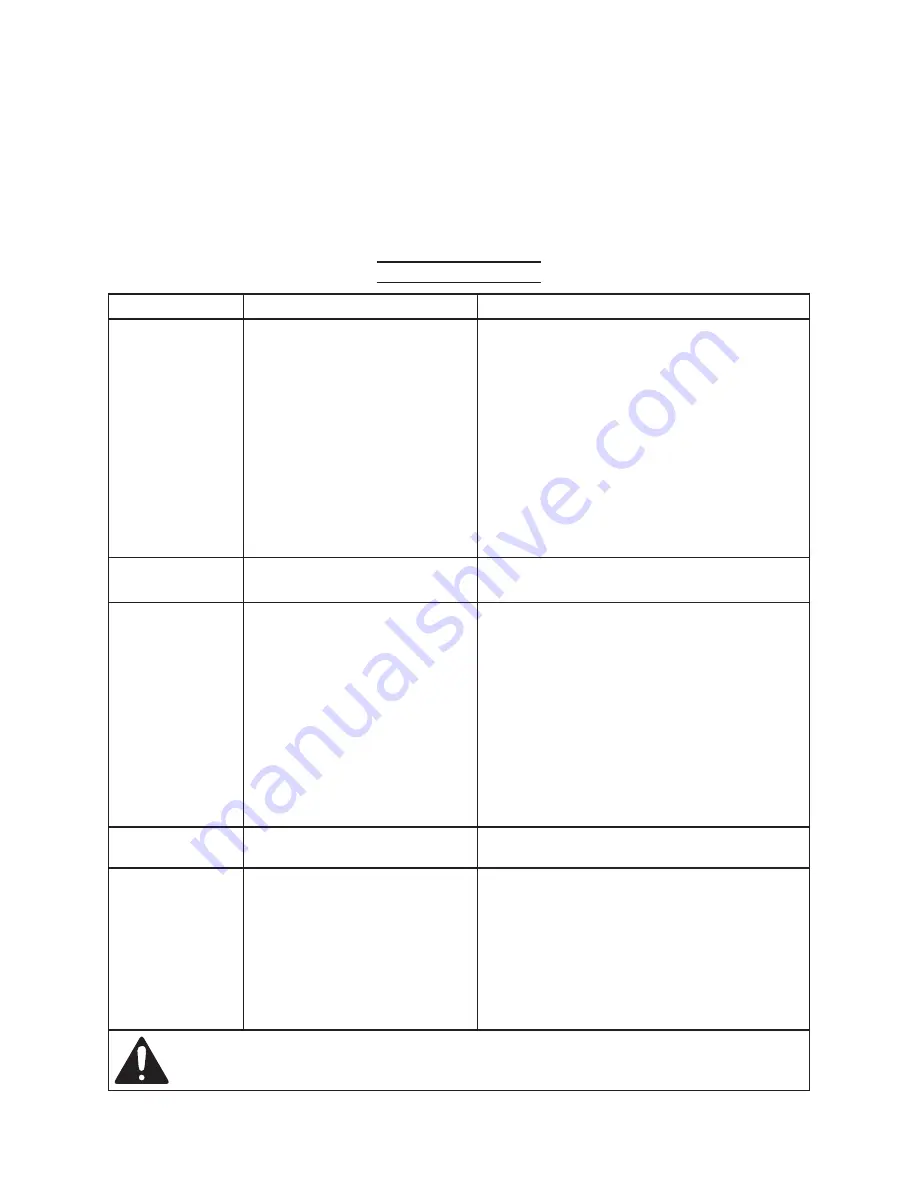
SKU 66872
For technical questions, please call 1-800-444-3353.
Page 13
Troubleshooting
Problem
Possible Causes
Likely Solutions
Insufficient
fastener depth.
1. Incorrect tool depth setting.
2. Not enough air pressure.
3. Incorrect lubrication or not
enough lubrication.
4. Blocked air inlet screen (if
equipped).
5. Mechanism contaminated.
1. Adjust depth setting, if available.
2. Check for loose connections and make
sure that air supply is providing enough air
pressure (PSI) to the tool’s air inlet.
Do not
exceed maximum air pressure.
3. Lubricate using air tool oil and grease
according to directions.
4. Clean air inlet screen of buildup.
5. Have qualified technician clean and lubricate
mechanism. Install in-line filter in air supply
as stated in Initial Set Up: Air Supply.
Fasteners drive
too deeply.
1. Incorrect tool depth setting.
2. Too much air pressure.
1. Adjust depth setting, if available.
2. Reduce air supply pressure (PSI).
Tool cycles
without firing
fastener.
1. Tool empty.
2. Incorrect fasteners used.
3. Magazine dirty or not
lubricated properly.
4. Insufficient air flow.
5. Nails jammed.
1. Fill with correct fasteners.
2. Empty, then fill with correct fasteners.
3. Clean and lubricate magazine and pusher.
4. Check for loose connections and make
sure that air supply is providing enough air
flow (CFM) and pressure (PSI) to the tool’s
air inlet.
Do not exceed maximum air
pressure.
5. Check the Magazine, remove Nozzle, and
clear bent or broken nails.
Frequent
jamming.
Incorrect fastener type.
Confirm fastener diameter, type, length, angle,
and collation type. Correct as needed.
Severe air
leakage.
(Slight air leakage
is normal,
especially on
older tools.)
1. Cross-threaded housing
components.
2. Loose housing.
3. Damaged valve or housing.
4. Dirty, worn or damaged valve.
1. Check for incorrect alignment and uneven
gaps. If cross-threaded, disassemble and
replace damaged parts before use.
2. Tighten housing assembly. If housing cannot
tighten properly, internal parts may be
misaligned.
3. Replace damaged components.
4. Clean or replace valve assembly.
Follow all safety precautions whenever diagnosing or servicing the tool.
Disconnect air supply before service.
out. Use a screwdriver to release
the jammed fastener by probing the
openings in the magazine.
3. Pull out the jammed fastener and the
remainder of the fastener strip that is
still in the magazine. Dispose of the
remaining fastener strip; it may be
bent or damaged in some other way.
4. If unable to clear jam using the meth-
od prescribed above, the tool should
be taken to a qualified service techni-
cian for proper servicing.