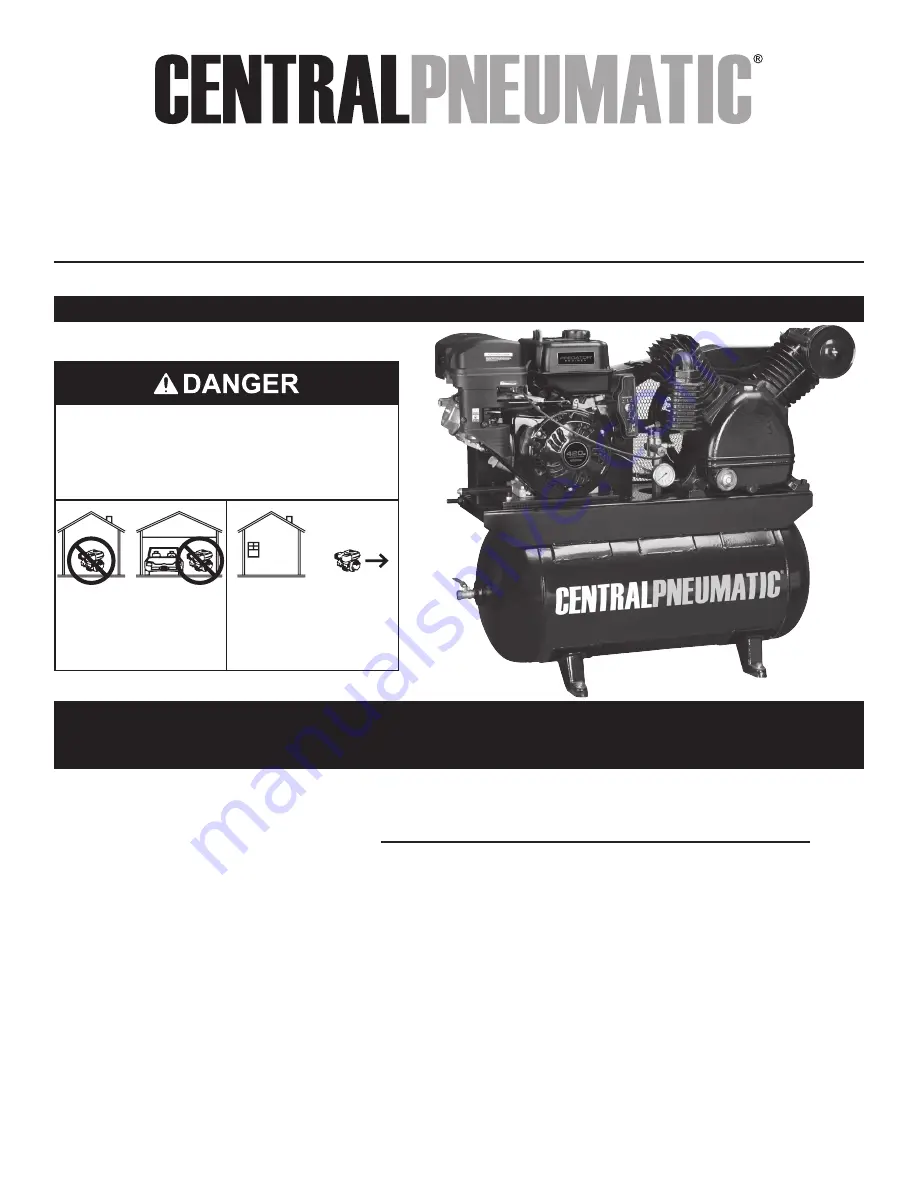
30 Gallon, 180 PSI
Gas Powered Two-Stage Air Compressor
67853 Air Compressor
Using an engine indoors CAN KILL YOU
IN MINUTES.
Engine exhaust contains carbon monoxide.
This is a poison you cannot see or smell.
NEVER use inside
a home or garage,
EVEN IF doors and
windows are open.
Only use OUTSIDE
and far away from
windows, doors,
and vents.
When unpacking, make sure that the product is intact and undamaged.
If any parts are missing or broken, please call 1-800-444-3353 as soon as possible.
Record Product’s Serial Number Here:
Note:
If product has no serial number, record month and year of purchase instead.
Note:
Some parts are listed and shown for illustration purposes only, and are not available individually
as replacement parts.
Visit our website at: http://www.harborfreight.com
Email our tech support at: tech@harborfreight.com
Copyright
©
2010 by Harbor Freight Tools
®
. All rights reserved. No portion of this manual or any artwork contained herein may be reproduced in any shape
or form without the express written consent of Harbor Freight Tools. Diagrams within this manual may not be drawn proportionally. Due to continuing
improvements, actual product may differ slightly from the product described herein. Tools required for assembly and service may not be included.
Manual Revised 11e
Summary of Contents for 67853
Page 2: ......
Page 19: ...Page 17 For technical questions please call 1 800 444 3353 Item 67853 Pump Assembly Diagram...
Page 21: ...Page 19 For technical questions please call 1 800 444 3353 Item 67853 Tank Assembly Diagram...
Page 53: ...3491 Mission Oaks Blvd PO Box 6009 Camarillo CA 93011 800 520 0882 www harborfreight com...