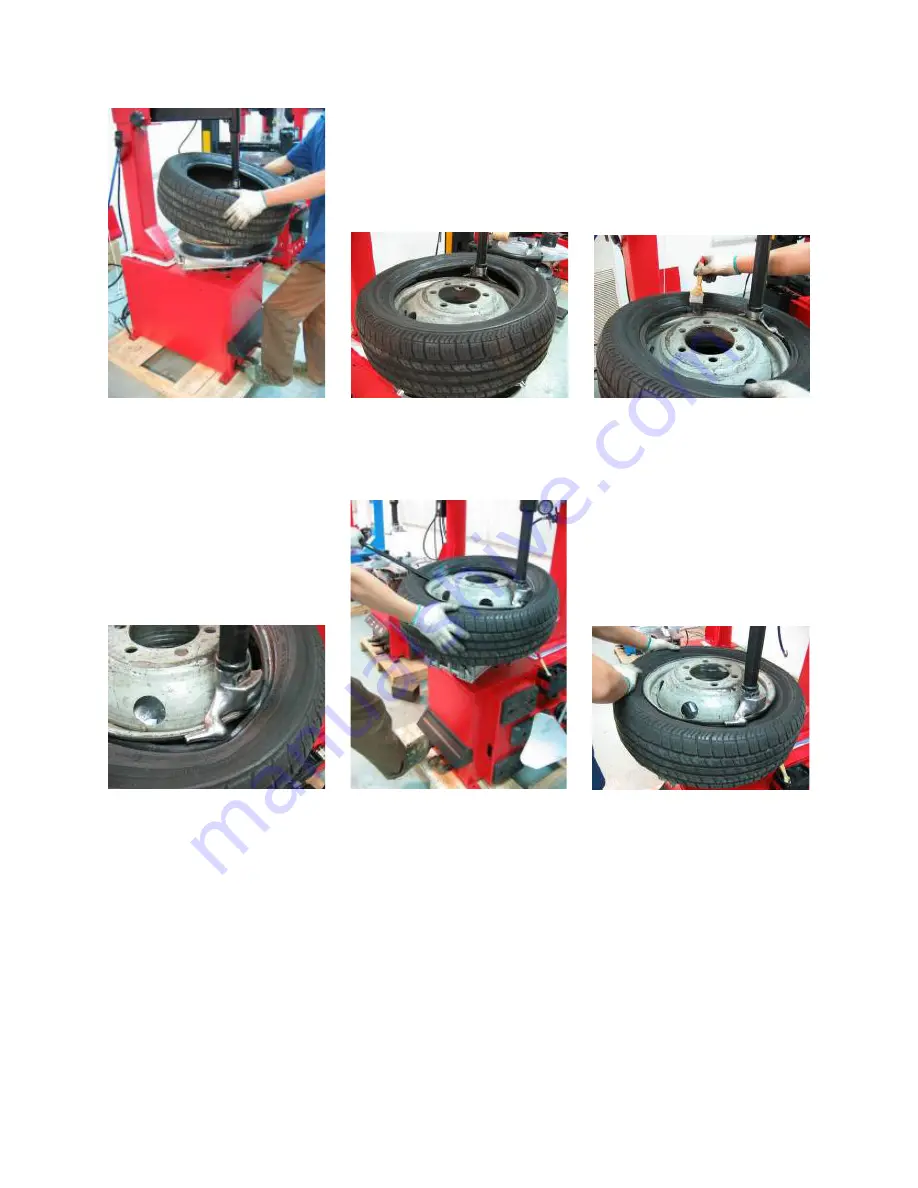
Page 27
SKU 45656
For technical questions, please call 1-800-444-3353.
7. Rotate the turntable in a clockwise
direction by fully depressing the
reverse pedal.
8. Continue until the nether bead of
the tire is completely onto the wheel
rim.
9. Insert the inner tube (if there is
one). And spread tire grease (or
a similar lubricant) liberally on the
complete circumference of the tire
bead.
10. Move the tire so that the bead
passes below the front section of
the mounting head and is brought up
against the edge of the rear section
of the mounting head.
11. Keep the tire bead pressed
down into the wheel rim channel
with your hands (or the lever). Then,
depress the reverse pedal to rotate
the turntable clockwise.
12. Continue this process throughout
the entire circumference of the wheel
and tire.