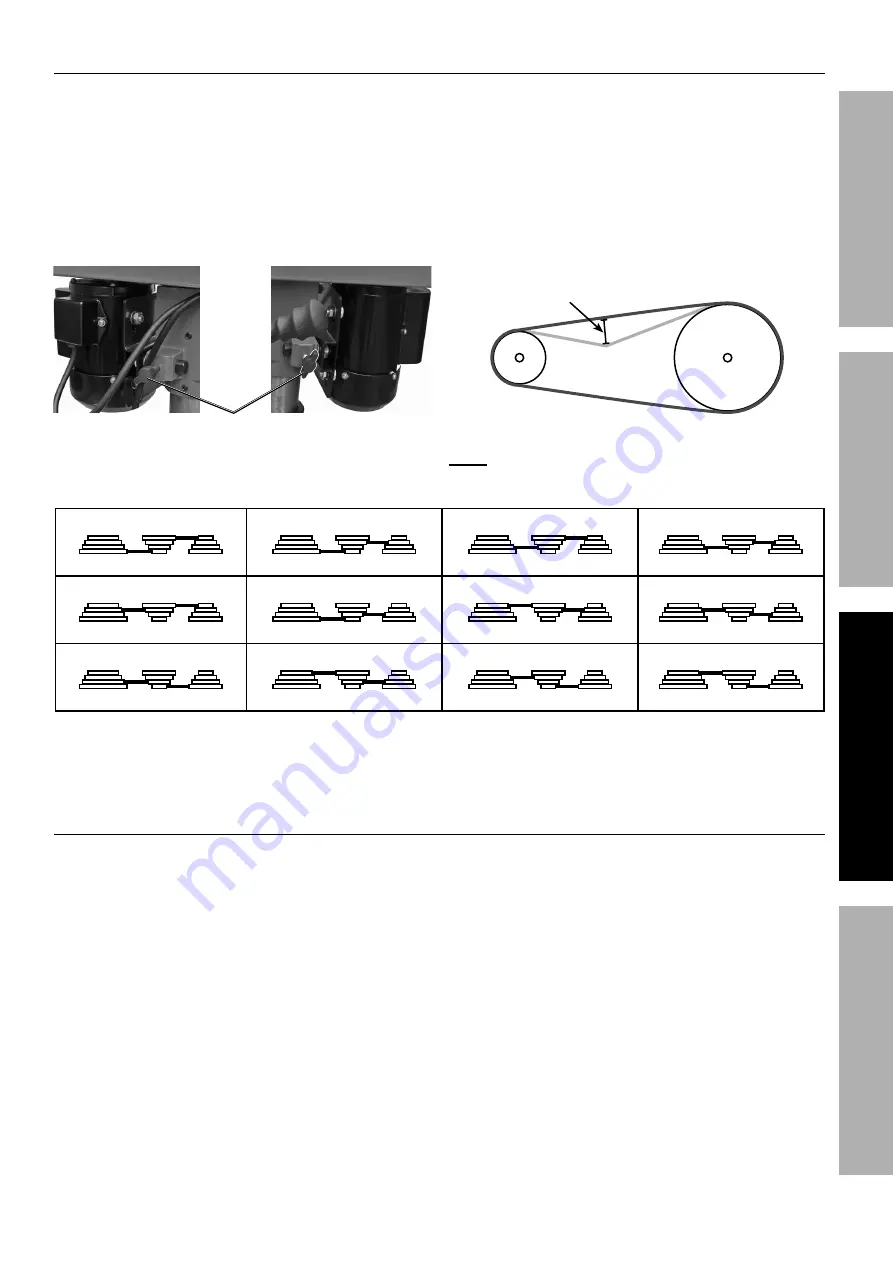
Page 9
For technical questions, please call 1-888-866-5797.
Item 63471
S
AFET
y
Op
ERA
TION
M
AINTENAN
c
E
SETU
p
changing Drill Speed
Before changing the speeds, make sure the
machine is switched OFF and UNPLUGGED.
1. Open the pulley cover.
2. Loosen the Motor Tension Knob (70) on
each side of the Headstock (67), and move
the Motor (77) towards the Headstock to
relieve tension on the Belts (43, 80).
Motor Tension
Knobs (70)
(front view)
(rear view)
Figure I: Motor Tension Knob locations
3. Consult the chart below and position the
Belts (43, 80) on the Pulleys (42, 46, 78)
according to the desired drill speed.
4. When the Belts have been correctly positioned,
tighten them by pushing the Motor away
from the Headstock until the belt deflects by
approximately 1/2″ at its center when using
reasonable thumb pressure. Lock this position
in with the two Motor Tension Knobs (70).
Deflection
Distance
Figure J: Belt Deflection
Note:
If either belt is too long to be properly
tensioned, it must be replaced.
300 RpM
Spindle Motor
370 RpM
Spindle Motor
470 RpM
Spindle Motor
570 RpM
Spindle Motor
630 RpM
Spindle Motor
690 RpM
Spindle Motor
950 RpM
Spindle Motor
1400 RpM
Spindle Motor
1620 RpM
Spindle Motor
1760 RpM
Spindle Motor
2550 RpM
Spindle Motor
2900 RpM
Spindle Motor
Figure K: Drill Speed Table
The table above shows the belt arrangements for given drill speeds.
A full chart is also located on the inside of the pulley cover.
Drill Bit Installation
1. Insert the drill bit into the jaws of the Chuck
approximately 1″, ensuring that the jaws
do not touch the flutes of the drill bit.
2. Before tightening the Chuck, ensure that
the drill bit is centered within the jaws.
3. Tighten the Chuck securely with
the included Chuck Key.