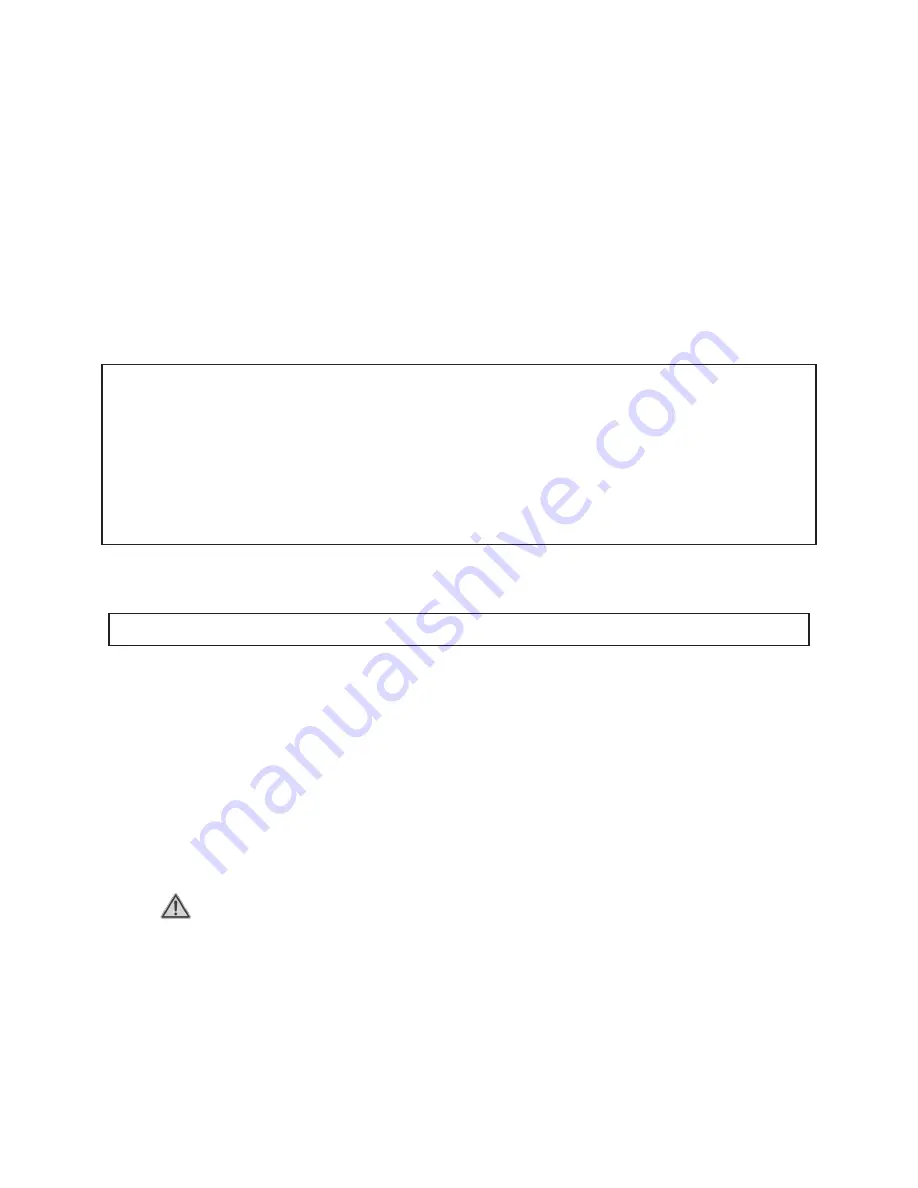
Anytime any maintenance or repairs are done, FIRST:
1.
Disconnect the Nailer from its air supply.
2.
Empty the Magazine Assembly (73) completely.
3.
Attempt to fire the Nailer into a piece of scrap wood to ensure that it is
disconnected and is incapable of firing any Nails.
4.
Always leave the Magazine Assembly (73) open during maintenance. The
Magazine is spring loaded, and may cause parts or a Nail to fly out of the Nailer.
7.
Make sure the Nose (40) moves freely.
8.
Reload the Nailer with Nails. Then, reconnect the air supply hose to the tool.
9.
Press the Nose (40) against a piece of scrap wood, and test fire the Nailer several
times while checking for proper operation. If the Nailer is properly firing, you
may continue using the tool. If the tool fails to perform properly, immediately
discontinue use and have the tool repaired by a qualified service technician.
10.
When finished working, disconnect the air supply. Remove the Nails. Then,
store the Nailer in a clean, dry, safe location out of reach of children.
INSPECTION, MAINTENANCE, AND CLEANING
1.
Inspect the air supply Screen that is located in the End Cap (84) before each
use, and clean or replace as necessary. Dirt and water in the air supply Screen
are major causes of pneumatic tool wear. Use a filter in the compressed air
system for better performance and longer tool life. The filter must have adequate
flow capacity for the specific application.
2.
Clean the external parts of the Nailer with a clean cloth and mild detergent or
non-flammable solvent. Then, dry.
3.
Store the tool in a clean, dry, safe location out of reach of children.
4.
CAUTION: All maintenance, service, or repairs not listed in this manual
are only to be attempted by a qualified service technician.
SKU 93760
For technical questions, please call 1-800-444-3353
PAGE 10