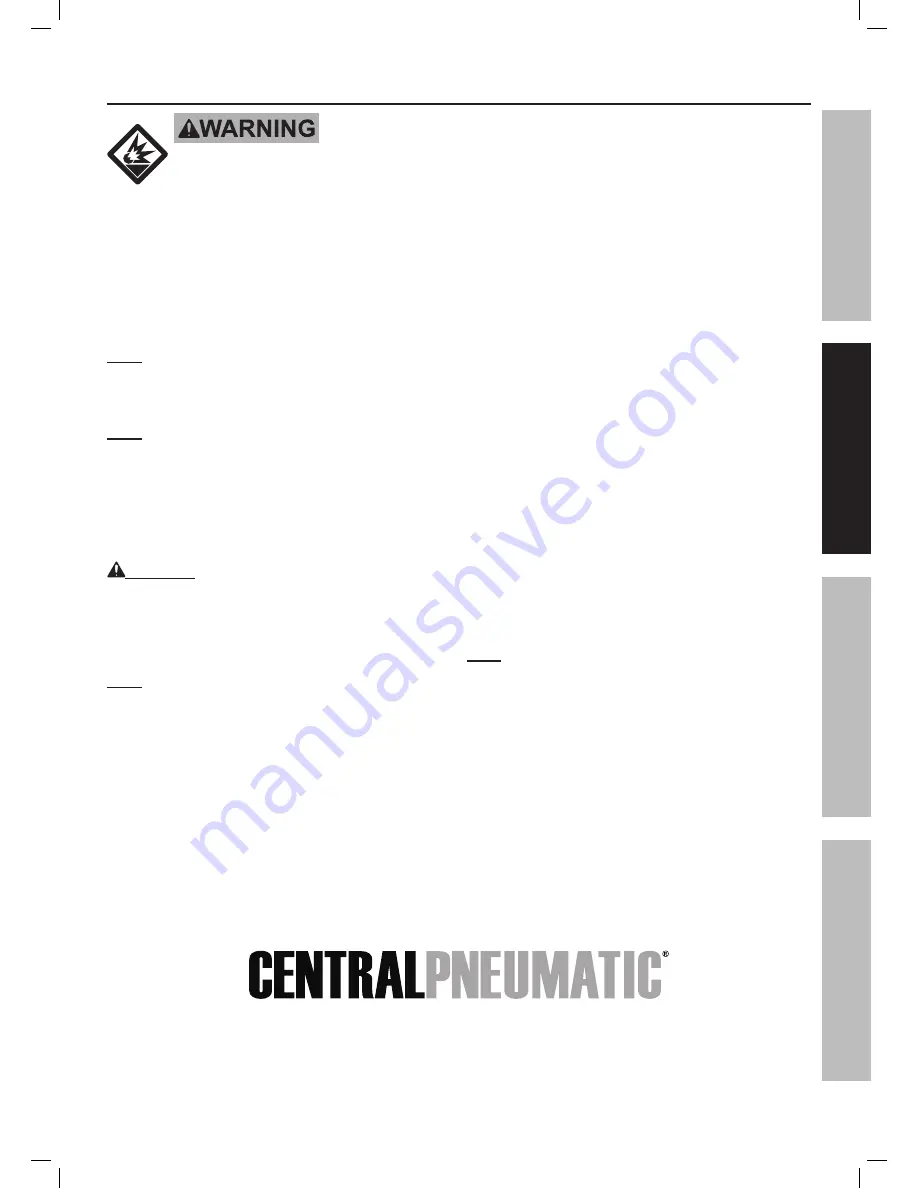
Page 9
For technical questions, please call 1-800-444-3353.
Item 67450
Air Supply
TO PREVENT EXPLOSION:
Use only clean, dry, regulated, compressed air to power this tool. Do not use oxygen,
carbon dioxide, combustible gases, or any other bottled gas as a power source for this tool.
1. Incorporate a filter, regulator with pressure gauge,
oiler, in-line shutoff valve, and quick coupler for
best service, as shown on Figure E on page 10
and Figure F on page 11.
An in-line shutoff
ball valve is an important safety device because
it controls the air supply even if the air hose
is ruptured. The shutoff valve should be a
ball valve because it can be closed quickly.
Note:
If an automatic oiler system is not used,
add a few drops of Pneumatic Tool Oil into
the airline connection before operation.
Add a few more drops after each hour of continual use.
Note:
This air tool may be shipped with a protective plug
covering the air inlet. Remove this plug before set up.
2. Attach an air hose to the compressor’s air outlet.
Connect the air hose to the air inlet of the tool.
Other components, such as a coupler plug
and quick coupler, will make operation
more efficient, but are not required.
WARNING! TO PREVENT SERIOUS INJURY
FROM ACCIDENTAL OPERATION:
Do not install a female quick coupler on the tool.
Such a coupler contains an air valve that will
allow the air tool to retain pressure and operate
accidentally after the air supply is disconnected.
Note:
Air flow, and therefore tool performance,
can be hindered by undersized air supply components.
3. The air hose must be long enough to reach
the work area with enough extra length to
allow free movement while working.
4. Release the tool’s trigger and empty its magazine.
5. Close the in-line safety valve between
the compressor and the tool.
6. Turn on the air compressor according to
the manufacturer’s directions and allow it
to build up pressure until it cycles off.
7. Adjust the air compressor’s output regulator
so that the air output is enough to properly
power the tool, but the output will not exceed
the tool’s maximum air pressure at any time.
Adjust the pressure gradually, while checking the
air output gauge to set the right pressure range.
8. The air pressure setting must not exceed job site
regulations/restrictions. The air pressure setting
must not exceed 90 PSI when being used with
workpieces that have a thickness of less than 1-3/4″.
9. Inspect the air connections for leaks.
Repair any leaks found.
10. If the tool will not be used at this time, turn off
and detach the air supply, safely discharge
any residual air pressure, and release the
trigger to prevent accidental operation.
Note:
Residual air pressure should not be present
after the tool is disconnected from the air supply.
However, it is a good safety measure to attempt to
discharge the tool in a safe fashion after disconnecting
to ensure that the tool is disconnected and unpowered.
SAFETY
OPERA
TION
MAINTENANCE
SETUP
Summary of Contents for 67450
Page 1: ......