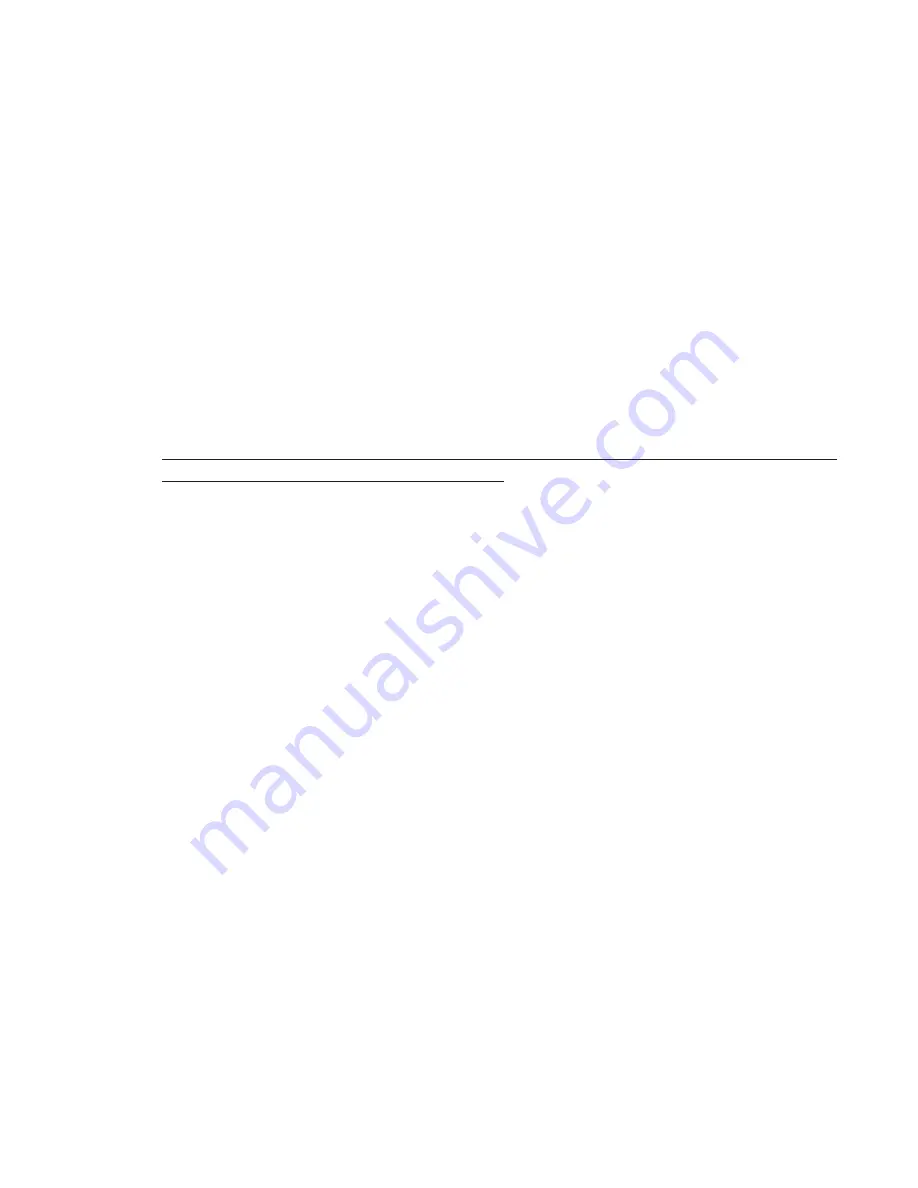
Page 5
SKU 93296
For technical questions, please call 1-800-444-3353
Operation (continued)
Note: Turn off your air compressor and disconnect the air hose when you are changing sockets.
After you attach the socket, attach the air hose and turn the air compressor on.
4.
Select the appropriate size 3/8” drive socket for your needs.
5.
Push and snap the socket (not included) onto the Anvil (6).
6.
Turn the Air Regulator (32) in the direction indicated by the H arrow on the Regulator to
increase the power. Turn it toward the L arrow to decrease the power.
Note: Set the Reverse Lever (38) to the left, so that the anvil turns clockwise (forward).
7.
Tighten the nut as tight as you can by hand.
8.
Place the socket (not included) over the nut you wish to tighten.
9.
Grip the Impact Wrench firmly with two hands and gently squeeze the Trigger (34).
Note: If the Impact Wrench cannot tighten the nut to your satisfaction, do not raise the air
pressure on the compressor over 90 PSI. Pressures above 90 PSI will strip the
workpiece and damage the tool, potentially causing the tool to fail, causing serious
injury. Use other appropriate methods and tools to tighten the nut.
10.
When the nut is tightened, release the Trigger (34). Turn off the air compressor and
disconnect the hose.
11.
If available, check the recommended torque specification for the nut. Use a torque
wrench to tighten the nut to the proper setting after using the Impact Wrench.
Loosening
Note: Set the Reverse Lever (38) to the right, so that the anvil turns counterclockwise (reverse).
12.
Place the socket (not included) over the nut you wish to loosen.
13.
Grip the Impact Wrench firmly with two hands and gently squeeze the Trigger (34).
Note: If the Impact Wrench cannot loosen the nut, do not raise the air pressure on the
compressor over 90 PSI. Do not attempt to loosen the nut with the Impact Wrench. Use
other appropriate methods and tools to loosen the nut.
14.
When the nut is loosened, release the Trigger (34). Turn off the air compressor and
disconnect the hose.
15.
If needed, remove the nut from the socket.
Refer to the illustration on page 6, and the Assembly Drawing on page 8.