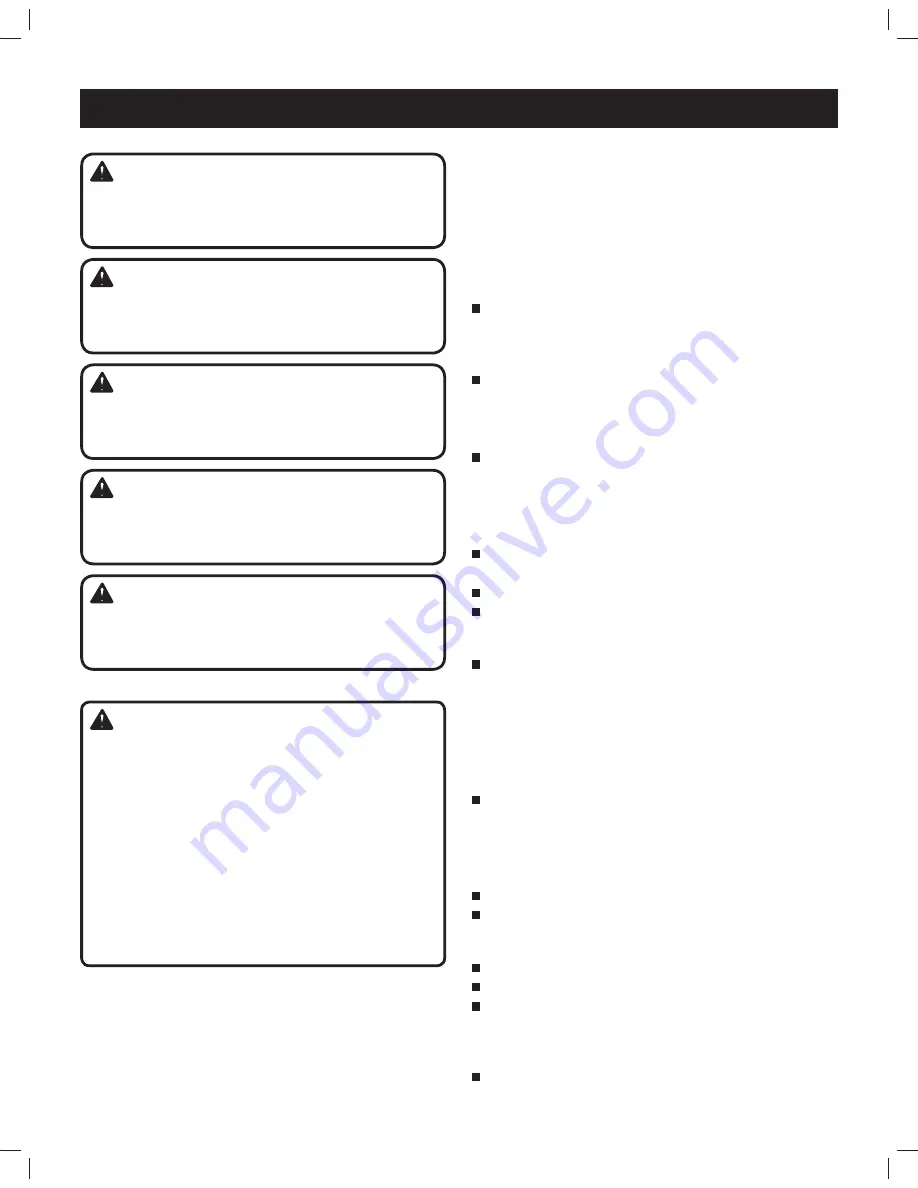
16
WARNING:
When servicing, use only identical Harbor Freight Tools
replacement parts. Use of any other parts may create a
hazard or cause product damage.
WARNING:
Always wear safety goggles or safety glasses with side
shields during power tool operation or when blowing
dust. If operation is dusty, also wear a dust mask.
MAINTENANCE
MAINTENANCE SCHEDULE
Refer to the
gas engine owner’s manual
for maintenance
procedures to be performed on the engine. If the unit is
used in an excessively dirty or dusty environment, check
and perform all maintenance procedures more often.
After First 100 Hours or First Month of Operation
(whichever occurs first)
Replace break-in lubricant with SAE 40W oil (refer to
Lubrication
).
Daily
Maintain lubricant level at the halfway point on the
sightglass. Discolored lubricant or a higher lubricant
level reading may indicate the presence of condensed
liquids (refer to
Troubleshooting
).
Humidity in the air causes condensate to form in the air
tank. Drain moisture from air tank(s) (refer to
Draining
the Tank
). Tank(s) subjected to freezing temperatures
may contain ice. Store the compressor in a heated area
before attempting to drain moisture from the tank(s).
Give compressor overall visual inspection and be sure
safety guards are in place.
Check for any unusual noise or vibration.
Check for leaks.
Weekly
The safety valve automatically releases air if the air
receiver pressure exceeds the preset maximum.
Check the safety valve before each use, following the
instructions found in
Checking the Safety Valve
. Pull
on the ring of the safety valves to make sure they are
operating correctly. Air pressure should escape when
the ring is pulled (refer to Fig. 4).
Check all pressurized components for rust, cracking or
leaking. Immediately discontinue use of the equipment
and relieve all system pressure if any of these problems
are discovered. Do not use the equipment until it has
been inspected and repaired by a qualified mechanic.
Clean the exterior surfaces of the compressor.
Check the air filter and replace if necessary.
Monthly
Check belt tension.
Check pulley retaining screws.
Check system for air leaks.
Every 3 Months or Every 300 hrs. of Operation
(whichever occurs first)
Change
lubricant.
WARNING:
Prior to performing any maintenance or repair, always
shut off the engine and remove the plug wire from the
spark plug.
WARNING:
Completely relieve the system of air pressure by pulling
the ring on the safety valve. Continue to pull the ring
until all air pressure escapes (Fig. 4).
WARNING:
Wait for the unit to cool before starting to service. Some
surface temperatures exceed 350°F when the unit is
operating.
WARNING:
Do not at any time let brake fluids, gasoline, petroleum-
based products, penetrating oils, etc., come in contact
with plastic parts. Chemical can damage, weaken or
destroy plastic which may result in serious personal
injury. Electric tools used on fiberglass material, wall-
board, spackling compounds, or plaster are subject
to accelerated wear and possible premature failure
because the fiberglass chips and grindings are highly
abrasive to bearings, brushes, commutators, etc.
Consequently, we do not recommend using this tool for
extended work on these type of materials. However, if
you do work with any of these materials, it is extremely
important to clean the tool using compressed air.