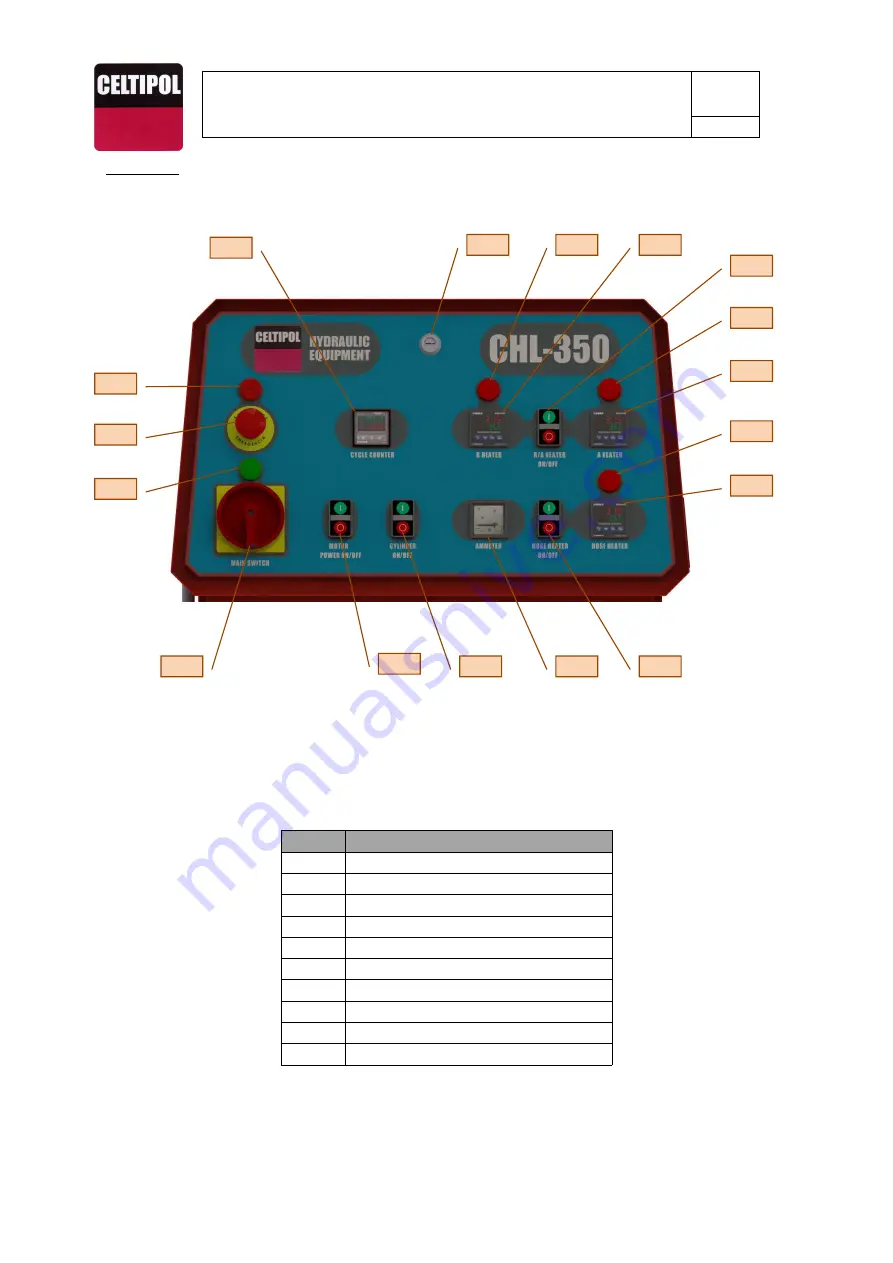
10
CHL-350 TECHNICAL MANUAL
03-2021
Translation of the original manual
CONTROL
REF.
DESCRIPTION
7052
Temperature controller ESM4420
7053
Start/stop button
7054
Ammeter
7055
Main switch
7056
Emergency stop
7057
Red signal light
7058
Green signal light
7059
Electric cabinet lock
7074
Cycle counter TCT201
7168
RESET button with red signal light
7057
7057
7059
7052
7057
7052
7053
7053
7054
7053
7053
7055
7058
7056
7168
7074
7052
Summary of Contents for CHL-350
Page 33: ...33 CHL 350 TECHNICAL MANUAL 03 2021 Translation of the original manual 14 ELECTRICAL DIAGRAMS ...
Page 34: ...34 CHL 350 TECHNICAL MANUAL 03 2021 Translation of the original manual ...
Page 35: ...35 CHL 350 TECHNICAL MANUAL 03 2021 Translation of the original manual ...
Page 36: ...36 CHL 350 TECHNICAL MANUAL 03 2021 Translation of the original manual ...
Page 37: ...37 CHL 350 TECHNICAL MANUAL 03 2021 Translation of the original manual ...
Page 60: ...60 CHL 350 TECHNICAL MANUAL 03 2021 Translation of the original manual 28 CE DECLARATION ...
Page 61: ...61 CHL 350 TECHNICAL MANUAL 03 2021 Translation of the original manual ...