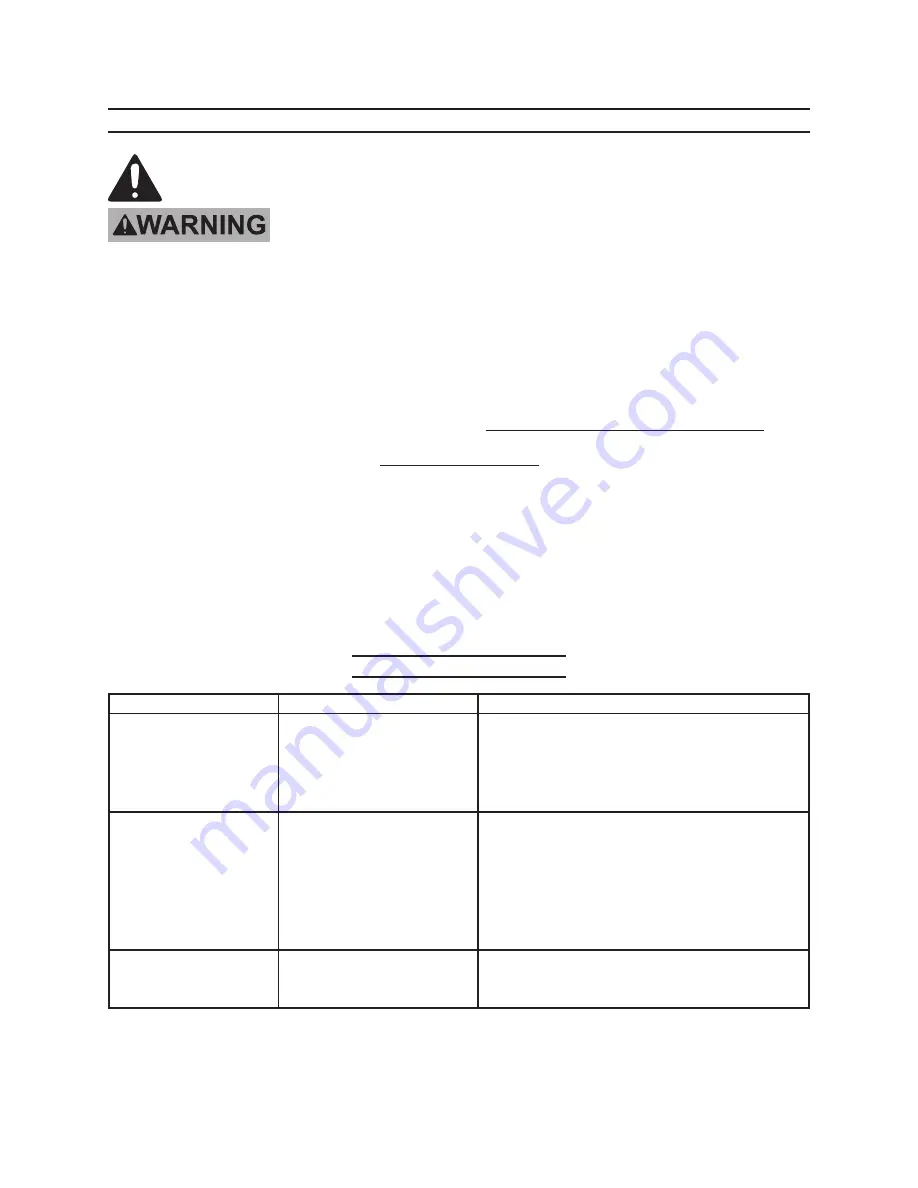
SKU 95498
For technical questions, please call 1-800-444-3353.
Page 12
INSPECTION, MAINTENANCE, ANd CLEANING
Procedures not specifically explained in this manual must be performed
only by a qualified technician.
TO PREVENT SERIOuS INjuRY FROM ACCIdENTAL
OPERATION:
Turn the Power Switch of the tool to its “OFF” position and unplug the
tool from its electrical outlet before performing any inspection,
maintenance, or cleaning procedures.
Before each use,
1.
inspect the general condition of the Air Compressor. Check for
loose screws, misalignment or binding of moving parts, cracked or broken parts,
damaged electrical wiring, loose air fittings, and any other condition that may affect
the safe operation of the Compressor. If abnormal noise or vibration occurs, have
the problem corrected before further use.
do not use damaged equipment.
Before each use,
2.
check the compressor oil level in the Oil Sight Glass (22). If
necessary, fill the crankcase of the Air Compressor with the proper amount and
type of compressor oil.
daily,
3.
purge the Air Tanks (51) of all air and moisture to prevent corrosion. To do
so, slowly and carefully unscrew (no more than four threads) the Tank Drain Valve
(52) until the compressed air and condensation begins to be released from the
Tanks. Allow sufficient time for all of the air and condensation to escape from the
Tanks. Then, firmly re-tighten the Drain Valve.
TROuBLESHOOTING
Problem
Possible Cause
Possible Solution
Compressor will not
start.
Blown fuse or circuit
1.
breaker tripped.
Loose electrical
2.
connections.
Bad capacitors.
3.
Replace or reset fuse/circuit breaker.
1.
Plug Compressor into a working, 120 volt,
2.
grounded, electrical outlet.
Replace capacitors.
3.
Low pressure.
Restricted air filter.
1.
Defective check valve.
2.
Air leak in safety valve.
3.
Defective valve plate.
4.
Replace air filter.
1.
Have a qualified service technician replace
2.
check valve.
Check valve by pulling on ring. If condition
3.
persists, have a qualified service technician
replace valve.
Replace valve plate.
4.
Safety valve releasing.
Defective pressure
1.
switch.
Defective safety valve.
2.
Have a qualified service technician replace
1.
pressure switch.
Replace safety valve.
2.