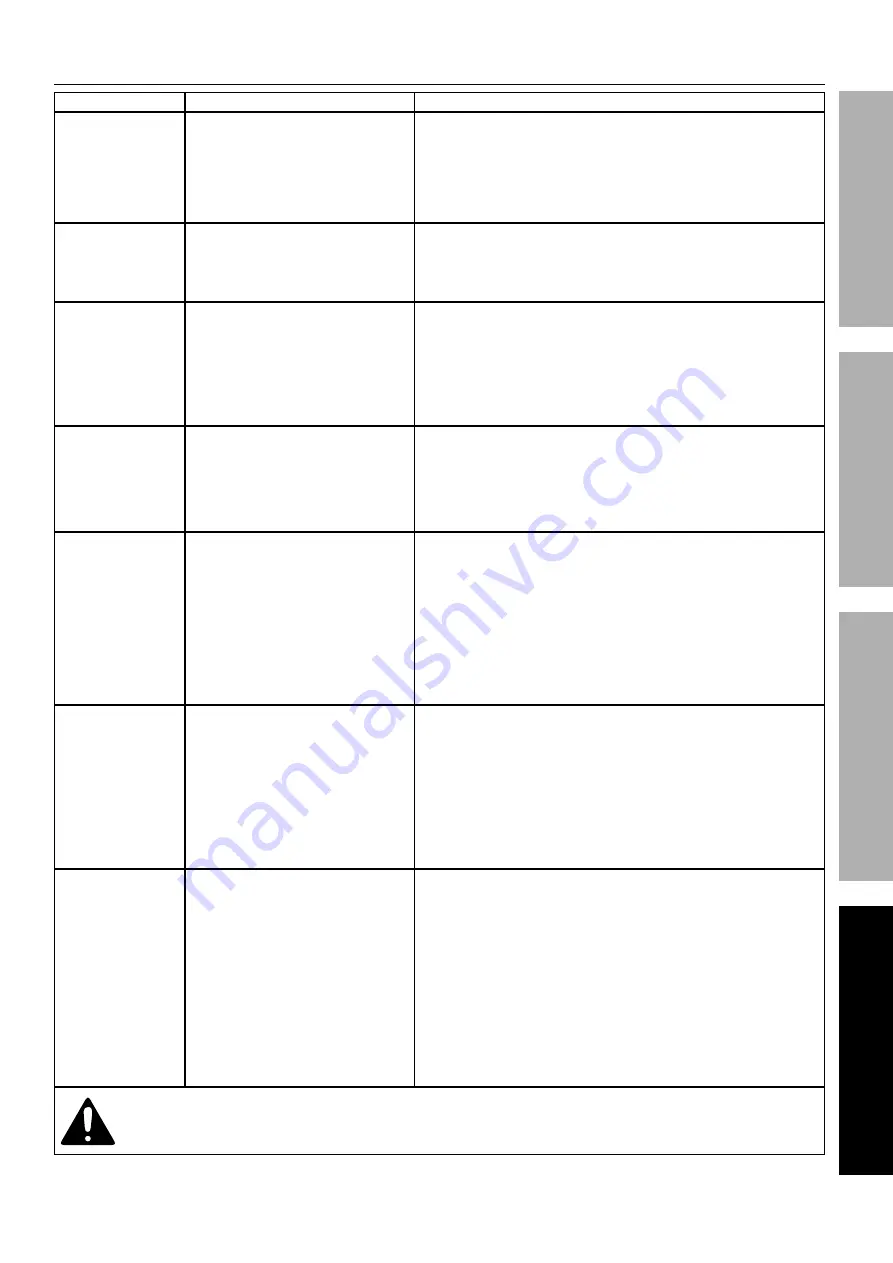
Page 17
For technical questions, please call 1-888-866-5797.
Item 62913
SAFETY
Op
ERA
TION
M
AINTENANCE
INST
ALLA
TION
Troubleshooting
problem
possible Causes
Likely Solutions
Engine will
not start
(Note: See engine
manual for engine
specific issues.)
COMPRESSOR SPECIFIC:
1. Pilot Valve closed.
2. Tank already pressurized.
COMPRESSOR SPECIFIC:
1. Open pilot valve before start procedure,
close after unit is running.
2. Turn engine on. Compressor will turn on as
needed when pressure reaches preset level.
Compressor
overheats
1. Incorrect lubrication or
not enough lubrication.
2. Worn parts.
1. Lubricate using recommended oil or
grease according to directions.
2. Have qualified technician inspect internal
mechanism and replace parts as needed.
Severe air
leakage
1. Poor air outlet seal.
2. Loose cylinder/cylinder head.
3. Damaged valve or housing.
4. Dirty, worn or damaged valve.
1. Tighten or re-attach using thread seal tape.
2. Tighten cylinder/cylinder head assembly.
If cylinder/cylinder head cannot tighten properly,
internal parts may be misaligned.
3. Replace damaged components.
4. Clean or replace valve assembly.
Unit stalls
1. Low engine idle.
2. Severely clogged air filter.
3. Improper lubrication.
4. Defective pilot/unloader valve.
1. Qualified technician should increase idle to
2,000±100 RPM by adjusting pressure switch.
2. Replace air filter.
3. Check for proper oil level.
4. Replace pilot valve.
Excessive noise
1. Loose drive pulley or flywheel.
2. Misaligned pulleys.
3. Lack of oil in crankcase.
4. Worn connecting rod.
5. Worn wrist pin bushing.
6. Worn bearings.
7. Loose belts.
1. Loose pulleys are a common cause of
“knocking”. Tighten appropriate bolts.
2. Align pulleys with straightedge and secure in place.
3. Check for proper oil level.
4. Replace connecting rod.
5. Remove piston assembly and replace necessary parts.
6. Replace bearings and oil.
7. Check for proper belt tension.
Oil in the
discharge air
1. Wrong type of oil or low-
quality oil.
2. Overheating.
3. Restricted intake air.
4. Worn piston rings.
5. Excessive moisture
in the tank.
1. Change oil. Check oil recommendations
under EQUIPMENT SET UP, Equipment
Oil Fill section of this manual.
2. See above Excessive Noise section.
3. Clean or replace air filter.
4. Replace piston rings.
5. Drain moisture from the tank daily.
Low discharge
pressure
1. Air leaks.
2. Leaking valves.
3. Restricted air intake.
4. Blown gaskets.
5. Slipping belts.
1. Listen for escaping air. Apply soap solution
to all fittings and connections. Bubbles will
appear at points of leakage. Tighten or
replace leaking fittings or connections.
2. Remove head and inspect for valve breakage,
weak valves, scored valve plate, etc. Replace
defective parts and reassemble. Replace head
gasket each time the head is removed.
3. Clean or replace air filter element.
4. Replace and gaskets proven faulty on inspection.
5. Tighten Belts (See monthly maintenance.)
Follow all safety precautions whenever diagnosing or servicing the equipment or engine.