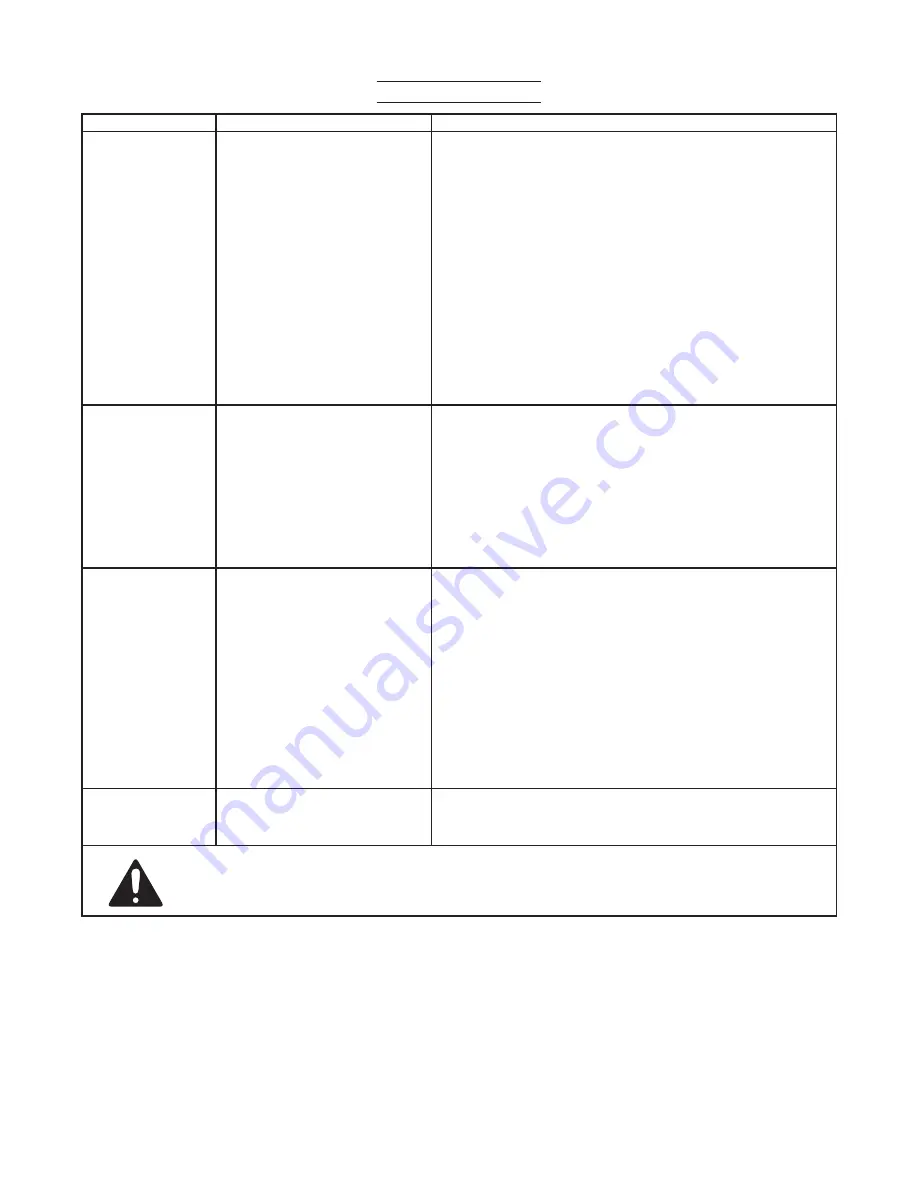
Page 15
For technical questions, please call 1-800-444-3353.
SKU 67708
troubleshooting
Problem
Possible causes
likely Solutions
Compressor does
not start or restart
1. Incorrect power supply.
2. No power at outlet.
3. Power cord not plugged in
properly.
4. Thermal overload switch
tripped.
5. Building power supply circuit
tripped or blown fuse.
6. Tank(s) already pressurized.
7. Cord wire size is too small or
cord is too long to properly
power compressor.
8. Compressor needs service.
1. Check that circuit matches compressor requirements.
2. Reset circuit breaker, or have outlet serviced by a qualified
technician.
3. Check that cord is plugged in securely.
4. Turn off Tool. Turn off Compressor and wait for it to cool down.
Press reset button. Resume operation.
5. Reset circuit or replace fuse. Check for low voltage conditions.
It may be necessary to disconnect other electrical appliances
from the circuit or move the compressor to its own circuit.
6. No problem. Compressor will start when needed.
7. Use larger diameter or shorter extension cord or eliminate
extension cord. See Recommended Wire Gauge for Extension
Cords in Safety section.
8. Have unit inspected by a qualified technician.
Compressor builds
pressure too slowly
1. Incorrect power supply.
2. Crankcase overfilled with oil or
oil too thick.
3. Working environment too cold.
4. Safety valve needs service.
5. Loose fittings.
1. Check that circuit matches compressor requirements.
2. Drain oil and refill to proper level with recommended oil.
3. Move unit to a warmer location. Check that recommended oil
is in crankcase.
4. Listen for air leaking from valve. If leaking replace with
identical valve with same rating.
5. Reduce air pressure, then check all fittings with a soap solution
for air leaks and tighten as needed. Do not overtighten.
Compressor not
building enough air
pressure
1. Filters need cleaning/replacing.
2. Crankcase oil too thick.
3. Check Valve needs service.
4. Compressor not large enough
for job.
5. Loose fittings.
6. Hose or hose connections not
adequate.
7. High altitude reducing air
output.
1. Check inlet and outlet filters. Clean and/or replace as needed.
2. Drain oil and refill to proper level with recommended oil.
3. Have technician clean or replace, as needed.
4. Check if accessory SCFM is met by Compressor. If
Compressor cannot supply enough air flow (SCFM), you need
a larger Compressor.
5. Reduce air pressure, then check all fittings with a soap solution
for air leaks and tighten as needed. Do not overtighten.
6. Replace with larger hose and/or hose connections.
7. You may need a larger compressor if you are situated in a high
altitude location.
High Oil
Consumption
1. Crankcase oil too thin.
2. Unit not on level surface.
3. Crankcase vent clogged.
1. Drain oil and refill to proper level with recommended oil.
2. Reposition unit on a level surface.
3. Clean Crankcase vent.
Follow all safety precautions whenever diagnosing or servicing the
compressor. disconnect power supply before service.