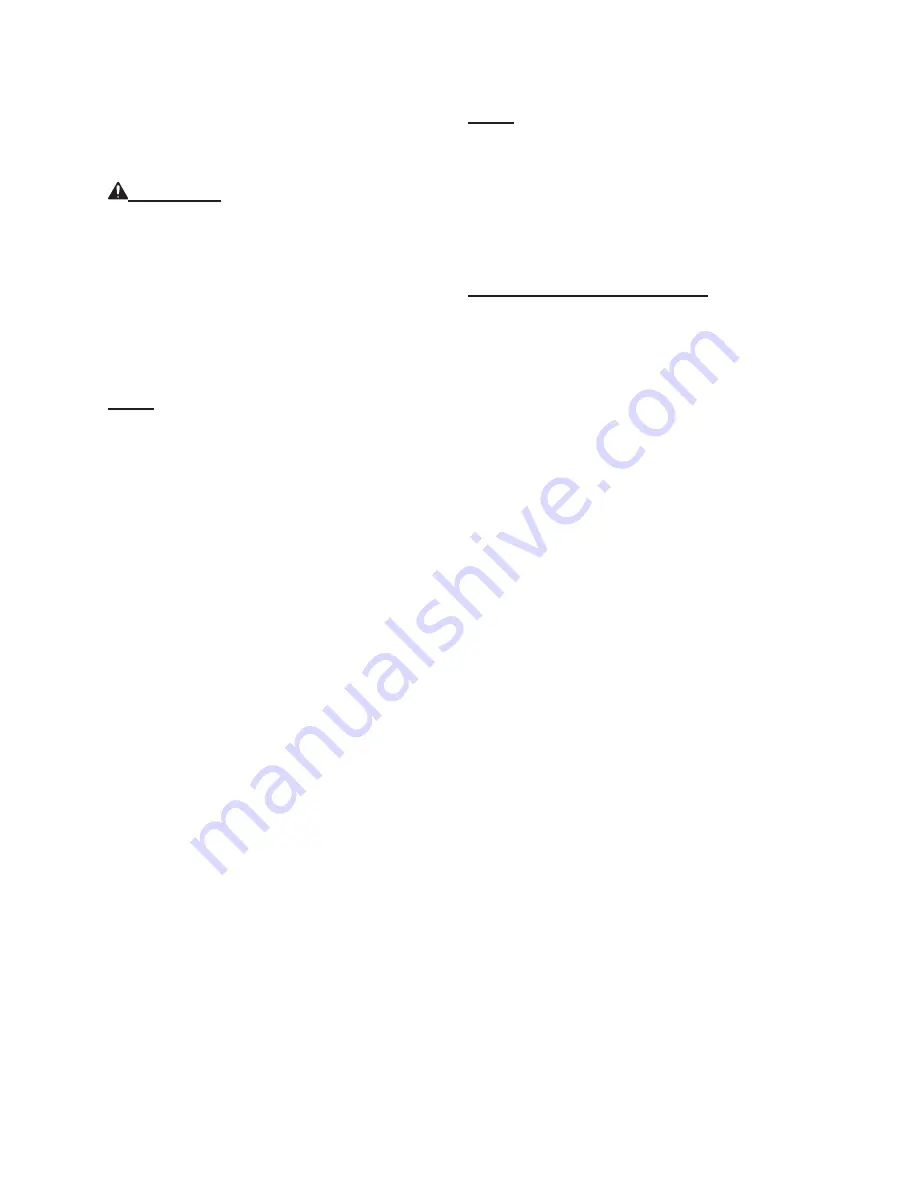
SKU 98917
For technical questions, please call 1-800-444-3353.
Page 8
ponents, such as a connector and
quick coupler, will make operation
more efficient, but are not required.
WARNING! TO PREVENT SERIOUS
INJURY FROM ACCIDENTAL
OPERATION:
Do not install a female quick
coupler on the tool.
Such a coupler
contains an air valve that will allow
the air tool to retain pressure and
operate accidentally after the air
supply is disconnected.
Note:
Air flow, and therefore tool perfor-
mance, can be hindered by under-
sized air supply components.
3. The air hose must be long enough
to reach the work area with enough
extra length to allow free movement
while working.
4. Close the in-line safety valve be-
tween the compressor and the tool.
5. Turn on the air compressor according
to the manufacturer’s directions and
allow it to build up pressure until it
cycles off.
6. Adjust the air compressor’s output
regulator so that the air output is
enough to properly power the tool,
but the output will not exceed the
tool’s maximum air pressure at any
time. Adjust the pressure gradually,
while checking the air output gauge
to set the right pressure range.
7. Inspect the air connections for leaks.
Repair any leaks found.
8. If the tool will not be used at this time,
turn off and detach the air supply
and safely discharge any residual air
pressure.
Note:
Residual air pressure should not be
present after the tool is disconnected
from the air supply. However, it is a
good safety measure to attempt to
discharge the tool in a safe fashion
after disconnecting to ensure that the
tool is disconnected and unpowered.
To Attach An Air Connector:
1. Attach a 1/4” Connector (not
included) to the Air Plug (83) prior to
operation.
2. Wrap about 3” of pipe thread seal
tape (not included) onto threads of
the Connector before attaching it to
the Air Plug.