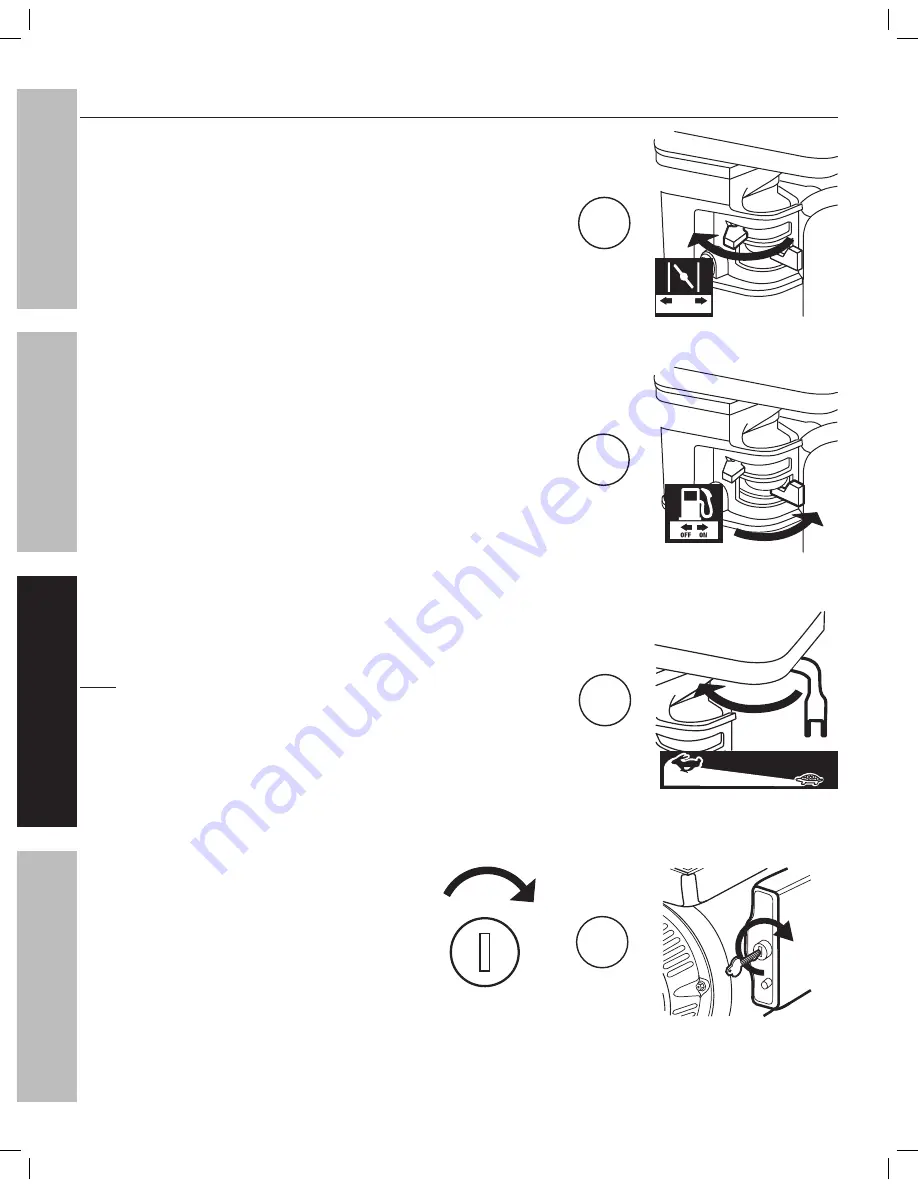
Page 12
For technical questions, please call 1-800-520-0882.
Engine for Item 56101
Electric Start (if equipped)
1. To start a cold engine, move the Choke to the
CHOKE position.
To restart a warm engine, leave the Choke in the
RUN position.
2. Open the Fuel Valve.
3. Slide the Throttle or Speed Control Lever to 1/3
away from the SLOW position (the “turtle”).
Note:
Some tools have a Speed Control Lever located
elsewhere on the tool which functions the same as
the Throttle. Use the Speed Control Lever in place
of the Throttle when the tool is so equipped.
4. Turn the Engine Switch to START.
CHOKE RUN
1
2
3
ON
OFF
START
4
START
SAFETY
OPERA
TION
MAINTENANCE
SETUP