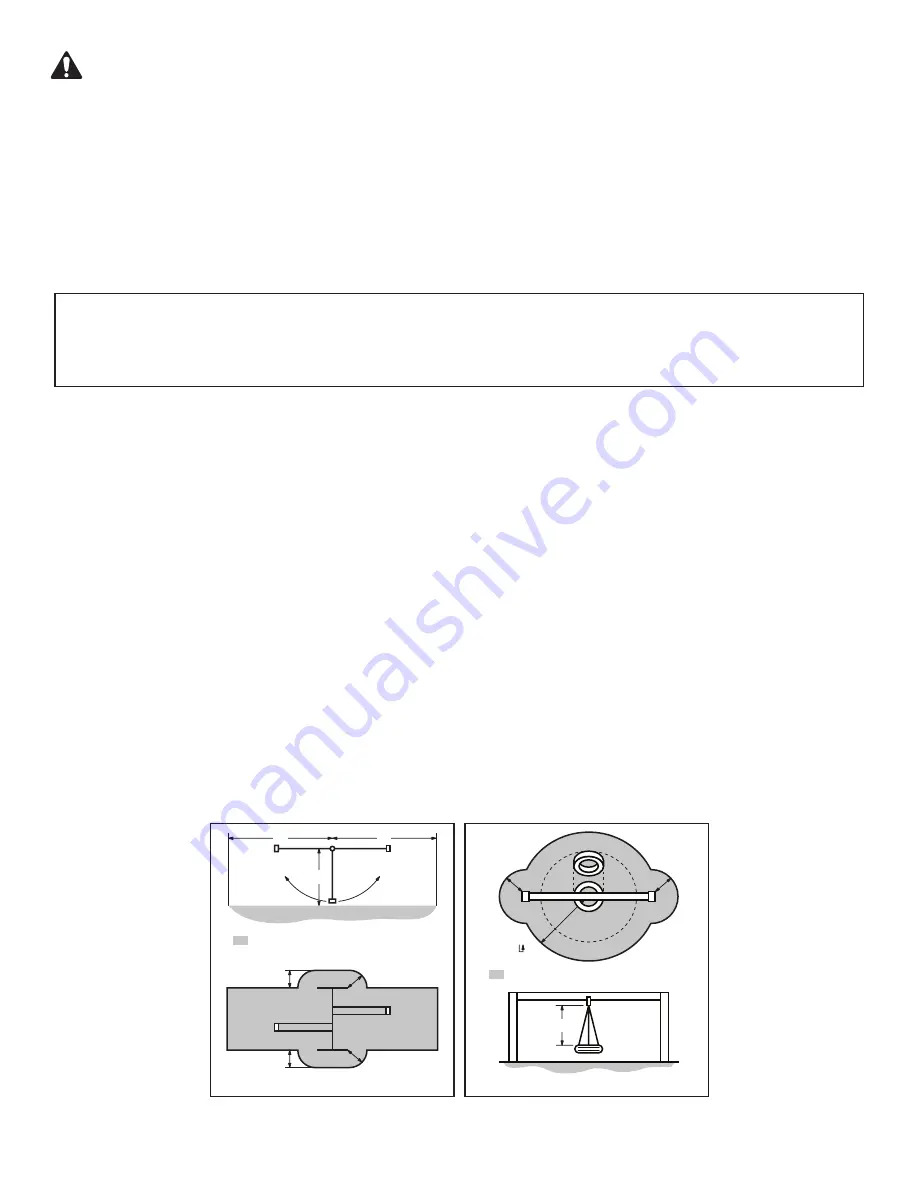
One of the most important things you can do to reduce the likelihood of serious head injuries is to install shock-absorbing
protective surfacing under and around your play equipment. The protective surfacing should be applied to a depth that is suitable
for the equipment height in accordance with ASTM F1292. There are different types of surfacing to choose from; whichever
product you select, follow these guidelines:
Loose-Fill Materials
• Maintain a minimum depth of 9 inches of loose-fill materials such as wood mulch/chips, engineered wood fiber (EWF), or
shredded/recycled rubber mulch for equipment up to 8 feet high; and 9 inches of sand or pea gravel for equipment up to 5 feet
high. NOTE: An initial fill level of 12 inches will compress to about a 9-inch depth of surfacing over time. The surfacing will also
compact, displace, and settle, and should be periodically raked and refilled to maintain at least a 9-inch depth.
• Use a minimum of 6 inches of protective surfacing for play equipment less than 4 feet in height. If maintained properly, this
should be adequate. (At depths less than 6 inches, the protective material is too easily displaced or compacted.)
NOTE: Do not install home playground equipment over concrete, asphalt, or any other hard surface. A fall onto a hard surface
can result in serious injury to the equipment user. Grass and dirt are not considered protective surfacing because wear and
environmental factors can reduce their shock absorbing effectiveness. Carpeting and thin mats are not adequate protective
surfacing. Ground level equipment -- such as a sandbox, activity wall, playhouse or other equipment that has no elevated play
surface -- does not need any protective surfacing.
• Use containment, such as digging out around the perimeter and/or lining the perimeter with landscape edging. Don’t forget to
account for water drainage.
• Periodically rake, check and maintain the depth of the loose-fill surfacing material. Marking the correct depth on the play
equipment support posts will help you to see when the material has settled and needs to be raked and or replenished. Be sure to
rake and evenly redistribute the surfacing in heavily used areas.
• Do not install loose fill surfacing over hard surfaces such as concrete or asphalt.
Poured-In-Place Surfaces or Pre-Manufactured Rubber Tiles
You may be interested in using surfacing other than loose-fill materials - like rubber tiles or poured-in-place surfaces.
• Installations of these surfaces generally require a professional and are not “do-it yourself” projects.
• Review surface specifications before purchasing this type of surfacing. Ask the installer/manufacturer for a report showing that
the product has been tested to the following safety standard: ASTM F1292
Standard Specification for Impact Attenuation of
Surfacing Materials within the Use Zone of Playground Equipment
. This report should show the specific height for which the
surface is intended to protect against serious head injury. This height should be equal to or greater than the fall height - vertical
distance between a designated play surface (
elevated surface for standing, sitting, or climbing
) and the protective surfacing
below - of your play equipment.
• Check the protective surfacing frequently for wear.
Placement
Proper placement and maintenance of protective surfacing is essential. Refer to diagram on front cover. Be sure to;
• Extend surfacing at least 6 feet from the equipment in all directions.
• For to-fro swings, extend protective surfacing in front of and behind the swing to a distance equal to twice the height of the top
bar from which the swing is suspended.
• For tire swings, extend surfacing in a circle whose radius is equal to the height of the suspending chain or rope, plus 6 feet in all directions.
From the CPSC Outdoor Home Playground Safety Handbook. At www.cpsc.gov/CPSCPUB/PUBS/324.pdf
Protective Surfacing - Reducing Risk of Serious Head Injury From Falls.
3
2H
2H
H
Denotes Use Zone with Protective Surfacing
Use Zone for Single-Axis Swings
6 ft.
6 ft.
6 ft.
6 ft.
Denotes Use Zone with Protective Surfacing
Use Zone for Multi-Axis Swings
6 ft.
6 ft.
6 ft.
L
3
support@cedarsummitplay.com