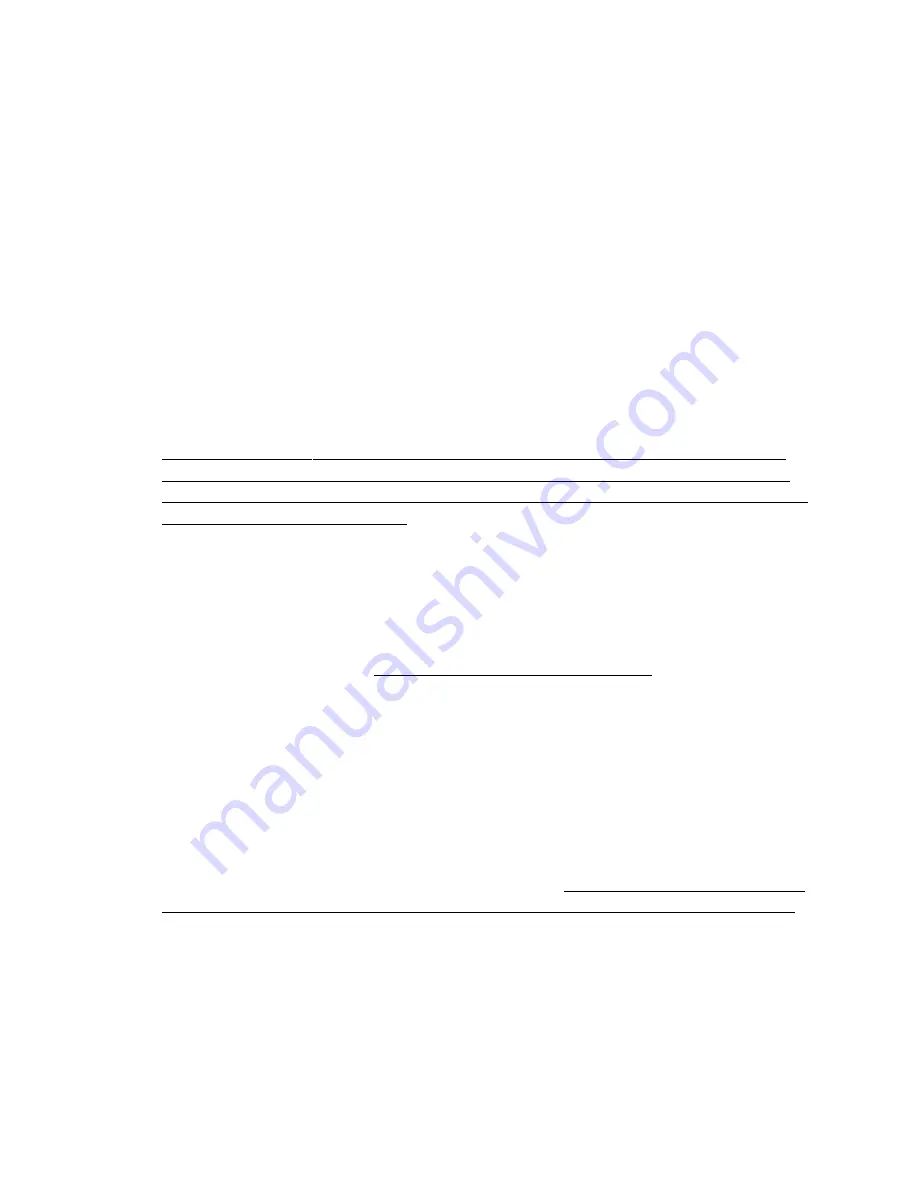
15.
In the event fast decompression of the Air Tanks (part #39) is required, immedi-
ately turn off the Gasoline Engine (part #25) and pull out on the
Pull Ring
of the
Safety Valve (part #29) until both Air Tanks have fully decompressed.
(See Figures B, and E.)
16.
Pull out on the Safety Valve (part #29) to immediately release air pressure in the
Air Tanks (part #39).
(See Figure I.)
SKU 04169
PAGE 10
REV 09/03
17.
When finished using the Air Compressor, turn off the Gasoline Engine
(part #25), and pull out on the Pull Ring of the Safety Valve (part #29) until both
Air Tanks (part #39) have fully decompressed.
(See Figures B, and E.)
INSPECTION, MAINTENANCE, AND CLEANING
1.
CAUTION!
Aways
release all pressure from the system and disconnect all
tools
from the Air Compressor before performing any inspection, maintenance,
or cleaning. Be aware that the sudden release of air from any valve or air tool can
present a danger to one’s ears.
2.
BEFORE EACH USE,
inspect the general condition of the Air Compressor.
Check all air fittings for leaks. Check for loose screws, misalignment or binding
of moving parts, cracked or broken parts, damaged, and any other condition that
may affect the safe operation of this tool. If abnormal noise or vibration occurs,
immediately release all pressure from the system and have the problem cor-
rected before further use.
Do not use damaged equipment.
The Drain Plugs are located underneath each Air Tank, and should be used daily
to release all trapped moisture that may cause Air Tank corrosion. Slowly and
carefully unscrew
(no more than four threads)
the Drain Plugs until the con-
densation begins to be released from the Air Tanks. Allow sufficient time for all of
the condensation to escape from the Air Tanks. Then, firmly re-tighten the Drain
Plugs.
(See Figure E.)
3.
DAILY: EMPTY CONDENSATION FROM THE AIR TANKS (part #39).
4.
DAILY:
Check the Air Compressor oil level. If necessary, fill with a premium
quality, 30-weight, non-detergent, compressor oil.
NOTE:
When checking the Air
Compressor oil level, make sure to
unscrew
(do not pull) the Oil Cap (part #23).
5.
EVERY 100 HOURS OF USE:
Clean the Air Filter Sleeve (part #1) with a mild
solvent. Then, dry and re-attach the Air Filter Sleeve. (Replace the Air Filter
Sleeve if it is too dirty to properly clean.) To clean or replace the Air Filter Sleeve,
remove the two Hex Socket Set Bolts. Remove the Air Filter Cover. Remove the
Air Filter Sleeve and clean. Then, replace the Air Filter Sleeve and two Hex
Socket Set Bolts.
(See Figures E, and F.)